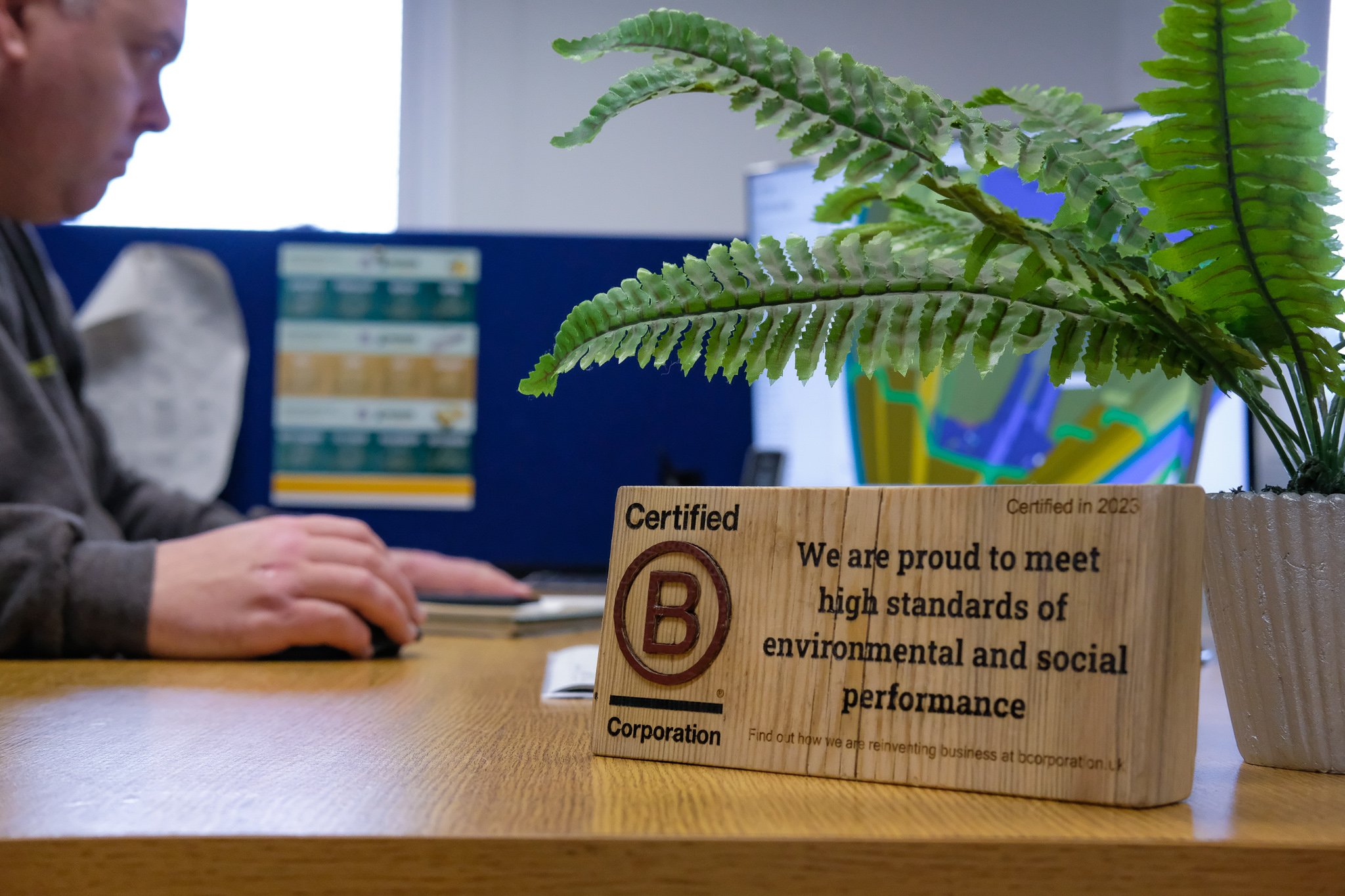
Custom Plastic Moulding
Introduction to Custom Plastic MouldinG
At Rototek, we specialise in transforming your idea into tangible products through custom plastic moulding. Our expertise in rotational moulding (rotomoulding) allows us to turn unique concepts into practical solutions across various industries, understanding our client’s vision and delivering a tailored rotationally moulded solution to meet their needs. Whether it’s creating durable components for industrial use or designing bespoke consumer products, our custom plastic moulding service offers distinct advantages compared to other manufacturing processes. More on this to come!
Rototek’s custom moulding solution focuses on designing a unique mould based on specific client requirements, turning the client’s idea into a product that is suited to the rotational moulding process. Rotomoulding offers relatively low custom plastic mould costs, from economical short runs to thousands of products, as well as the ability to cope with large custom plastic mouldings. Rotomoudling is ideally suited to new product development and prototype work, as this can be carried out without vast expense.

Rototek's Approach to Custom Moulding
Rototek’s approach to custom moulding is rooted in over 30 years of technical expertise, with a diverse team on hand to support our clients through the process. Our extensive experience in the field of rotational moulding has positioned us as industry leaders, capable of turning your idea into a functional design, and through to the final high-quality product. Our end-to-end service is designed to seamlessly guide our clients from the initial concept through to the finished product.
Initial consultation and concept development: at the outset of each project, we engage closely with our clients to understand their needs and vision for their project.
Design and material selection: our in-house design team utilizes state-of-the-art Computer Aided Design (CAD) software to create detailed 3D models of your product. Our design team can either fully create your concept, or work alongside your designers. Leveraging our three decades of expertise, we choose materials that not only fulfill the design requirements but also consider environmental impacts, durability, and functionality.
Prototyping: before proceeding to full-scale production, we create prototypes using advanced techniques such as 3D printing or wooden models depending on the size and complexity of the project. This critical step allows us to test the design’s functionality and make necessary adjustments, ensuring the final product will perform as intended under real-world conditions.
Toolmaking and production: we have relationships with a range of specialist tool makers, which enables us to select the right tool making partner for your project. Our design team project manages the entire tool making process for you, resulting in a custom plastic mould that is ready for use in our manufacturing facility. This mould will always be produced using steel or aluminium for durability. The production phase is then carried out using our cutting-edge rotational moulding machines, which are capable of handling everything from small to large-scale mouldings. Our skilled operatives oversee the manufacturing process, applying their expertise to manage the unique requirements of each product.
Quality control and finishing: as the product emerges from production, it undergoes a rigorous quality control process. Every item is carefully inspected to ensure it meets our high standards, as well as those of our clients. The finishing touches are then applied, which may include the fitting of components, additional detailing, and final aesthetic enhancements by our finishing team.
Delivery and aftercare: once a product has passed all inspections and meets our quality expectations, it is prepared for delivery. We pride ourselves on our punctual delivery services and can ship products worldwide direct to your customer, offering a range of contracts to suit your requirements.
By choosing Rototek, clients benefit from our 30 years of technical experience and are partnering with a leader in custom plastic moulding capable of delivering exceptional results that align with their specific needs. Our approach is not just about meeting expectations but exceeding them, ensuring each client receives a product that truly reflects their vision and requirements.
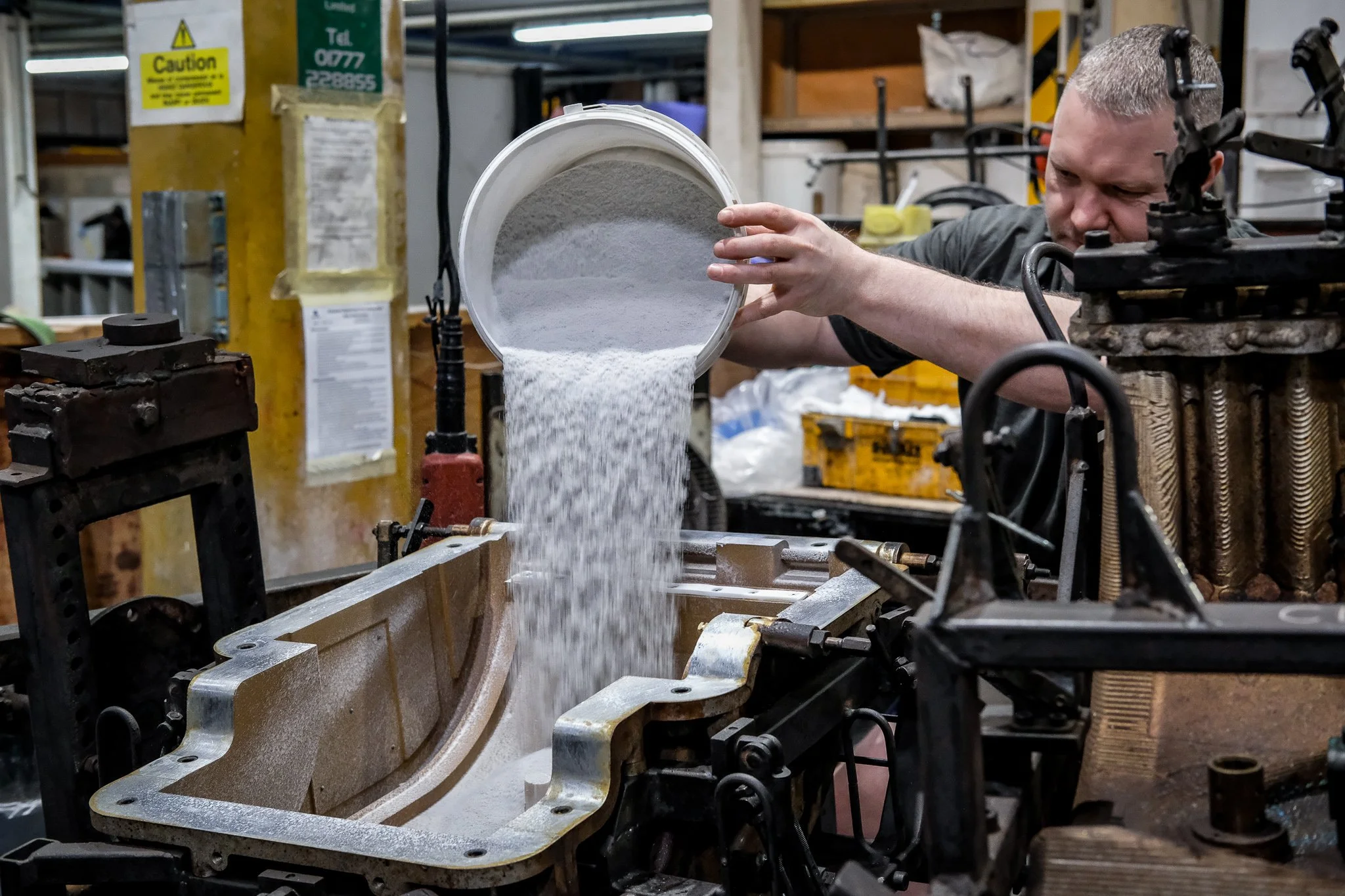
Design and Prototyping Services
Our in-house design and prototyping service is central to our custom plastic moudling process. The initial phase in our design process involves a thorough analysis of the product requirements and their intended use, this helps us understand the challenges and demands the product will face in its operational environment. Then we must select the right material, ensuring we choose the plastic powder that offers the best balance of strength, flexibility and durability for your product. Our design team then use CAD software to create precise 3D models of the proposed products, allowing us to visualise the product in great detail.
Once the initial 3D model is created, we make adjustments to enhance the product’s manufacturability and functionality. This involves refining the design to ensure it can be efficiently produced without compromising quality or performance. Once the team are happy with the final design, we work with our tooling partners to create the moulds. The final stage is our sampling process, where we create samples of your product in our manufacturing facility with the newly completed mould as part of a fit and function test. Our design and prototyping services are designed to ensure that every product we create achieves its intended purpose and exceeds our clients’ expectations.
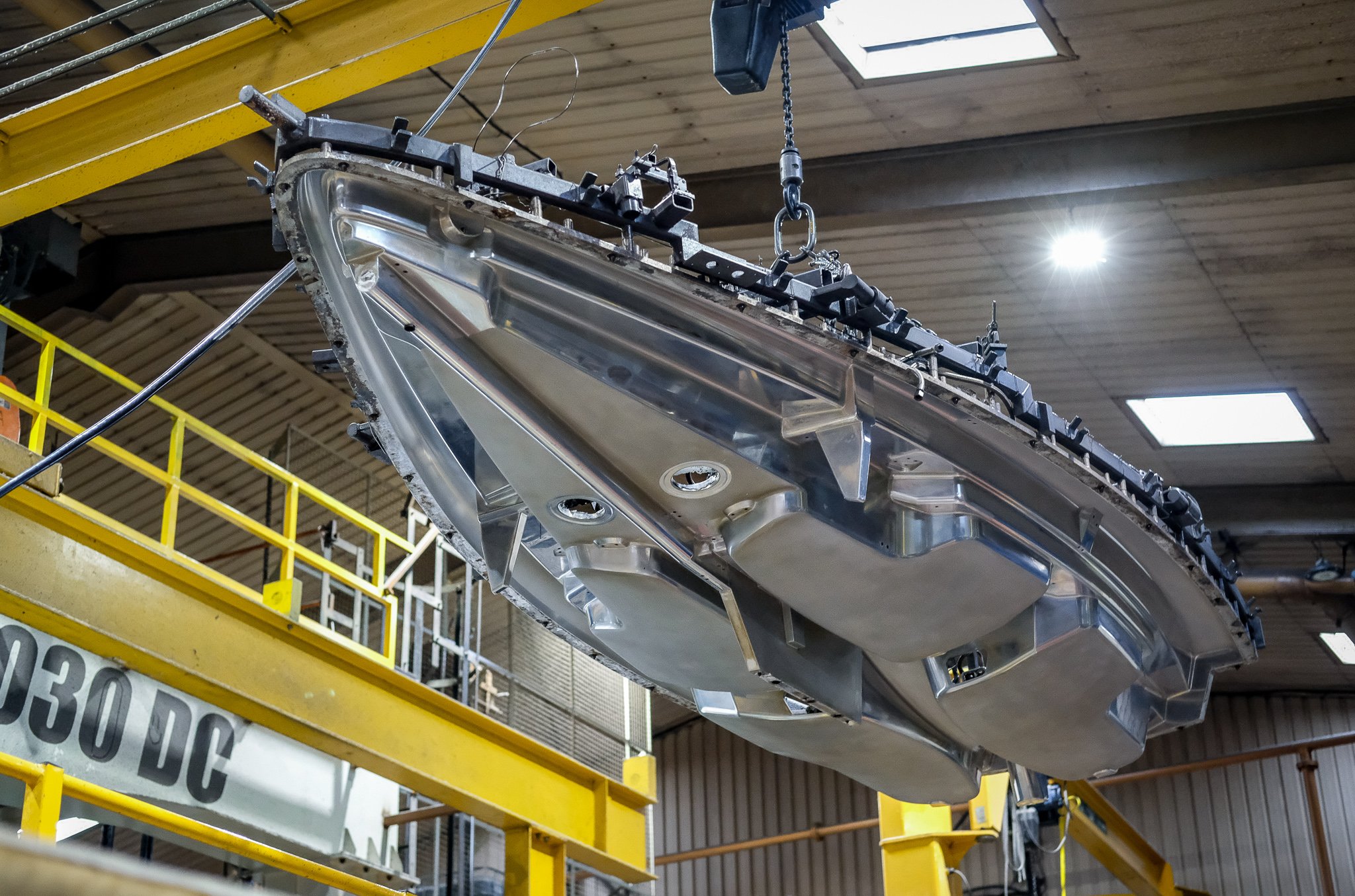
Production Capabilities
Rototek operates across three manufacturing sites in Nottinghamshire, with over 150,000 square feet of production space. These well-equipped sites enable us to handle projects of varying scales and complexities, showcasing our capability to consistently deliver exceptional products. Our facilities operate across three shifts per day, ensuring continuous production and flexibility. From compact containers to large-scale mouldings of up to 7 meters, our technology and skilled workforce are equipped to deliver your project. Our unique use of customised machinery and robotics enhances our efficiency and the quality of the finished products.
Across our three sites, we currently manufacture over 100,000 products per year across our 20 machines, ranging from rock & roll and bi-axial carousel machines to electrically heated tooling. We are also investing in more sustainable production methods in our newest factory.
We have the capability to use recycled powder if this is appropriate for your product. Most of the plastic powder used within our manufacturing process ensures the final products will be recyclable by the end consumer.
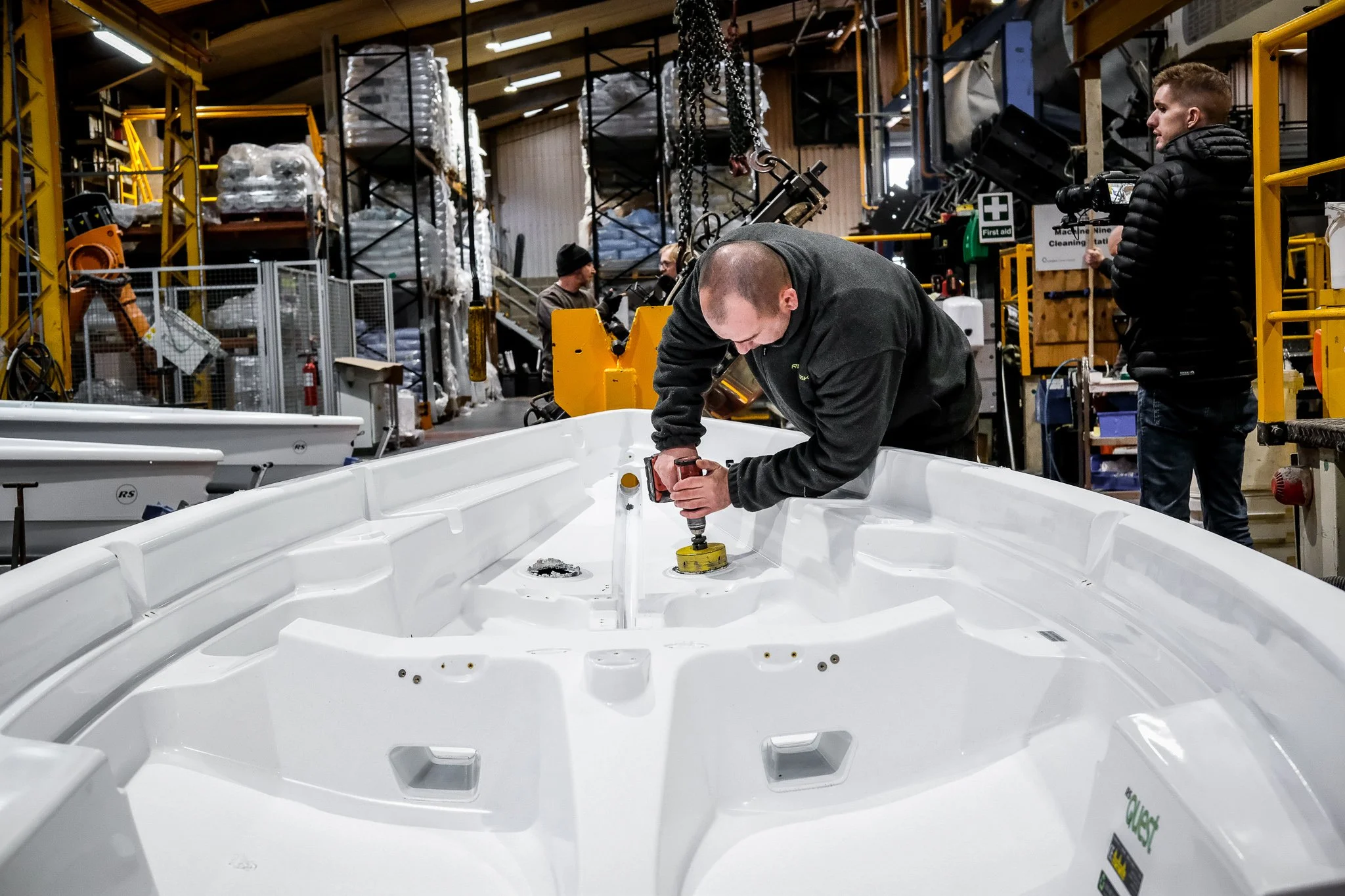
Quality Assurance and Sustainability
As an ISO 9001 accredited and B Corp Certified company, Rototek adheres to high quality standards. In 2023, over 99.7% of our products fulfilled our customers' expectations in terms of quality, which is well above the industry standard. We strive for continuous improvement in our processes and products, aiming to contribute positively to both our community and the environment. We are investing in more sustainable production methods and would like to work with new clients who share our vision of a more sustainable future for the manufacturing industry.
Rototek achieved B Corp Certification with our parent company, Gusto Group. The Group also includes construction companies Gusto Homes and Gusto Construction. As a B Corp, we are part of a global community of businesses that meet high standards of social and environmental impact, which has been certified through our completion of the B Corp Impact Assessment. By certifying, we are stepping into a framework for continuous improvement. Therefore, to maintain certification, companies must undertake the assessment and verification process every three years, demonstrating they are still meeting the B Corp standards. A company must score 80 points to achieve B Corp Certification and Gusto Group are proud to have scored 92.3 points.
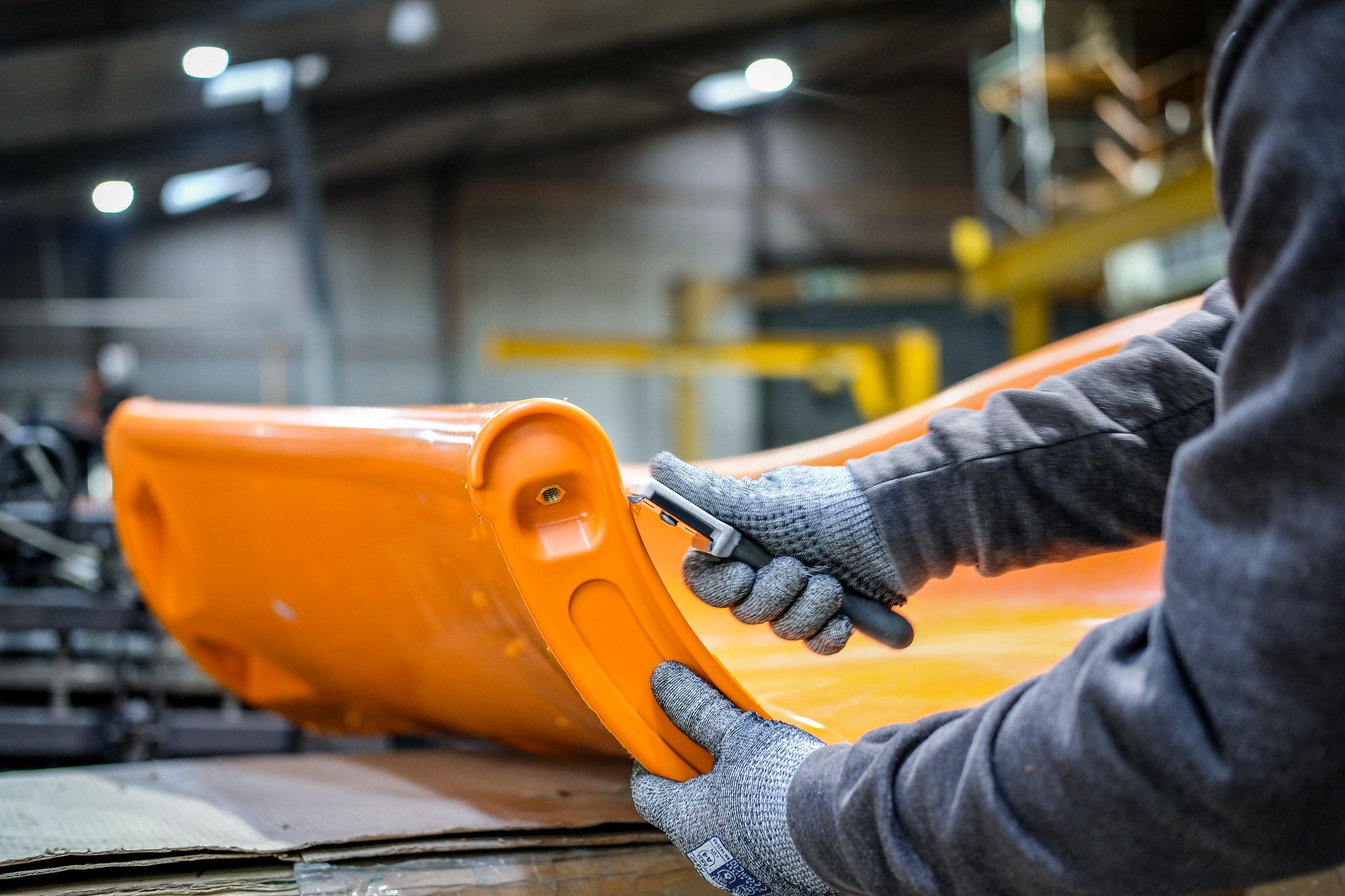
Applications of Custom Plastic Products
Our portfolio of products showcases the diversity of our manufacturing capabilities, from smaller furniture to 7m sailing dinghies, we have the capacity to create it all. Examples include: oil and water tanks, grit bins, bollards, outdoor and indoor furniture, marine applications, pump chambers/housing, mudguards, bumpers, portable toilet parts, containers, planters, privacy screenings, the list goes on! Our in-house design team loves a challenge and will work to bring your idea to reality within the capabilities of our manufacturing process.
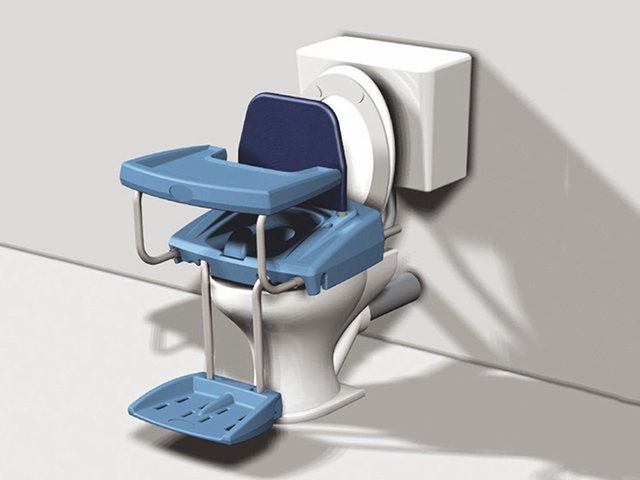
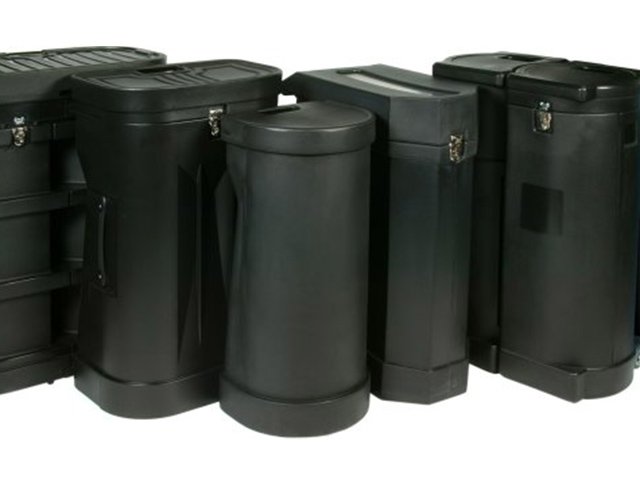
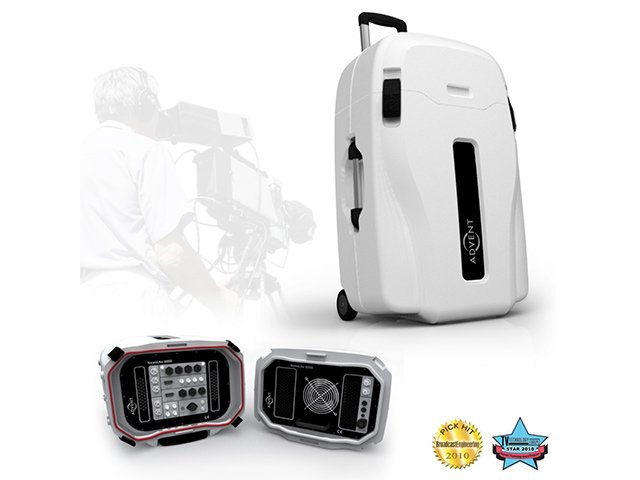
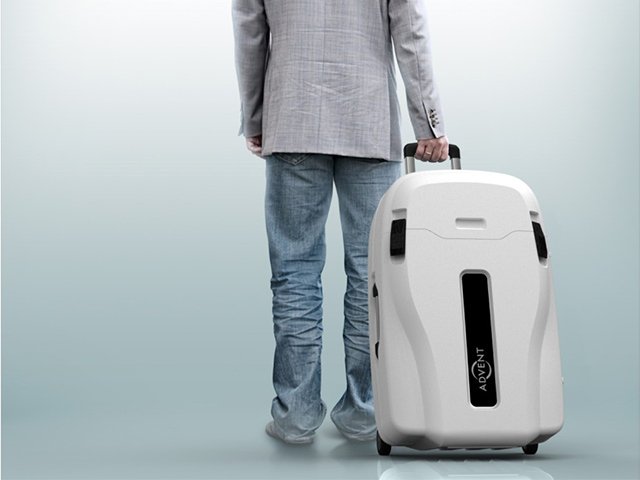
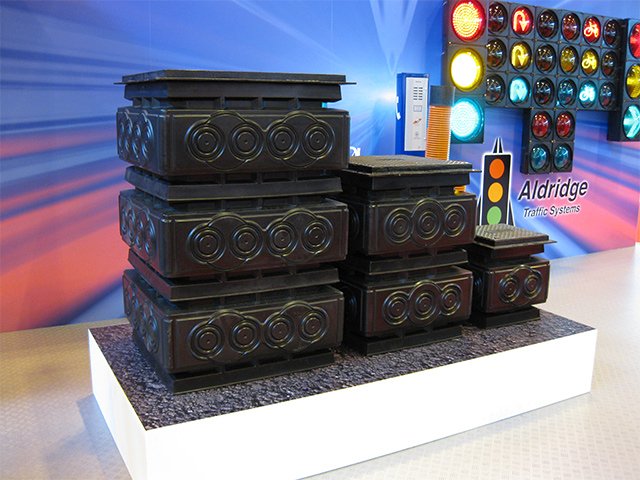
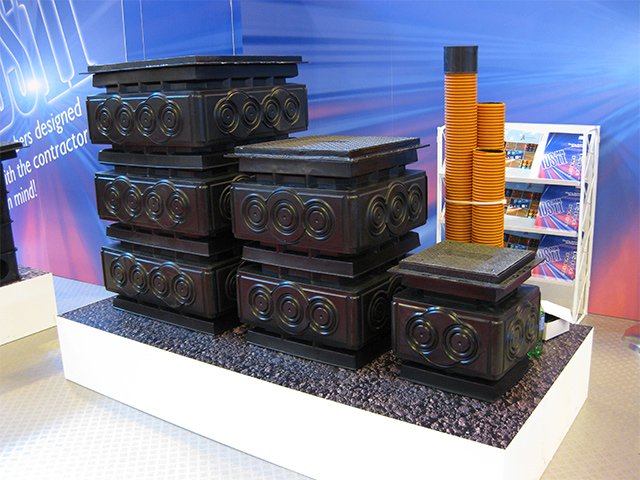
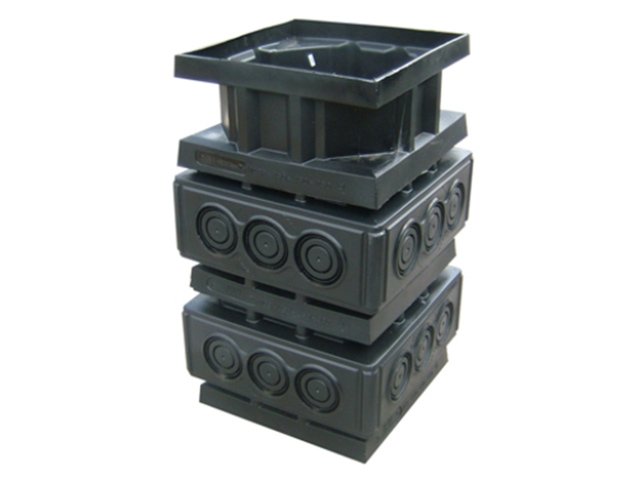
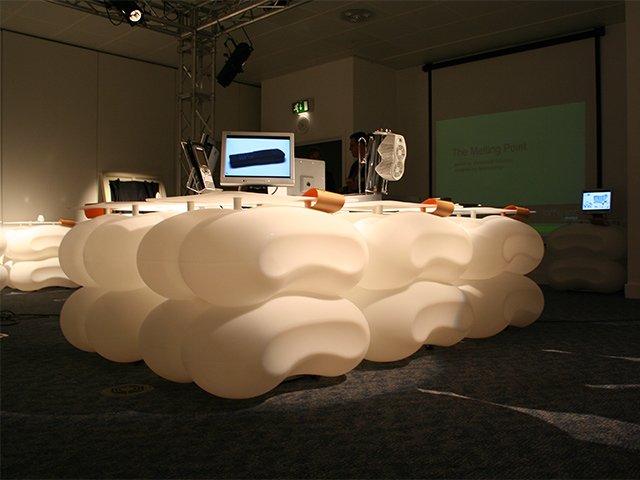
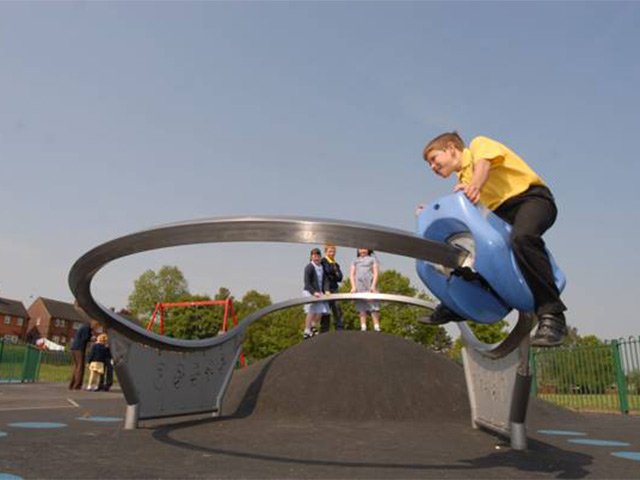
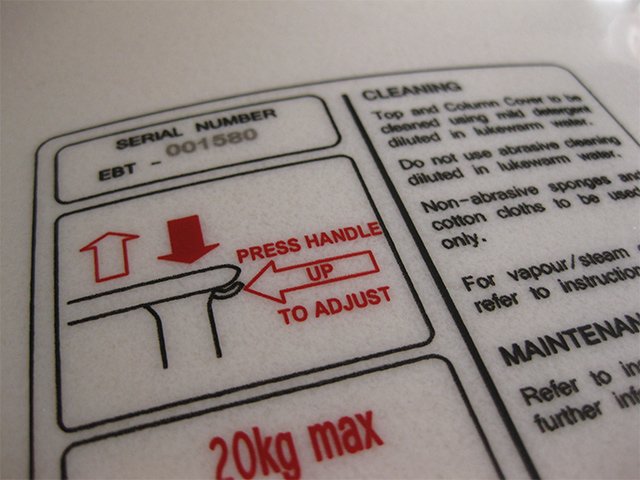
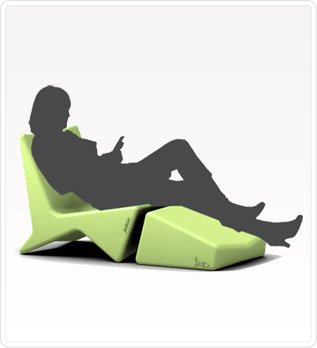
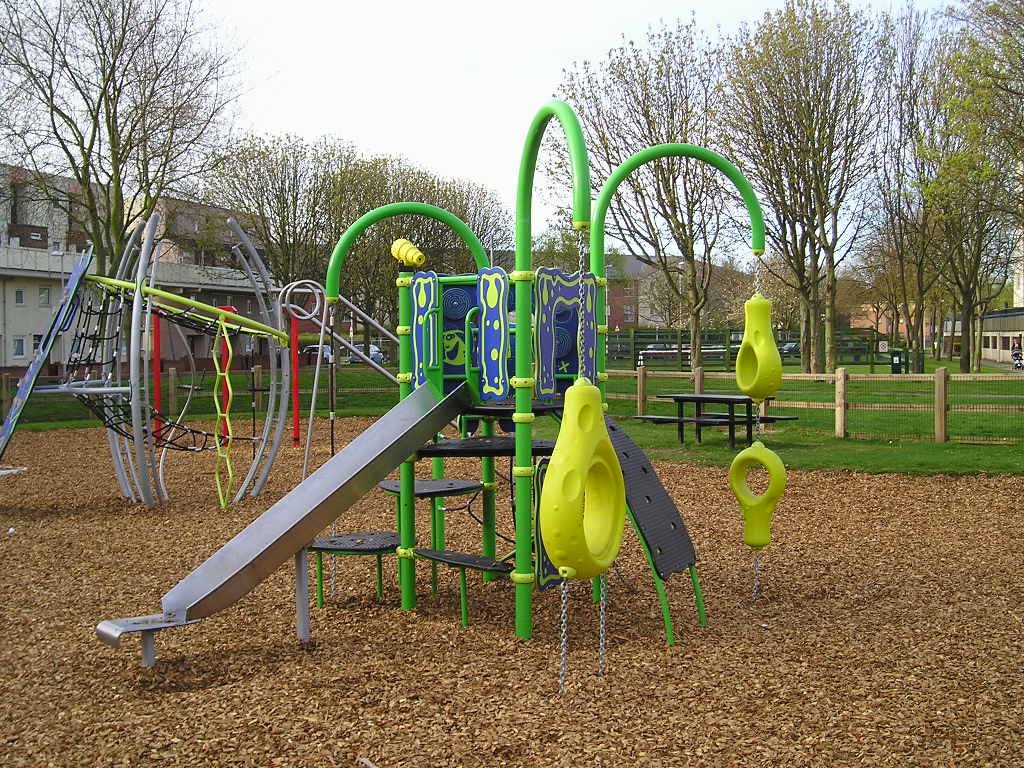
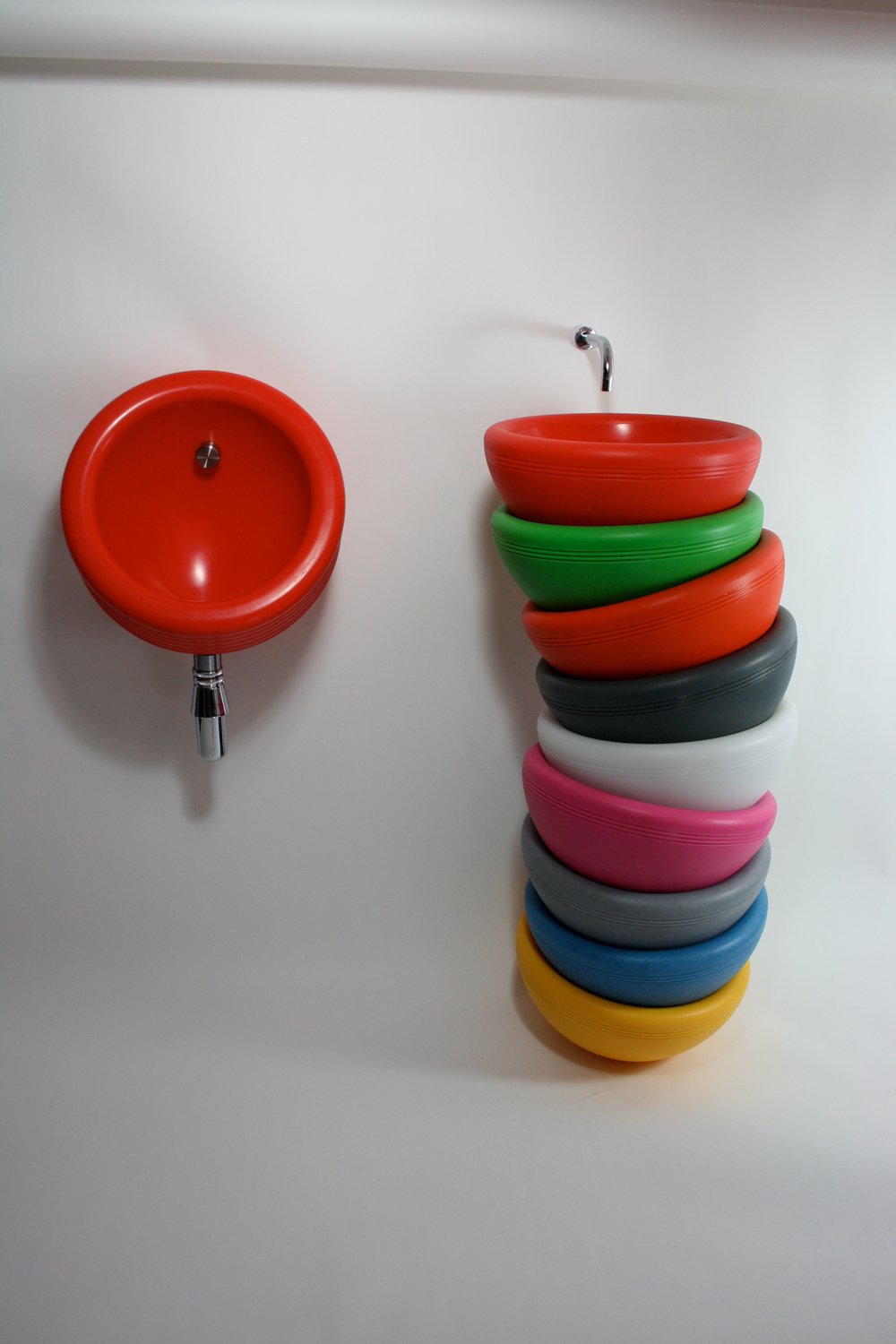
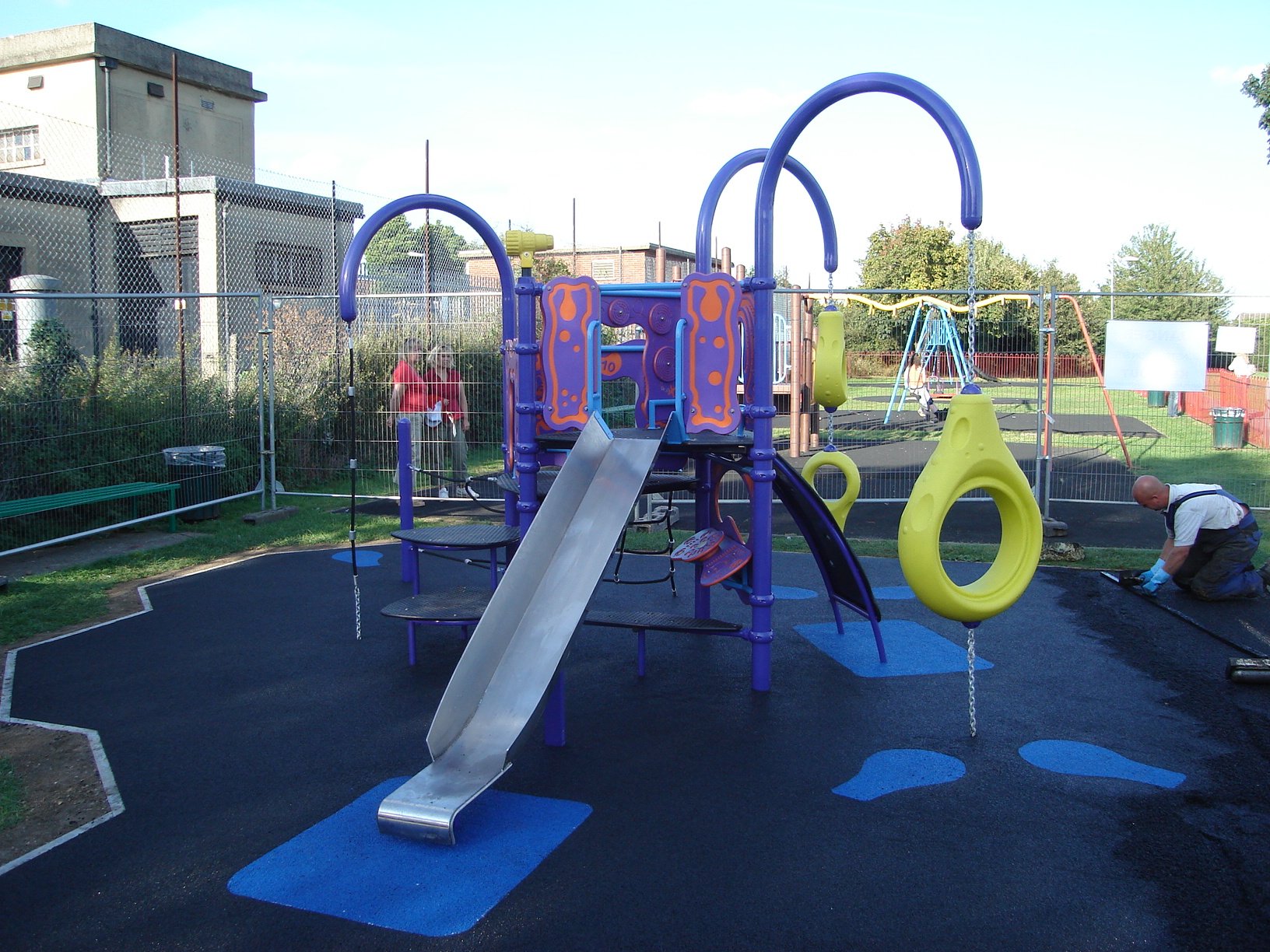
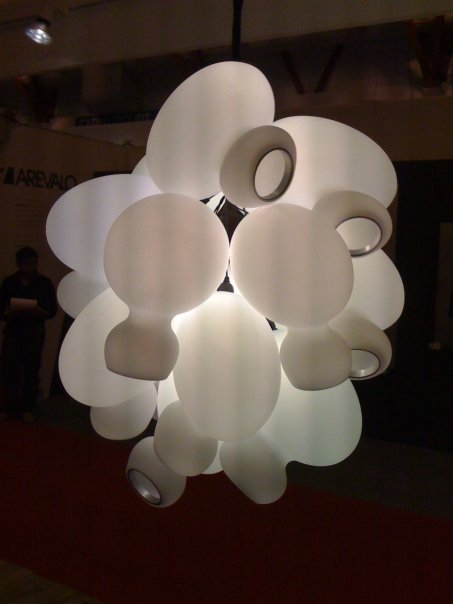
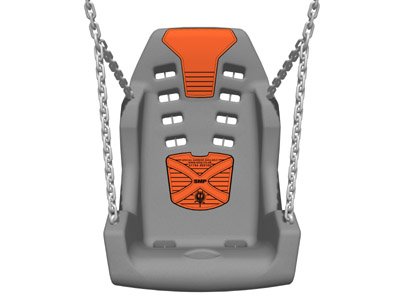
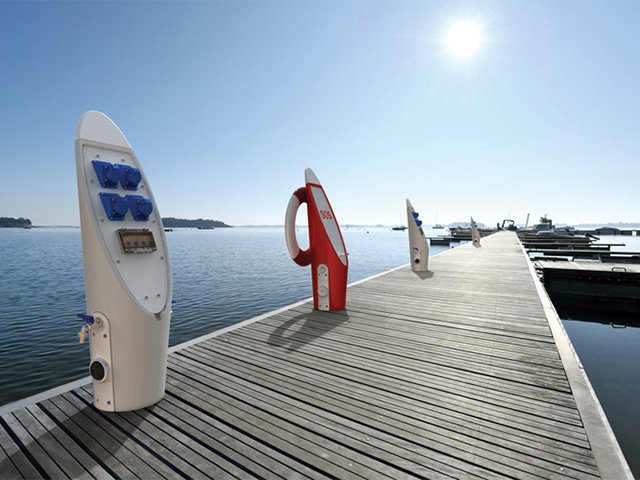

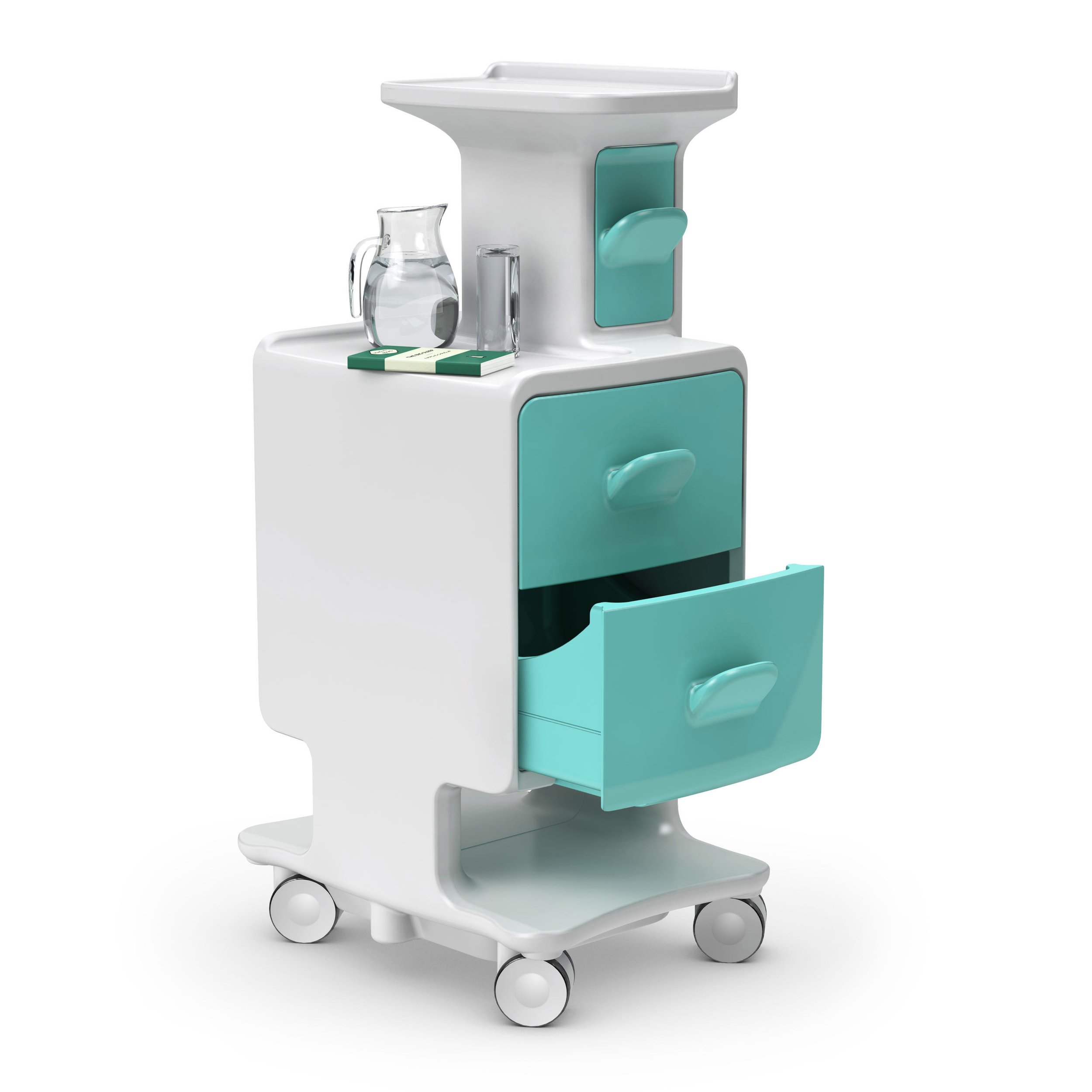
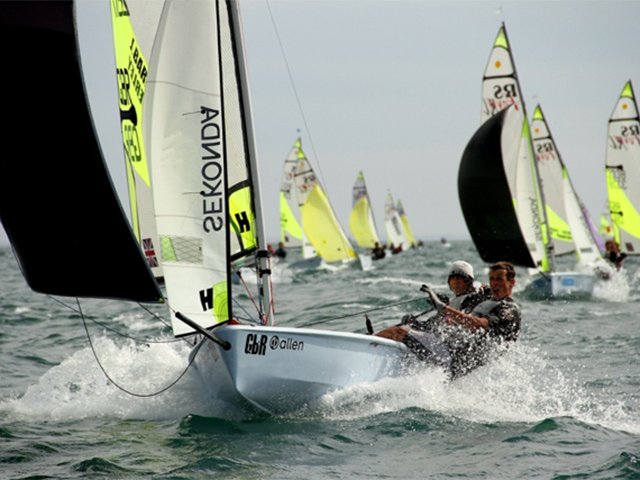
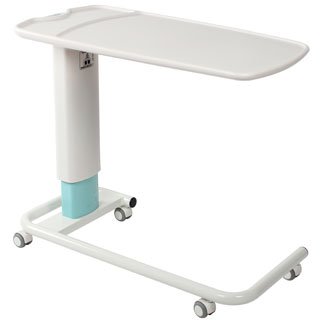
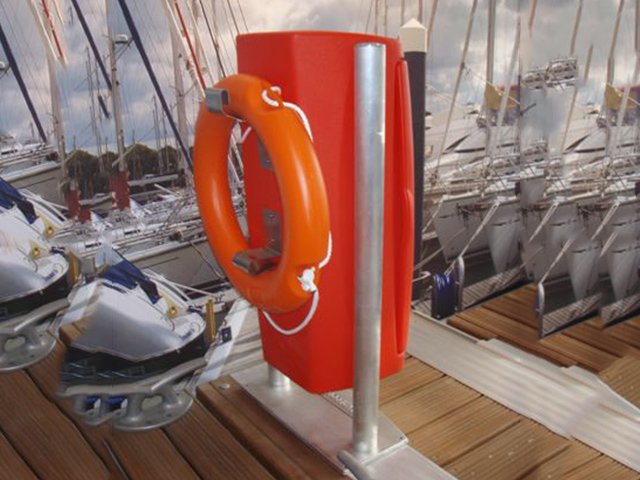
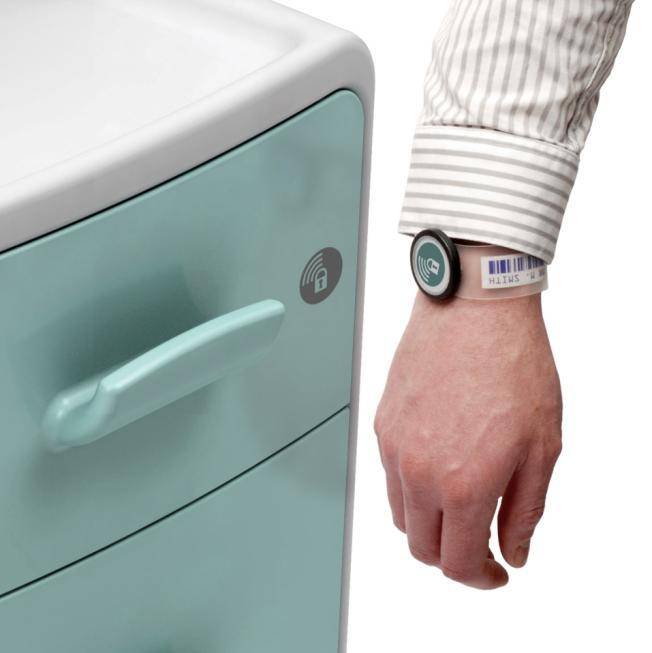
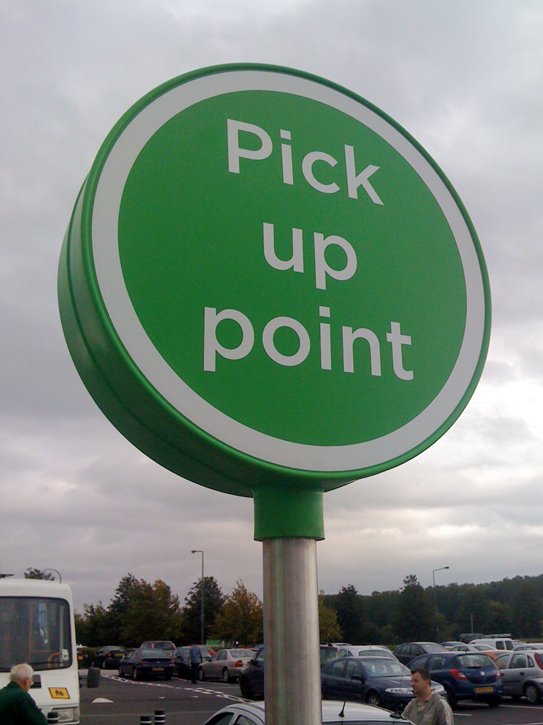
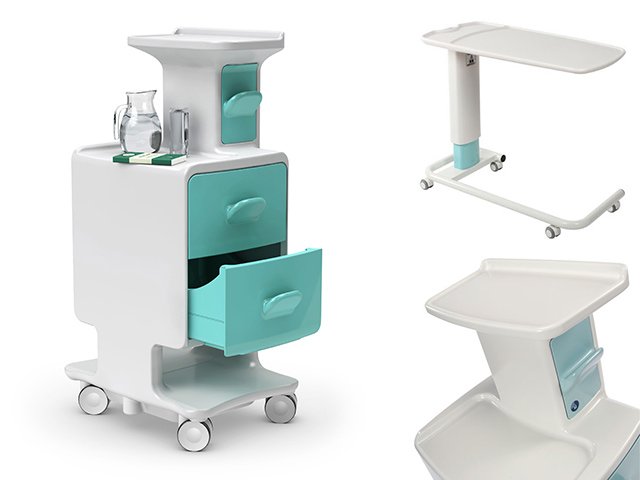
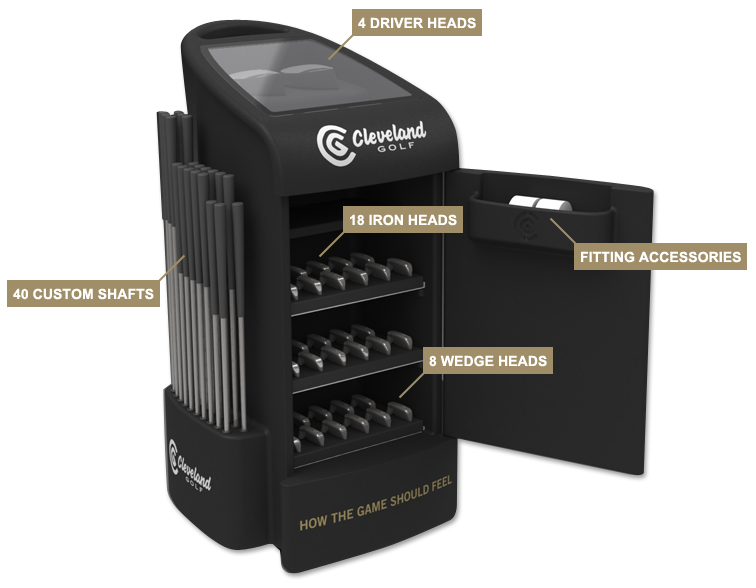
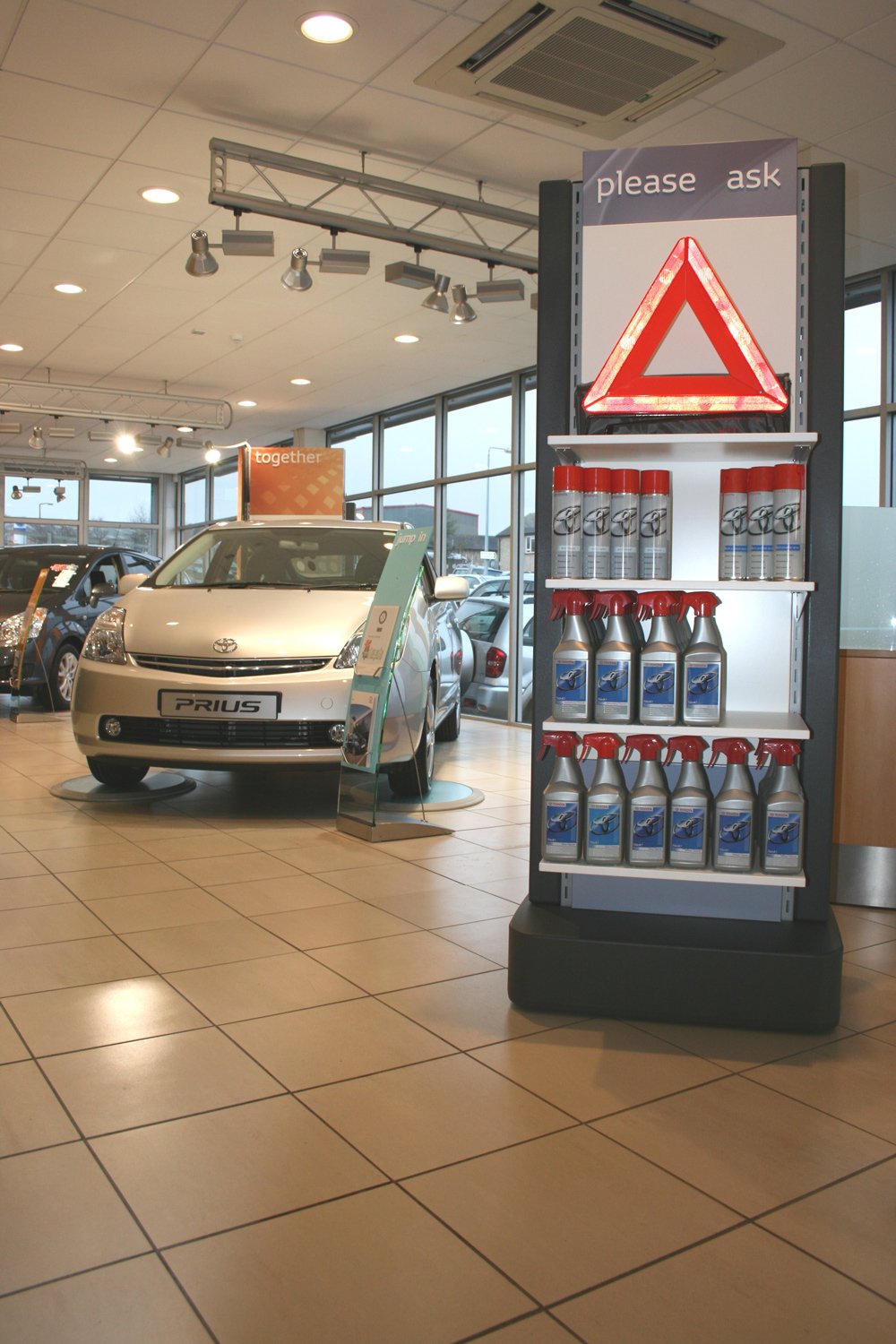
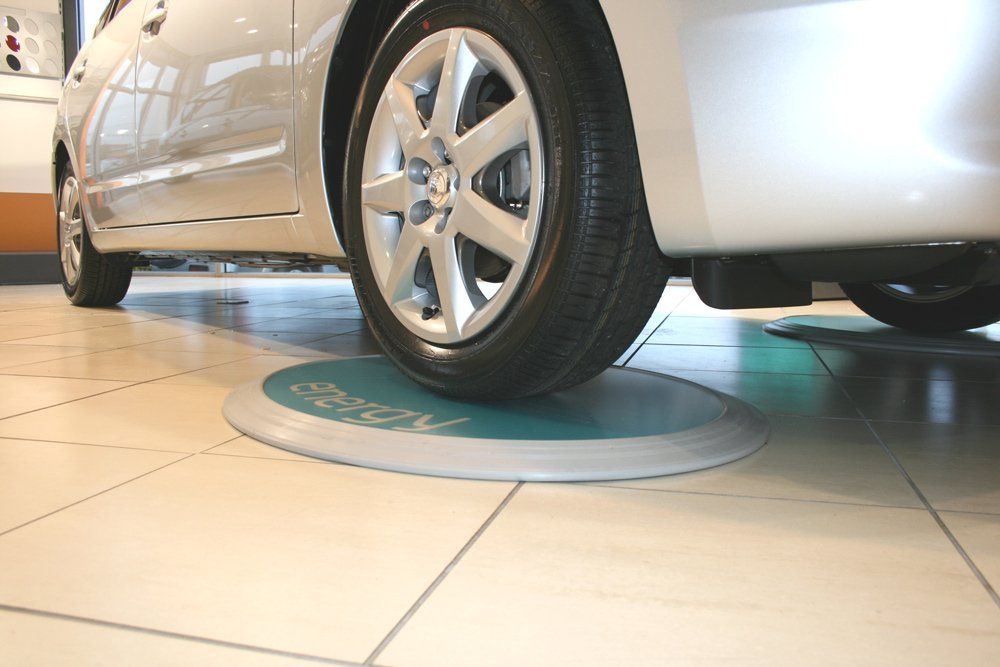
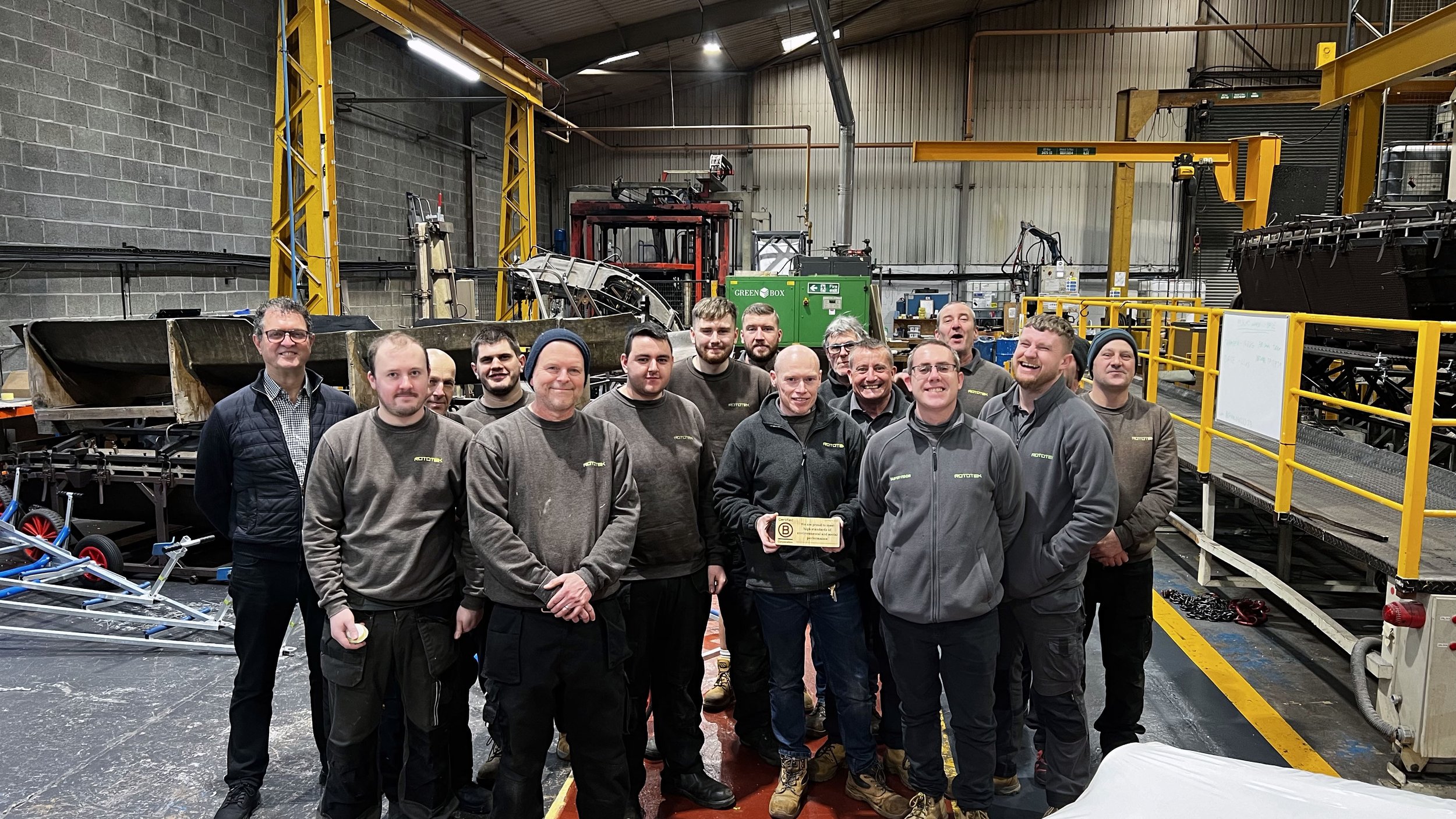
Why Choose Rototek for Custom Moulding?
Rototek brings over 30 years of experience in technical rotational moulding, combining a deep understanding of the industry with the technical skills required to produce the custom plastic moulding to fulfil your needs. Our 30-year presence in the market is a testament to our ability to adapt and thrive in this ever-evolving industry, making us a reliable partner for your manufacturing needs.
Our comprehensive, end-to-end service makes us stand out from other manufacturers, with our friendly and knowledgeable team on hand to guide clients through the process. Our brilliant team are the reason we have such
high customer retention rates and positive feedback on their customer service. Our team is dedicated to shaping the future of manufacturing, transforming your concepts into tangible products. We pride ourselves on having the right team to solve the issues that may occur, and we are there not only as your supplier but as your moulding partner, giving you the first-class service that you need.
With Rototek, you're not just choosing a service. You're partnering with a leader in innovative and sustainable manufacturing solutions.
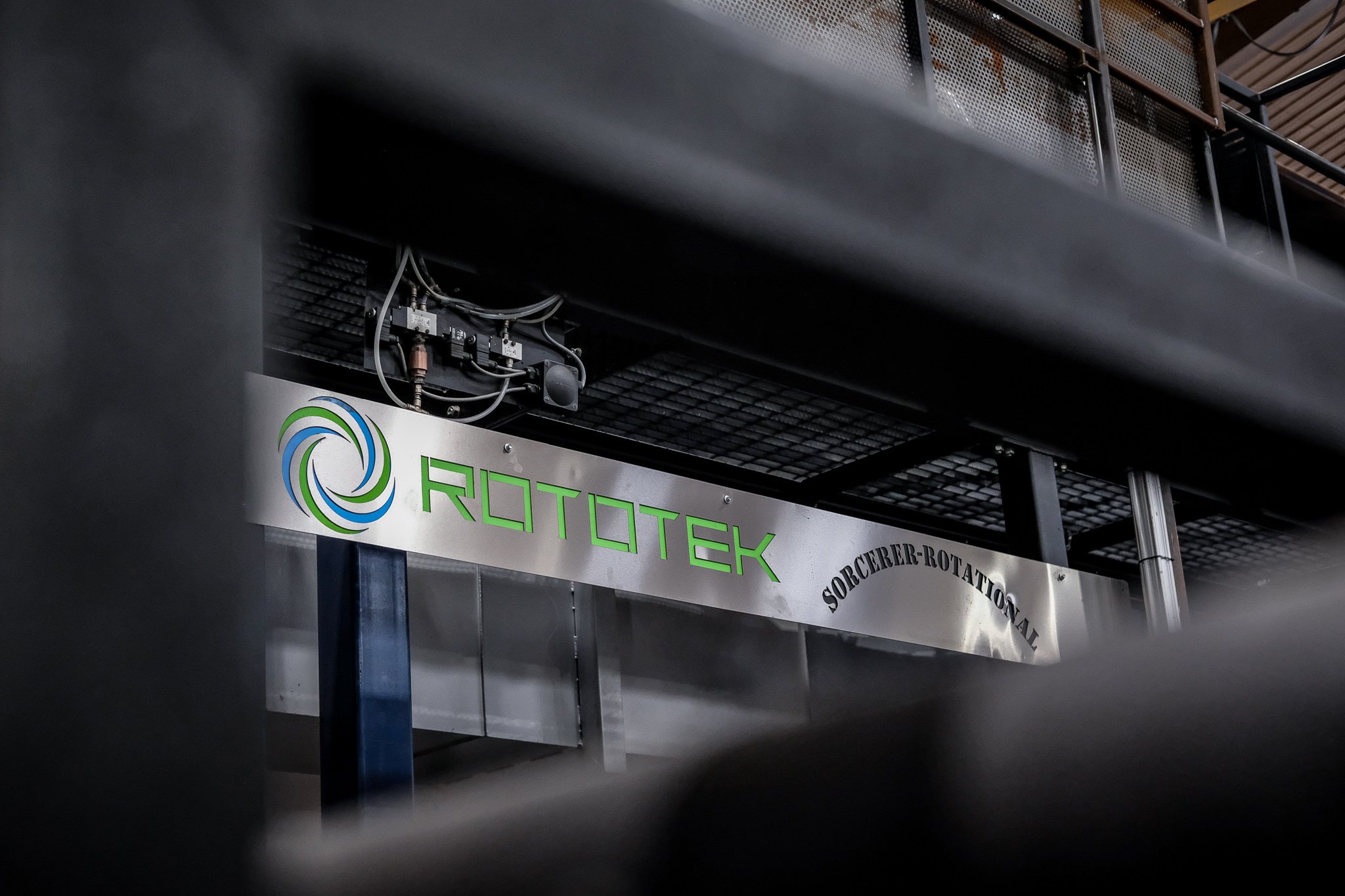
Contact us
Transform your idea into tangible products through custom plastic moulding.