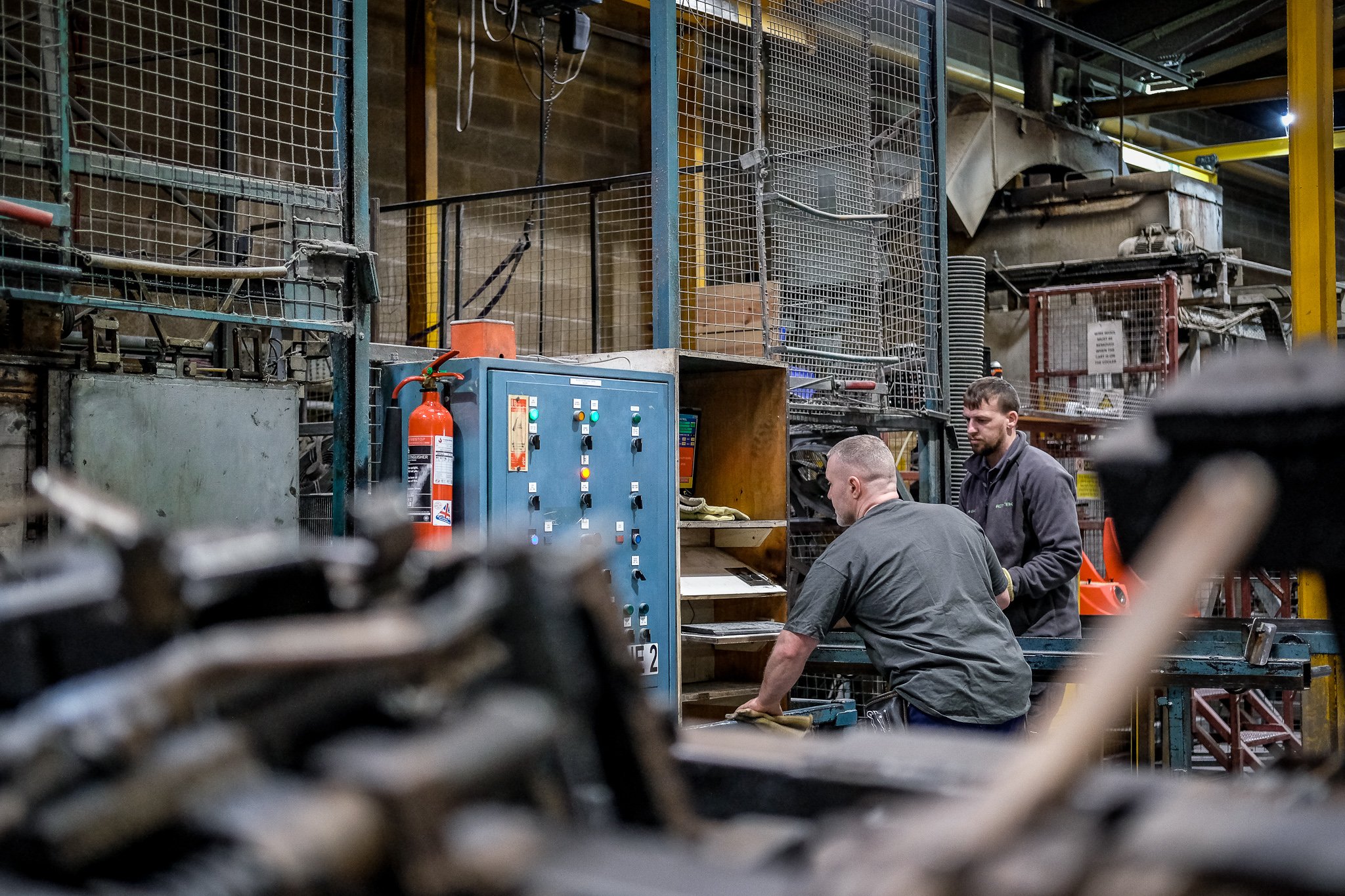
Rotomoulding with PE and PU foam
Designers of plastic parts and products have a wide range of techniques to achieve their desired outcomes. Key factors in selecting the most suitable method include cost, quality, versatility, and production timelines. At Rototek, we take this a step further by offering value-added solutions, such as incorporating partially foamed polyethylene (PE) in two or three layers, as well as fully polyurethane (PU) foaming for complete parts.
Rotomoulding: PE Layering
The rotational moulding (rotomoulding) process begins with loading a mould with a precise amount of polymer powder or resin. At Rototek, we can enhance this process by offering multi-layer capabilities. With expertise developed since the early 2000s, we have been producing multi-layered components for various industries, including marine, paddleboards, and offshore sectors.
Our rotomoulded parts start as hollow mouldings, created during the rotational moulding process. During production, we can incorporate multiple layers of materials to enhance product buoyancy and impact resistance. These advanced techniques ensure your products not only meet but exceed performance expectations in demanding applications.

The Advantages of PE Layering
PE layering offers several significant advantages, streamlining production while enhancing product quality. By integrating the entire process into a single operation, the need for additional post-processing steps, and the associated labour, is eliminated.
This method ensures a complete chemical bond between layers, enhancing structural integrity and significantly reducing the risk of delamination. Using advanced in-mould technology, we monitor three critical parameters: internal air within the mould, the mould itself, and the airflow around the mould. This precise monitoring, available on all our machines, sets Rototek apart from most competitors.
Additionally, the efficiency of completing the process in a single production cycle translates to cost savings, which can be passed directly to the customer, making PE layering an economical and high-quality solution.
The Disadvantages of PE Layering
PE layering requires in-house expertise and precise control throughout the process. Without the necessary skills and monitoring systems, it becomes difficult to process materials correctly, leading to inconsistent results and reduced product quality.
Additionally, the range of materials suitable for this process is limited, so it may not be suitable to your project for this reason.
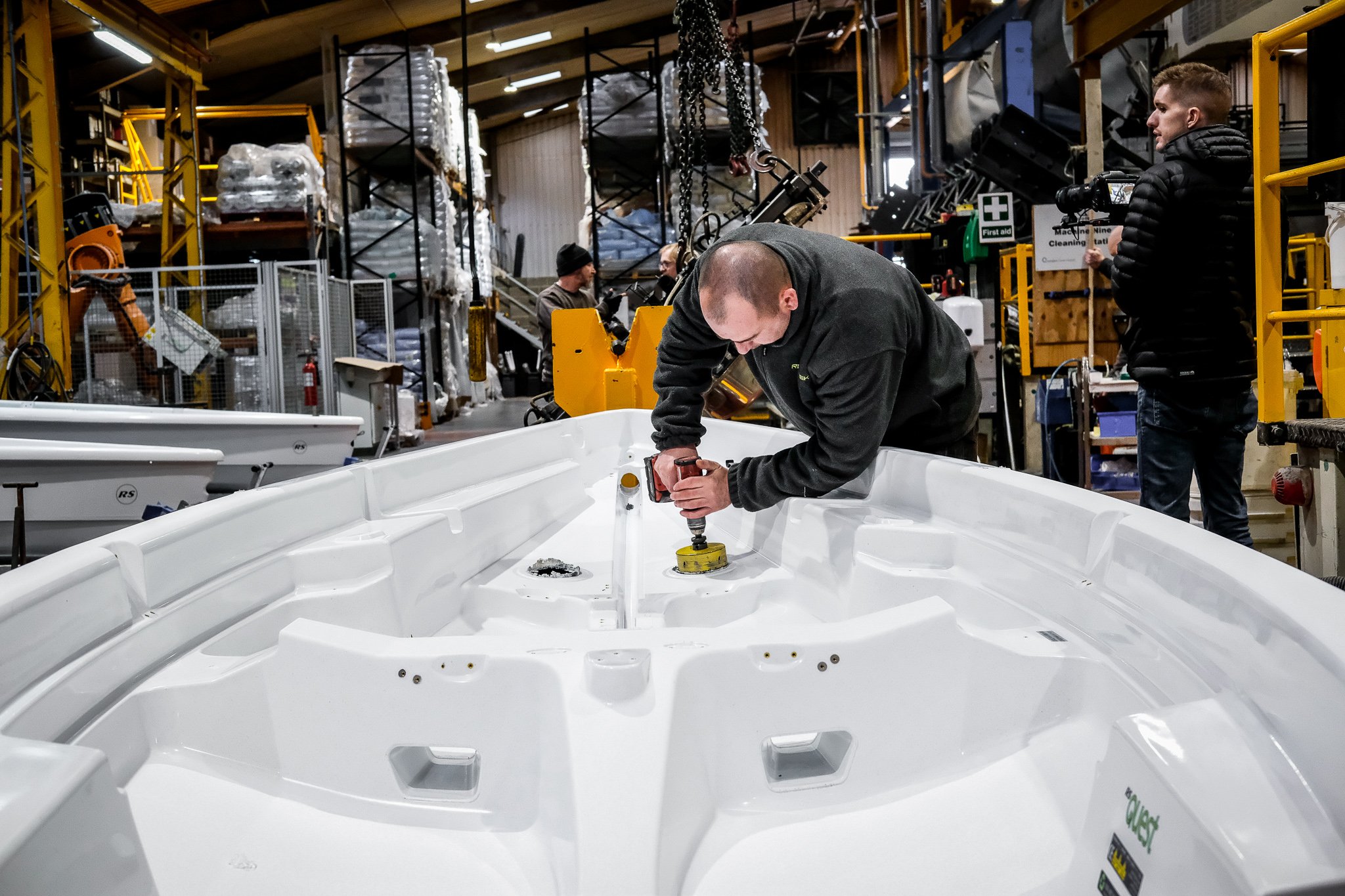
Materials we can use: Polyethylene (PE) powdered foam
We offer several material options tailored to the end use of your product, with the most popular choice being polyethylene (PE) foam. This material is available in powdered form, similar to standard polyethylene, as it is essentially polyethylene combined with either compounded or blended foam - selected based on the specific application requirements.
One major advantage of using PE foam is its recyclability. This material can be kept in a closed-loop system and recycled repeatedly, making it an environmentally sustainable option.
PE foam is also highly versatile, offering excellent impact resistance and chemical resistance. Its durability and cost-effectiveness make it an ideal solution for enhancing the functionality of hollow parts. The foamed material allows for the design of lightweight technical products with added benefits such as sound deadening, insulation, and buoyancy - ideal for applications like boat hulls and floats. It is strong yet lightweight, ensuring a balance of durability and performance for a wide range of applications.
Materials we can use: Polyurethane (PU) two-part foam
The rotomoulding process involves loading a mould with a pre-measured amount of polymer powder or resin and the end result is a stress-free hollow part.
To further enhance product performance, we can incorporate PU foam to completely fill the moulded part, providing additional sound insulation and structural stiffness where needed.
PU foam is available in various chemical formulations, allowing for the production of either rigid or soft, flexible foam. This versatility makes it suitable for applications requiring high stiffness, flexibility, or cushioning.
Unlike PE foam, the application of PU foam is a post-production process. It requires specialized equipment and solid formers or jigs to maintain the product’s shape. Due to the material’s high exothermic reaction during curing, parts must remain in jigs for extended periods - potentially hours or even days - depending on the amount of PU foam used per product.
The big disadvantage of using PU is that we cannot reuse this material back into our production cycle and it must be removed and sent to a specialized facility for recycling.
Polypropylene (PP) foam and EVA (Ethylene-vinyl acetate) foam are alternative materials; however, we have chosen not to incorporate them into our process. This decision is driven by the limited recyclability of these products, which does not align with our internal sustainability and environmental policies.
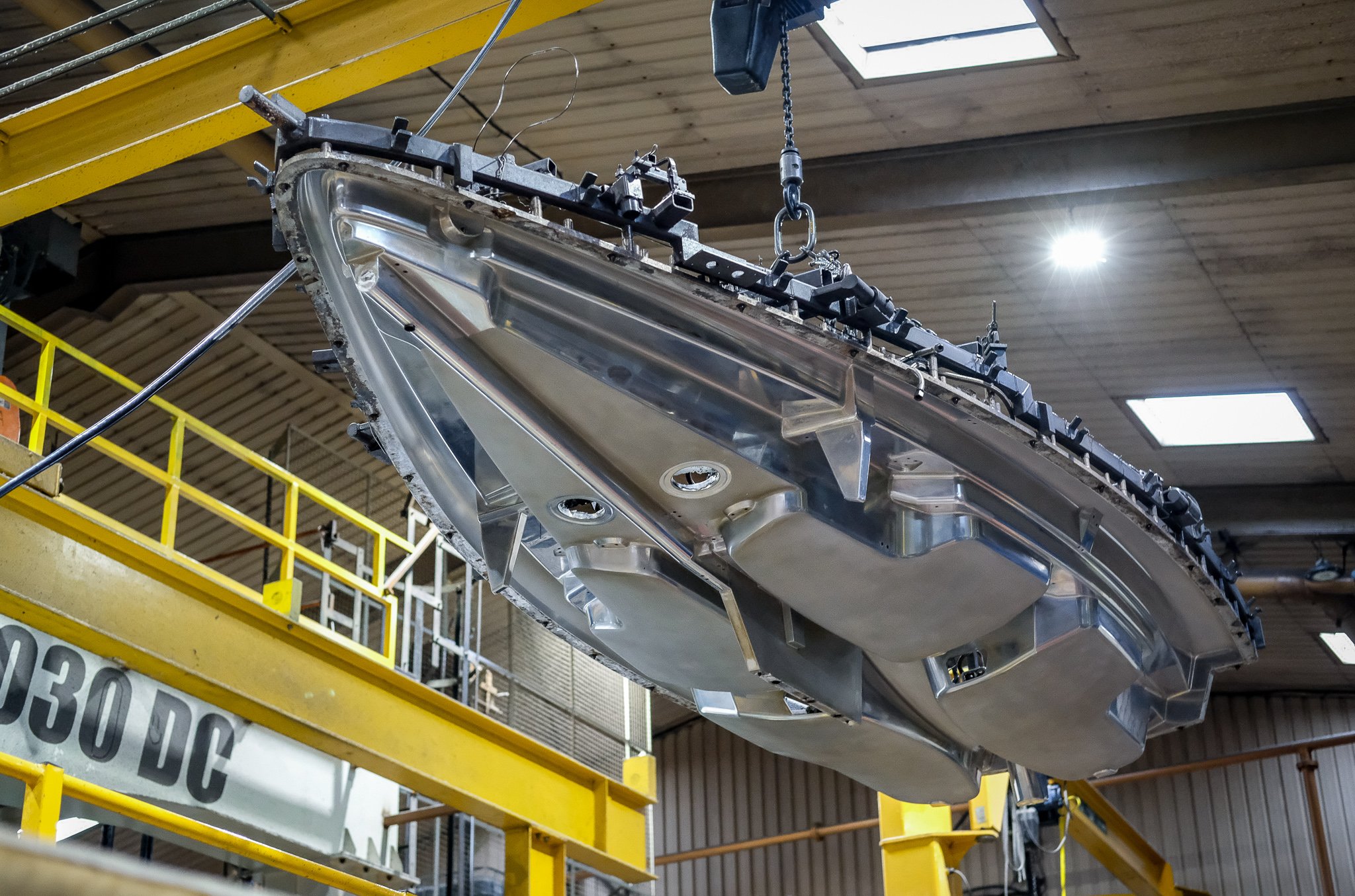
What types of PE Foam do we use: One-step foam
The one-step foam process is ideal for applications such as fish storage boxes. In this method, polyethylene material is compounded or blended with a blowing agent additive, allowing it to be used directly in the rotational moulding process. During moulding, the additive and standard polyethylene melt at different rates, creating a solid outer skin with a foamed inner core. This results in a product that maintains a rigid, durable exterior while offering a softer inner layer to protect the contents. The process can be customized to meet the specific requirements of the end user, ensuring the final product aligns with the desired application and performance needs.
What types of PE Foam do we use: Open and closed cell foams
Open and closed cell foams are often discussed together, but they are distinct materials with different costs, applications, and performance characteristics. Both types start with a polyethylene base, combined with a blowing agent additive that is either compounded or blended into the material for direct use in the rotational moulding process.
Open cell foam forms large bubbles within the material, with air filling the open spaces between the cells. This creates a softer, more flexible structure, similar to a sponge. Although open cell foam can be harder to control during production, it is typically more cost-effective than closed cell foam due to the use of fewer additives and less material.
Closed cell foam produces smaller, more tightly packed bubbles, resulting in a denser and more durable material. It offers excellent strength, chemical resistance, and rigidity, making it ideal for applications that require buoyancy and impact resistance. Closed cell foam is commonly used for boat hulls, industrial and commercial components, offshore floats, and buoys where stiffness and durability are essential.
Each type of foam serves specific purposes, allowing for tailored solutions based on performance needs and budget considerations.
CONTACT US
If you’re interested in enhancing your rotationally moulded products with PE or PU foam, our team at Rototek is here to help. Whether you need improved insulation, buoyancy, impact resistance, or structural integrity, we have the expertise and technology to deliver tailored solutions that meet your exact specifications.
Contact us today to discuss how our foam solutions can add value to your products and help drive your project forward.