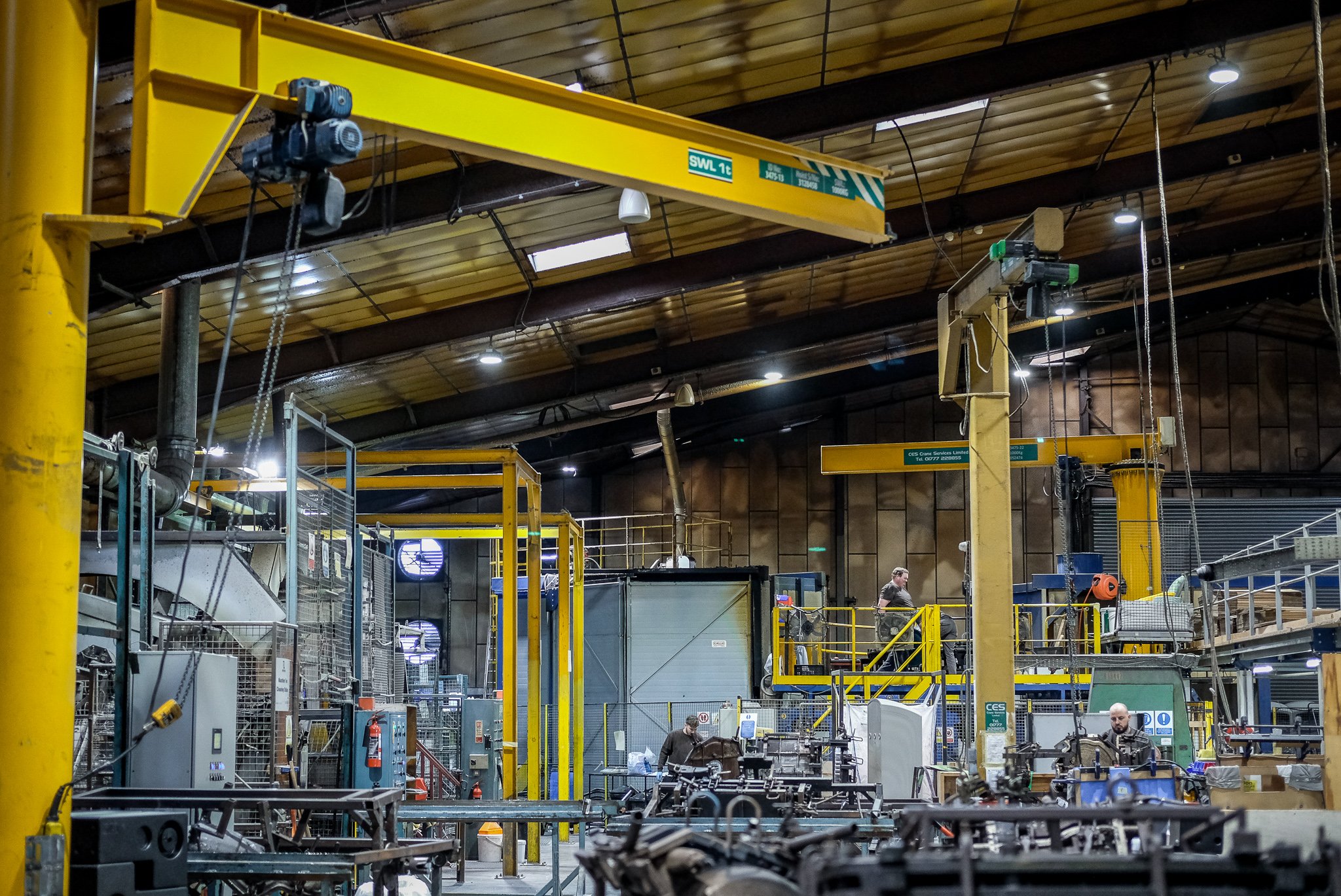
Blow Moulding vs Rotomoulding
Rotomoulding (or rotational moulding) is a manufacturing process where a hollow mould is filled with ground plastic powder. The process begins with pouring a pre-measured weight of plastic ground powder into a mould, which is then closed and held shut with fitted bolts or clamps. The mould is then sent into an oven where it rotates around two axes. This can be bi-axil or a rock and roll motion. As heat is transferred through the mould, the plastic powder begins to melt and build up layers of plastic around the mould’s surface.
When all of the powder is distributed and the product has taken its desired shape, the mould is transferred out of the oven into precooling and then into the cooling chamber. As the rotation continues, the mould is cooled using air fans and additional water cooling if needed. Throughout this process, the powder solidifies into its final shape. At this point, the mould can be opened, and the product is removed before it is passed over to the finishing team. At this final stage, the finishing team will trim down any edges left by the mould and fit additional parts to complete the product.
At Rototek, we have over three decades of experience in technical rotomoulding and our dedicated team offer a complete service, from collaborating with you on your initial design concept for the product to finishing the product. Our expertise lies in optimising the product’s design for rotational moulding and we can work independently or with your design team to achieve this. We have the capability to manage a wide range of projects, from simple to highly complex designs. Across our two production sites, we rotomould over 100,000 products per year ranging from small water containers to large 7-metre mouldings. Across our sites, we utilise over twenty machines, including advanced rotomoulding and robotics technology.
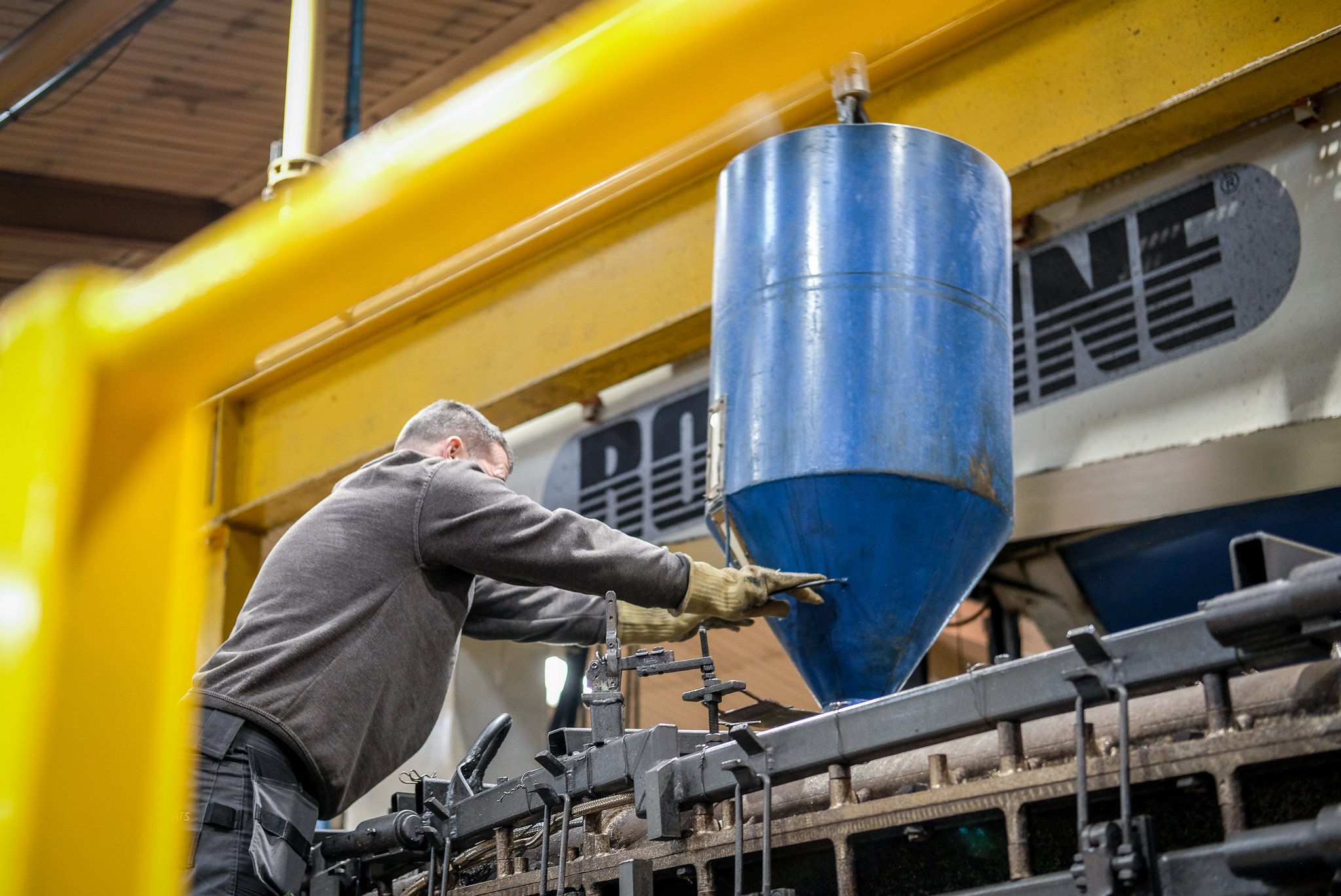
Introduction to Blow Moulding
There are a few main blow moulding processes: extrusion, injection and stretch. Extrusion blow moulding is the most common of the three. To start this blow moulding process, plastic pellets must be pre-melted. The pellets are then extruded into a hollow molten tube that is mechanically clamped into the product mould. Compressed air is then added into the tube, which causes the molten pellets to expand and take the shape of the mould. The cooling stage is rapid – once the mould has cooled down (the plastic has solidified and taken its final moulded shape), the mould is opened, and the final product is released ready for the next stage of the process.
Common products made using blow moulding include various plastic bottles and plastic containers, a lot of packaging for cosmetics and toiletries are made using this method including automotive fuel tanks, medical storage containers along with many household cleaning product containers and industrial drums and tanks.
Key Differences Between Blow Moulding and Rotomoulding
A key difference between the blow moulding and rotomoulding methods is the cycle time needed for the manufacturing process. Blow moulding cycles can be quite a lot shorter than most rotomoulding processes, which is why rotomoulding is better suited for more complex mouldings that perhaps require inserts and graphics, along with stringers for spreading loads. Rotomoulding is therefore suited to products that require more attention to detail in their manufacturing process, whereas blow moulding is more suited to less complex product shapes.
The wall thickness of rotomoulded products has the capacity to be thicker than blow moulded products. The moulds used for the blow moulding manufacturing process tend to be more expensive than those used for rotomoulding, but the lifespan of the moulds used for blow moulding tend to be longer.
Different products are more suited to different manufacturing processes. In general, larger, more complex, thicker-walled products are more suited to the rotomoulding process, whereas smaller, simpler products are more suited to the blow moulding process.
Advantages of Rotomoulding
A key advantage of rotomoulding is the design flexibility and complexity, making this manufacturing process more appropriate for more detailed projects. Examples include; indoor and outdoor furniture, sailing dinghies, tanks and bollards. At Rototek, our skilled design team are on hand to fully create your concept, or work alongside your design team.
Another advantage of rotomoulding is that it can create stronger, more durable products, which are capable of having thicker walls than if the product was blow moulded. Rotomoulding is also suitable for mouldings of all sizes, from small 1-litre water containers to large 7-metre sailing dinghies, although less suitable to micro products such as cosmetic packaging. In terms of materials, you can use polyethylene, polypropylene, thermoplastic elastomer, and nylon with blow moulding, as long as the material is in a powdered form.
The main advantage of working with Rototek on your project is our unique approach to optimising designs for rotomoulding. Leveraging our three decades of experience, we use Computer Aided Design (CAD) to create 3D models and then a prototype of your product, allowing us to evaluate the design’s functionality to ensure it performs as intended in real-world conditions.
Advantages of Blow Moulding
The key advantage of blow moulding is the cost-effectiveness for producing large volumes of product, for example thousands of units of cosmetics packaging. On the other hand, rotomoulding is more appropriate for larger, more technical mouldings. Blow moulding is also more suited to the production of smaller, more generic, non-technical products. For example; watering cans, small plastic containers and bottles and household cleaning product containers.
Another advantage of blow moulding is the speed of production. As the cycle time is shorter, you can mould more products in a shorter time frame compared to rotomoulding. However, this often means that the minimum run quantity for a product is much higher.
Although the moulds used within blow moulding are more expensive compared to rotomoulding, the life of these moulds are longer. As with rotomoulding, you can use polyethylene, polypropylene, thermoplastic elastomer and nylon with blow moulding, as long as the material is in pellet form. As with rotomoulding, there is the opportunity to add inserts and graphics to your product post-moulding.
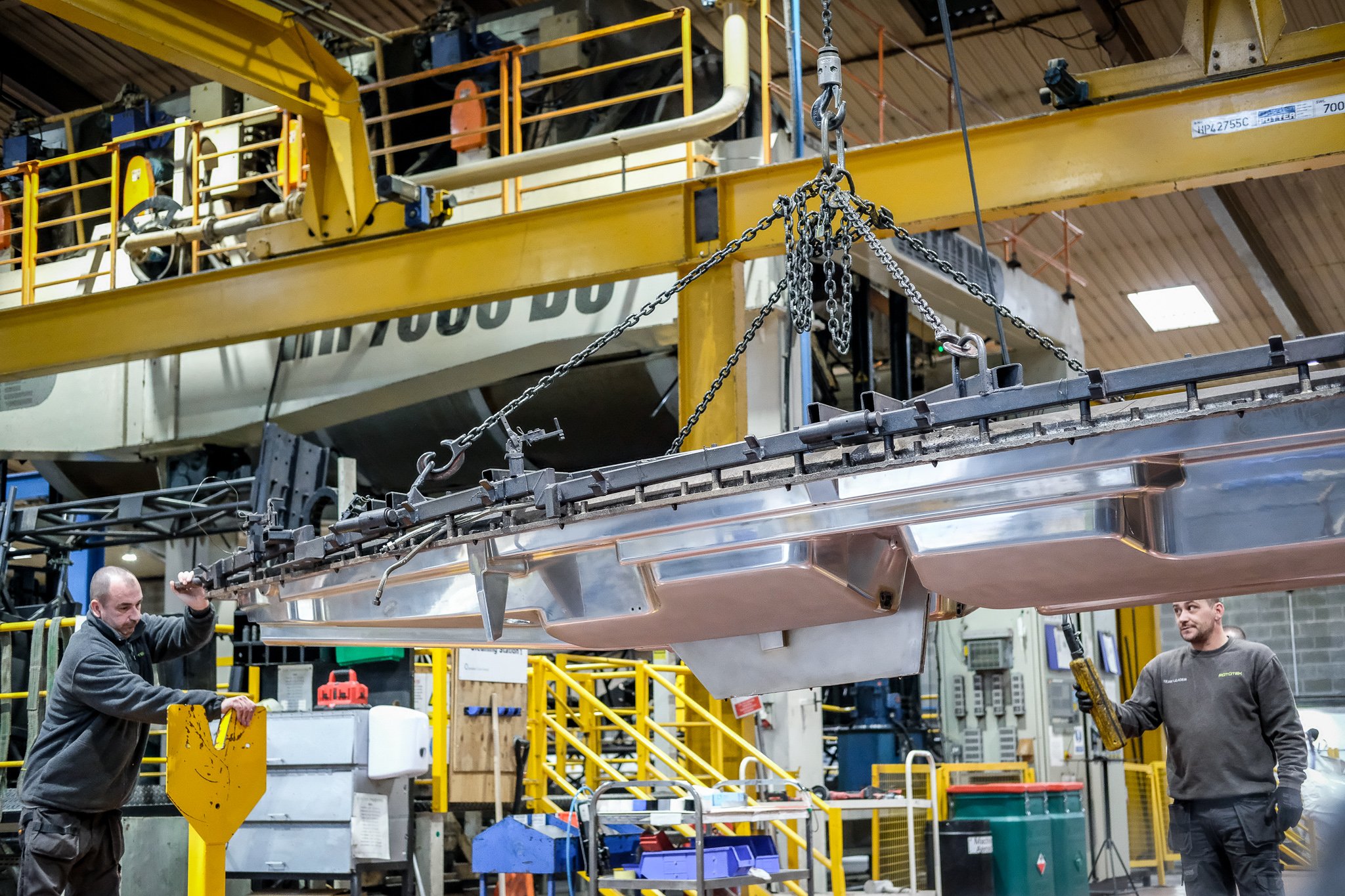
Rototek’s Service
Our service starts with your idea. At the outset of any project, we engage closely with our clients to understand their needs and vision. Once we have a firm concept, our experienced design team will utilize CAD to create 3D models of your product, either fully creating your concept or working in collaboration with your designers. Once we have evaluated the design’s functionality and made any necessary adjustments, we select the right tool making partner for your project.
Once the mould is signed off and we are ready to start production, our skilled operatives will oversee the manufacturing process across one of our two Nottinghamshire based sites. Once your product emerges from production, it is handed over to our finishing team who will add any finishes touches such as fitting components and additional detailing. Once your product has passed all of our inspections and meets our high ISO 9001 accredited quality standards, it is prepared for delivery. We can ship your products directly to your customers, offering a range of contracts to suit your needs.
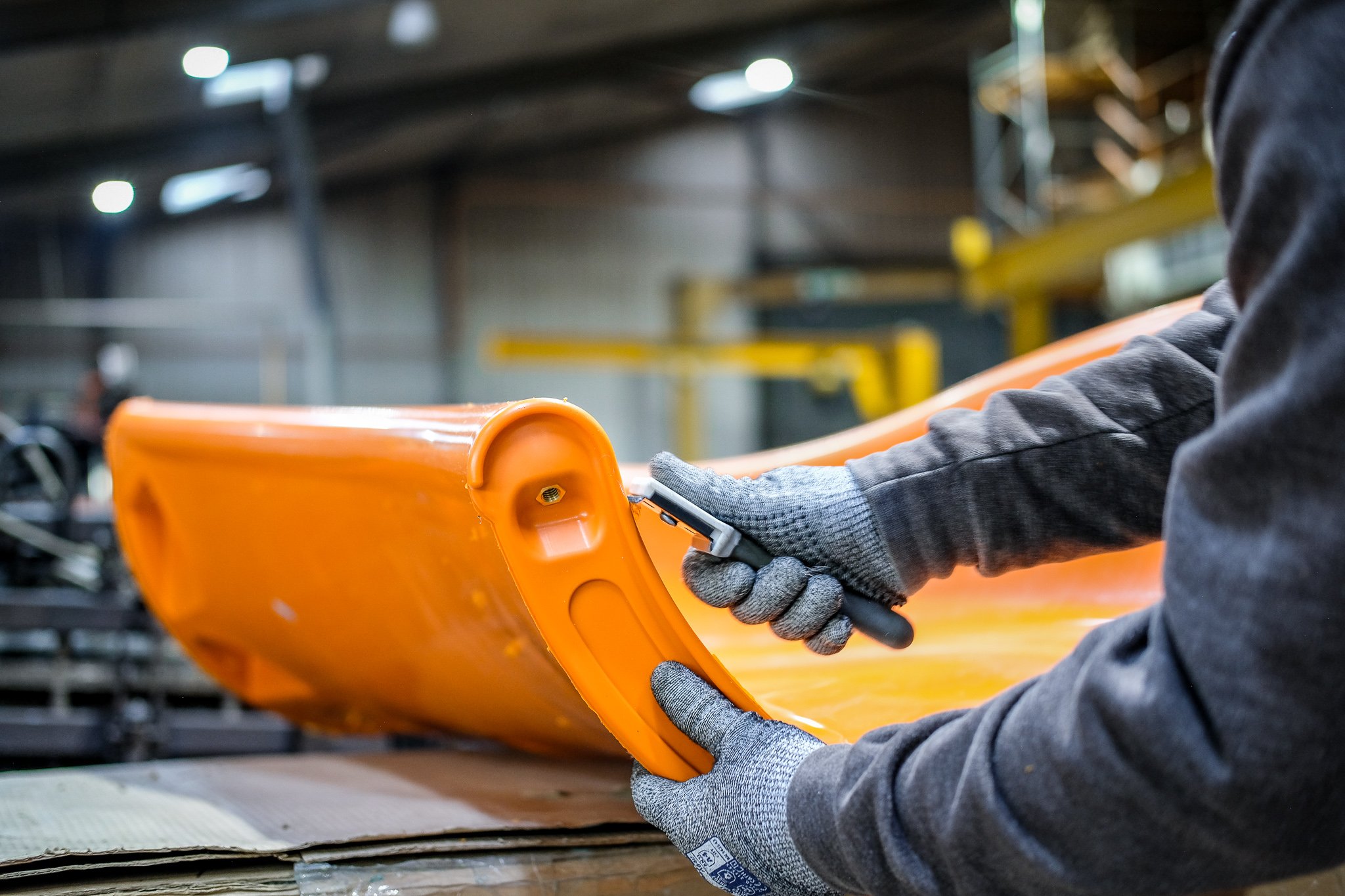
Why Choose Rototek
When you choose Rototek, you are choosing three decades of technical rotomoulding expertise with a renowned leader in the industry. Our skilled team will be with you every step of the way from the concept and design stage, right through to ensuring your products reach your customers on time. Our team holds the technical skills required to design and manufacture your product, evolving your original idea to ensure it benefits from the rotomoulding manufacturing process. Our approach is not just about meeting expectations but exceeding them, ensuring each client receives a product that truly reflects their vision and requirements.
As a company, we champion innovation, and our mission statement is ‘shaping the future through technical innovation, to provide our partners with a more sustainable manufacturing service.’ We are focused on investing in more sustainable production methods in our newest factory, where we are focusing on collaborating with new clients who share our vision of a more sustainable future for the manufacturing industry. We are investing in innovative technology which reduces our energy consumption, with our goal being to move away from carbon intensive production methods. Alongside the bigger picture projects, we are making day-to-day improvements on site such as reducing our waste and using more recycled materials within the products that allow this. We believe this is our point of difference within our industry - our team are shaping the future of manufacturing.
With over twenty machines ranging from rock & roll and bi-axial carousel to electrically heated tooling, we are working 24 hours a day, 5 days a week to bring your idea to life. Our wide range of machines increases our design capabilities. For example, bi-axial machines create uniform wall thickness, whereas rock & roll machines will allow thicker and thinner areas within the product. Our diverse product capabilities range from smaller furniture and containers to large 7-meter mouldings - we have the capability to mould it all. Examples include; oil and water tanks, grit bins, bollards, outdoor and indoor furniture, marine applications, pump chambers/housing, mudguards, bumpers, portable toilet parts, containers, planters, privacy screenings... the list goes on! Our design team loves a challenge and will collaborate with you to bring your idea to life.
With Rototek, you are not just choosing a rotomoulding service. You are partnering with a leader in innovative and sustainable manufacturing solutions.
Contact us to find out more.