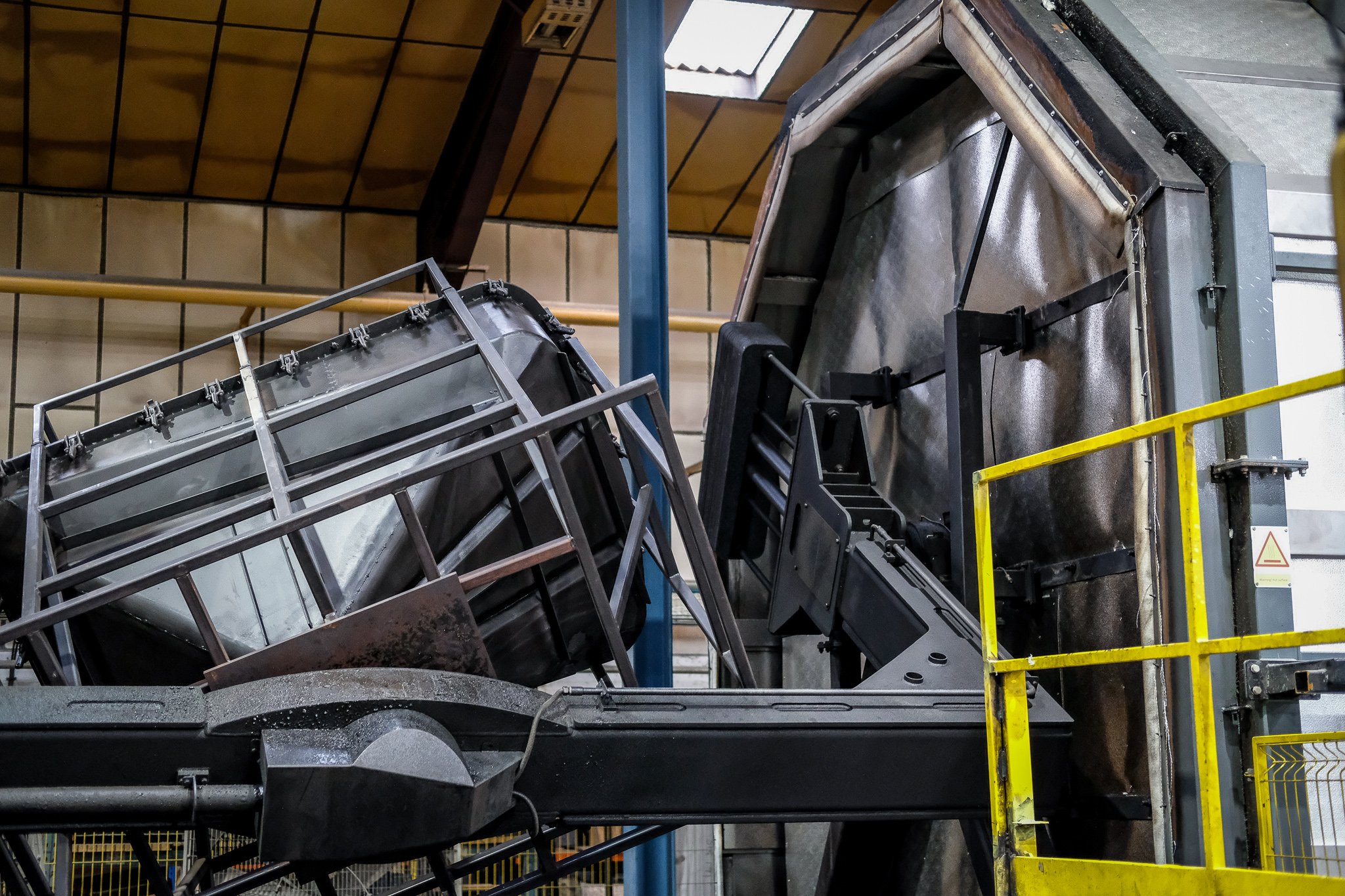
Injection Moulding VS ROtoMoulding
Designers of plastic parts and products can employ a broad range of techniques to achieve their desired end product and decisions on the most suitable method centre around cost, quality, versatility, and production timelines.
Injection moulding is classed as the most abundant manufacturing process. However, with the innovations coming through in rotational moulding, also known as rotomoulding, this is now challenging as a key manufacturing process for products made via plastic moulding.
At Rototek, we utilise the many benefits that rotomoulding presents but both manufacturing processes have their unique advantages. We’ll examine how these techniques compare in terms of design freedom, tooling costs, and material choices.
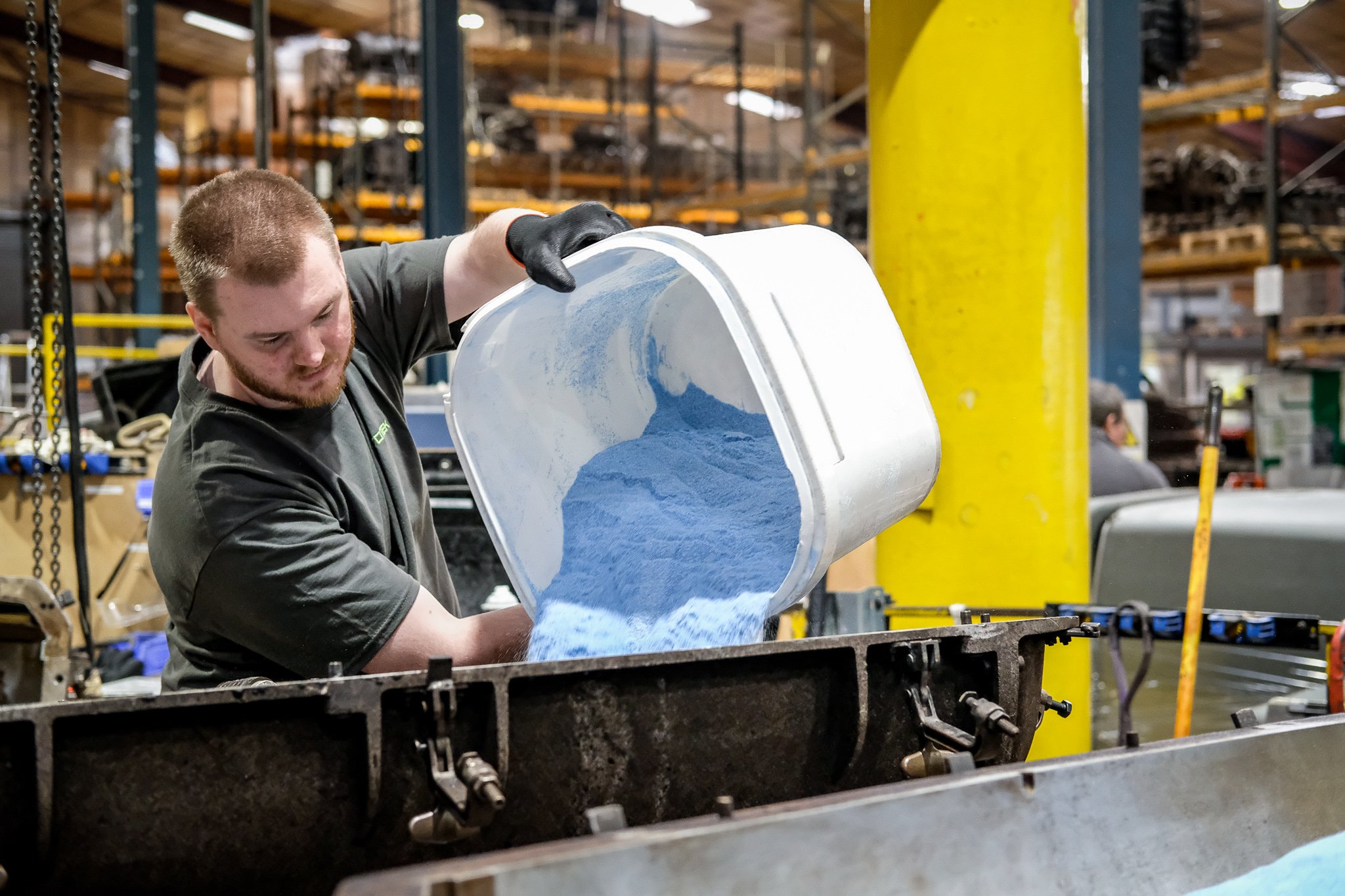
Rotomoulding
The rotomoulding process involves loading a mould with a pre-measured amount of polymer powder or resin. The tool is mobile and is sent into the oven. The tool is then heated in the hot air flow from the oven while it rotates on two perpendicular axes. The constant rotation, from which the process takes its name, allows the polymer to melt and coat the interior of the mould surface evenly. This means that, unlike products manufactured using injection moulding, there are no ‘stress points’ in the final object which could make it susceptible to breakages under pressure.
The mould is then removed from the oven and cooled, typically with fans or water, resulting in the polymer solidifying into the desired shape. Once completed, the finished product can be removed (demoulded) by simply opening the mould.
Injection moulding
Injection moulding is often considered to be the workhorse method in the world of manufacturing, with more than 30 per cent of all products worldwide made using this process. Due to the expensive equipment required, as we will explore later, it is typically applied to mass production of plastic parts due to economies of scale.
The method isn’t dissimilar to rotomoulding, but the injection moulding tool is stationary, and rotomoulding doesn’t require pressure. This pressure is a key element of the injection moulding technique.
The process begins by melting thermoplastic pellets in a heated barrel. The molten plastic is then injected into the tool cavity, usually under hydraulic pressure. The mould is cooled to allow the plastic to harden into the required form, before being ejected once fully cooled. The end product requires little to no post-processing. Whilst the injection moulding and rotomoulding processes are not dissimilar, there are a few notable differences which will dictate which method is right for your project.
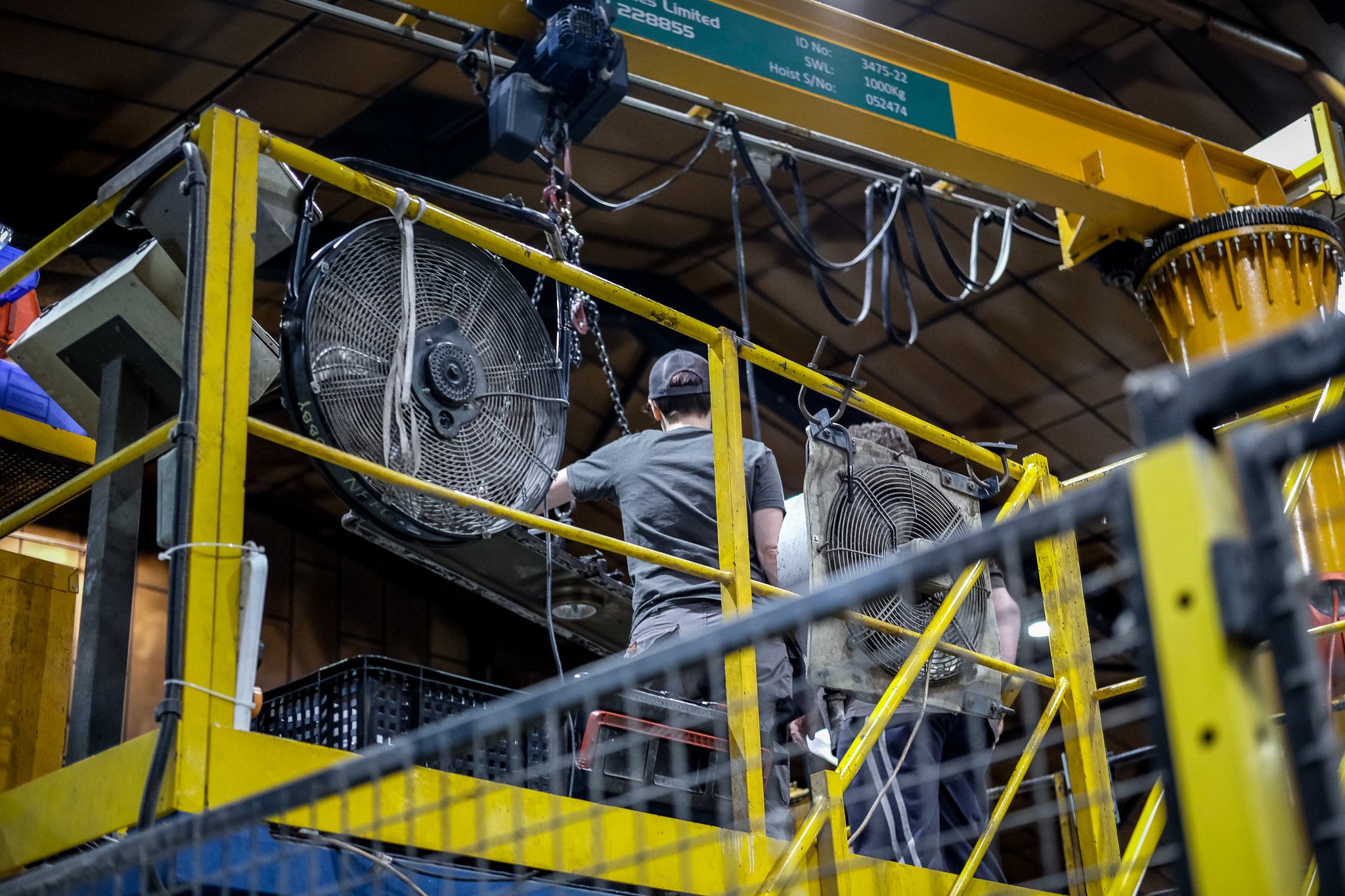
How do the processes compare?
Differences in materials used
Firstly, let’s look at the materials involved in each technique. Rotomoulding largely uses polyethylene (PE) – a light, versatile resin which is recyclable and can have several different crystalline structures, including linear low-density (LLDPE) and high-density (HDPE).
Polyethylene is the most widely used thermoplastic in the world, accounting for around 30 per cent of all plastics, owing to its low cost, versatility, easy processability, excellent electrical insulation properties, toughness, flexibility and non-toxicity, to name a few properties.
Rotational moulding can also utilise materials such as polypropylene (PP), PVC, and nylon, but this is less common.
Injection moulding, on the other hand, utilises a broader range of thermoplastics, including:
Acrylonitrile Butadiene Styrene (ABS) – an opaque thermoplastic known for its tough and impact resistant properties. It’s commonly used in electronic housings, auto parts, pipe fittings and, importantly, Lego toys!
Polycarbonate (PC) – a transparent thermoplastic which is lightweight and durable. It’s often used as an alternative to glass, in roofing or safety eyewear.
Polyamide – a synthetic polymer made of petroleum-based plastics, which is wear-resistant and low cost.
Polystyrene – a lightweight, versatile synthetic polymer commonly used in packaging and construction due to its insulation and protective properties.
Injection moulding can process both thermoplastic and thermosetting polymers. Whilst thermoplastic can be remelted and remoulded once set due to its low melting point, and offers better dimensional stability, thermosetting plastic cannot be reformed once hardened, making it typically stronger.
Tooling costs
Injection moulds are typically made of stainless steel, P20 steel or H13 steel, all of which are expensive and are not easily altered once created. This can become an issue if a customer requires a design change such as adding extra material to a part. This is extremely challenging with this type of material and in many cases may mean scrapping the tool entirely and starting over.
In contrast, due to the lack of pressure needed during this process, rotational moulds tend to be comprised of mild steel or aluminium. This makes them significantly less expensive and easier to change. Rotomoulding tools are usually between 2-3mm thick, depending on the toolmaker.
Production times and costs
Looking at rotomoulding first, due to the nature of its heating and cooling cycles, the process was historically restricted to only one or two cycles completed each hour. This limits production volumes and can result in extended production timelines. However, with the introduction of electrically heated tooling and full integrated robotic production cells, this can now be scaled up to bring the process production times and energy usage down. That said, the time needed to reach the production stage is typically shorter than in injection moulding, which can be several months depending on the project.
The tooling and material costs involved in rotational moulding are lower, making it a cost-effective method for small to medium runs. This means that it can produce low to medium batch numbers, which may better suit the customer’s needs and result in less waste.
The production times in injection moulding are much faster, producing large quantities of product quickly. This means that although injection moulding has higher initial tooling costs, when produced at high volumes it offers lower per-part costs than rotomoulding. This also makes it less suitable for projects that require smaller runs.
Complexity and design flexibility
Rotational moulding has high design flexibility, allowing for the creation of complex shapes, sizes and features that are impossible to achieve with other manufacturing methods. Dimensional stability also supports the production of large, hollow parts, making it ideal for storage vessels, for example. Additionally, the process’s flexibility facilitates the easy incorporation of features like inserts, threads, and double walls.
The nature of the rotomoulding process also means that particularly distinctive shapes and other complex geometries can be made in a single, seamless piece, rather than built from several individually manufactured components. As a result, the finished object doesn’t have as many stress points, which reduces the risk of fractures.
Injection moulding, on the other hand, is a high precision method far better suited to repeatability, allowing it to produce high volumes of identical parts, which is a huge advantage in terms of delivering consistency on a large scale. Injection moulders can achieve designs accurate to within +/- .001 inches – results which are consistent across multiple production runs.
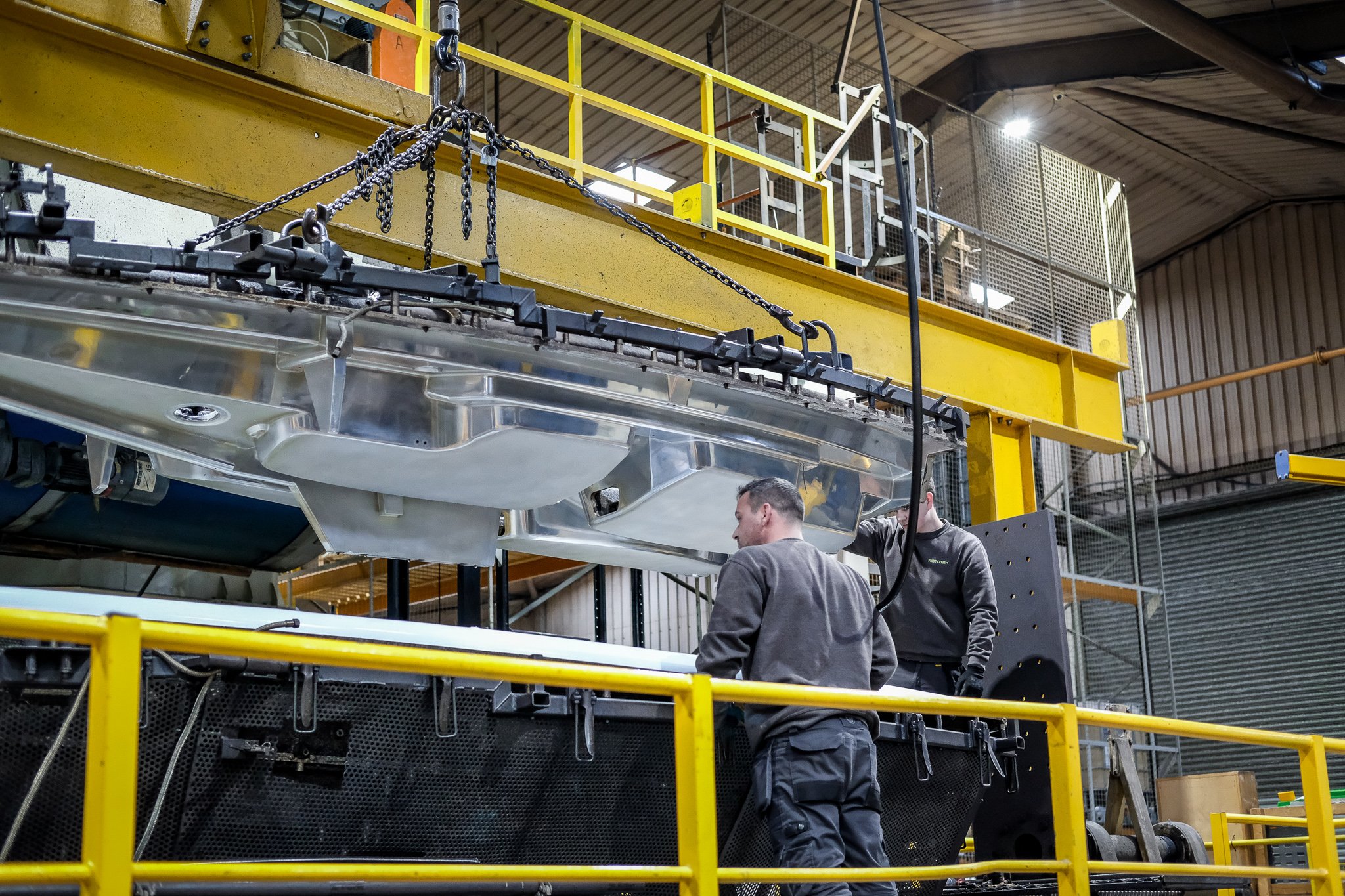
Advantages of Rotomoulding
As outlined above, the versatility of rotomoulding means that it is well suited to smaller runs of products of a wide range of shapes and sizes, delivering durable end products at a lower cost. This makes it a far more affordable option for a wider range of end users. Due to its ability to create hollow structures, the most common uses of rotational moulding include septic, chemical, oil and fuel tanks, as well as shipping and water containers. It can also create traffic signs, and consumer products such as toys.
Overall, rotational moulding costs present less than a fifth of injection moulding equivalents. It is also able to offer flexibility in terms of end design, such as offering a range of smooth or textured finishes to enhance the final product. Design amends are also easier, for example changing wall thickness without re-tooling. At Rototek, we have an experienced design team who will work with you or alongside your design team to bring your ideas to life.
However, owing to the lack of pressure in the process, rotomoulding isn’t able to contend with injection moulding when it comes to the tiny levels of detail that can sometimes be needed in very small parts, these can be imprinted on products in injection moulding, whereas you will be relying on the material flow in rotomoulding which can be troublesome due to the material used largely being PE.
On the whole, rotomoulding is considered to be the more sustainable manufacturing process of the two as it produces less waste than other techniques and employs recyclable materials such as PE. If you chose to work with Rototek, we are also a B Corp Certified company which means we are part of a global community of businesses that meet high standards of social and environmental impact.
Advantages of Injection Moulding
The ability of the injection moulding process to efficiently produce a large volume of identical and precise objects, at a lower cost-per-part is what sets it apart from rotomoulding, as well as being able to employ a wider range of materials.
Other advantages include the final product’s high tolerance, and the lack of post-processing needed. Although initial tooling costs are higher, because plastic injection moulding is typically an automated process performed by machines and controlled by a sole operator, overheads can be significantly reduced. It’s worth noting that new innovation from some companies, including Rototek, bringing the use of automation and robotics into rotational moulding machines will certainly open up new channels of production that have not been historically available from the process.
However, injection moulding has its limits too. Due to the specification of injection moulding technology, it’s only appropriate for making objects with regular (uniform) wall thickness. Furthermore, because the size of the final part is limited to the size of the mould, some large objects are impossible to produce in one single piece. Items that are too large for an injection moulding machine’s capability need to be created in multiple parts and joined together later, which can result in a less stable product.
Because of the variety of plastics that can be used in injection moulding, the method can produce a huge range of products such as automotive parts, consumer electronics, packaging, plastic bottles, and plastic furniture.
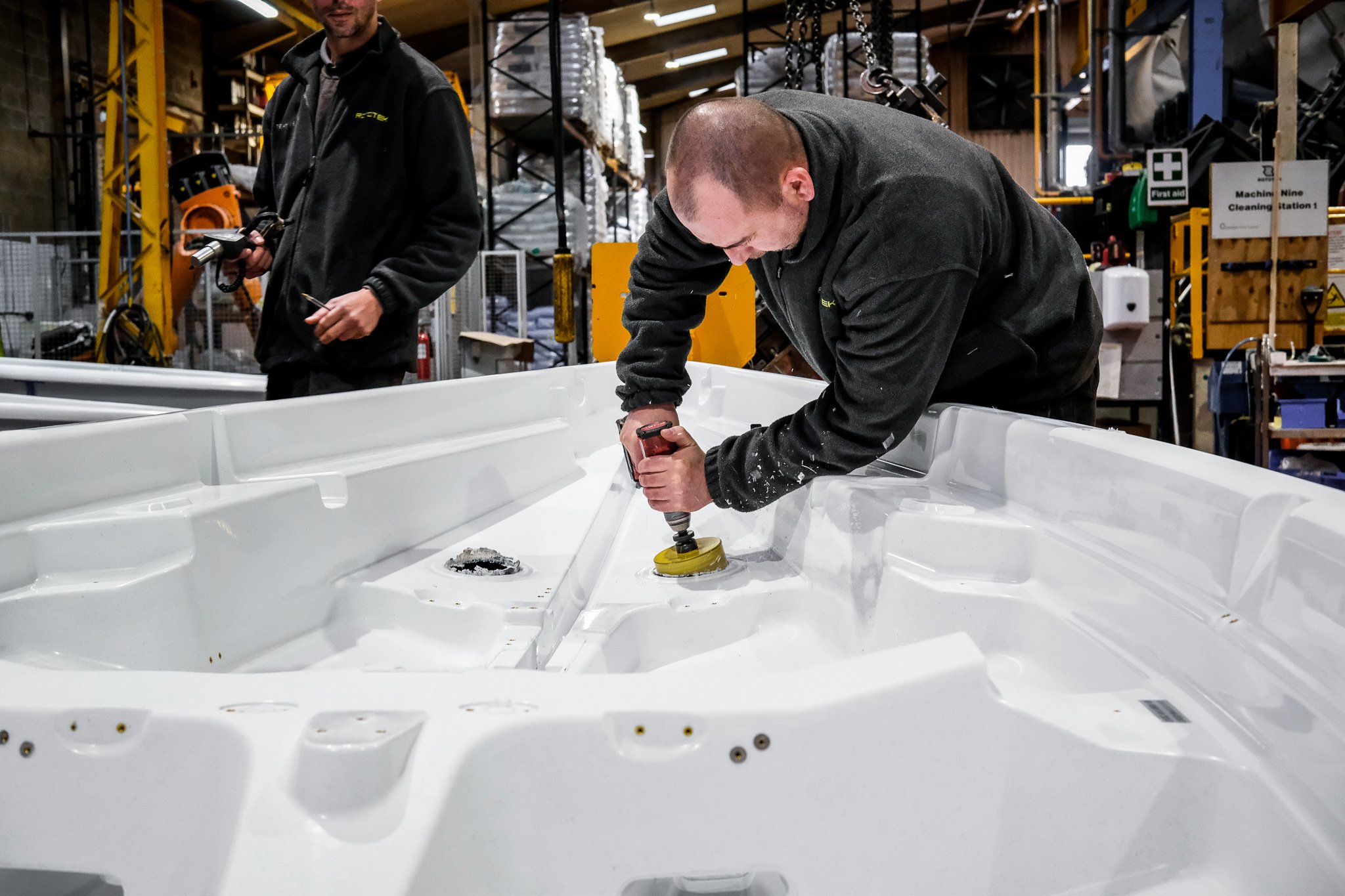
Looking ahead
Rotomoulding is rapidly becoming one of the fastest growing sectors in the plastic industry, particularly amid an increasing demand for sustainable and environmentally friendly products.
The global rotational moulding machines market was estimated at US$ 918.7 million in 2023 and is projected to reach US$ 1,321 million by 2033. Currently, rotomoulding machines make up around 1 to 2 per cent of the global packaging machinery market – a figure which we are expecting to see increase rapidly.
Rotational moulding is Rototek’s bread and butter and is a method we have specialised in for over 30 years. Utilising more than 20 state of the art rotational moulding machines and by employing robotics and automation, we produce over 150,000 products annually across two sites.
We employ advanced CAD/CAM software to allow for design optimisation and can manufacture a broad range of products, spanning from small water containers to large 7-metre mouldings. Our in-house design team will work with you to bring your ideas to life and ensure they are suited to the rotational moulding process.
Rototek are committed to reducing our impact through investing in new plant and equipment to reduce our energy usage, alongside beginning to remove the need for gas-operated machinery across our two manufacturing sites. We are a disrupter in the industry, but also a leader in coming up with innovative ways to improve the environmental viability of the rotational moulding manufacturing process.
Contact us to find out more.