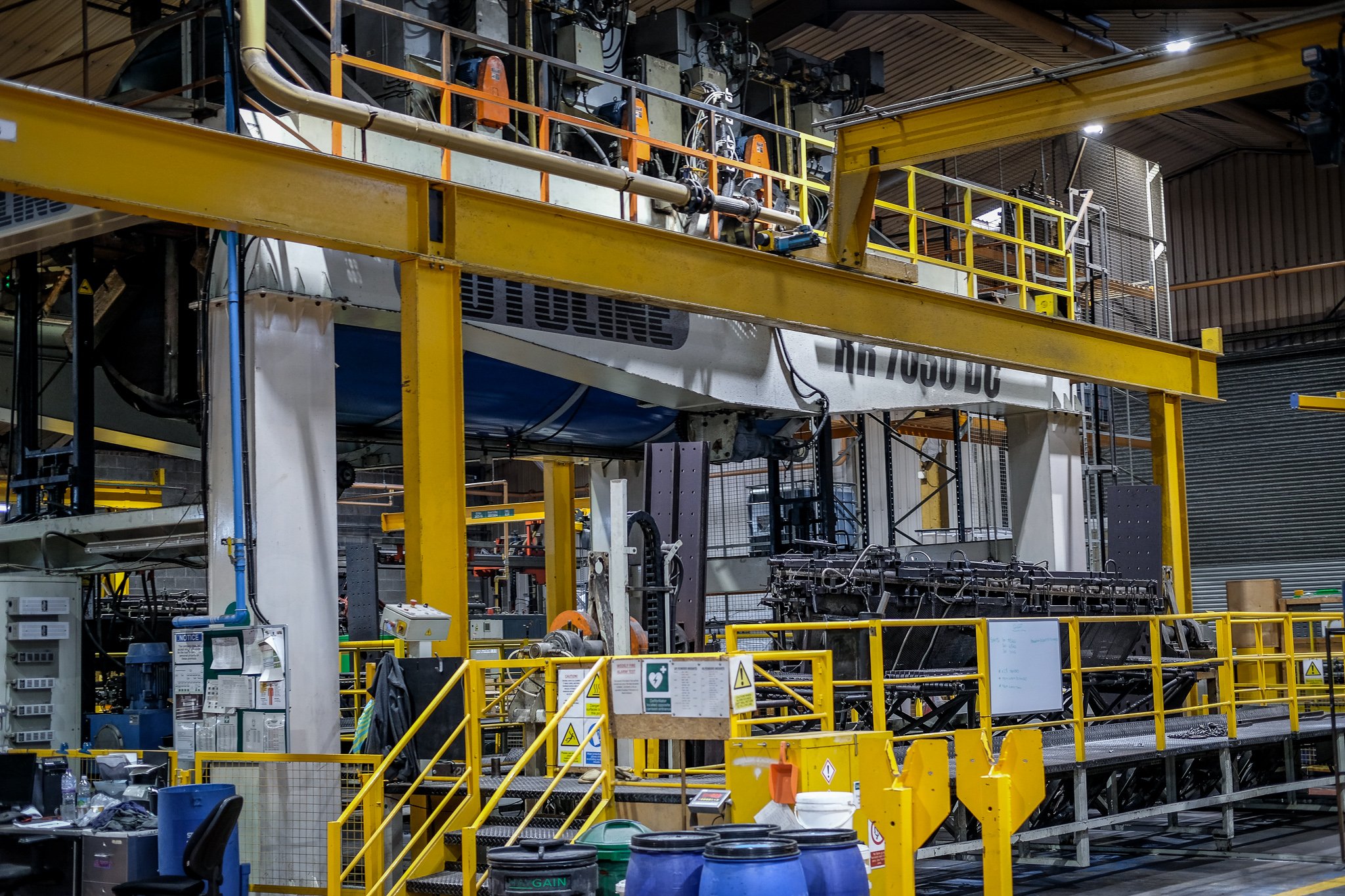
ROtoMoulding Process
Rotational moulding, also known as rotomoulding, is a manufacturing process that creates seamless plastic products that are used across a huge range of industries.
What is Rotomoulding?
What we know today as rotational moulding was first introduced when R. Peters patented the first process in late 1855 in Britain as a method of laying a material by use of a rotating mechanism that produced “two centrifugal motions at right angles to each other”. This has become more and more efficient over the decades to the way we process today, however the most communally used material today, polyethylene, was only discovered by mistake in 1933 by Eric Fawcett and Reginald Gibson, while working at Imperial Chemical Industries (ICI) at the works in Northwich, England.
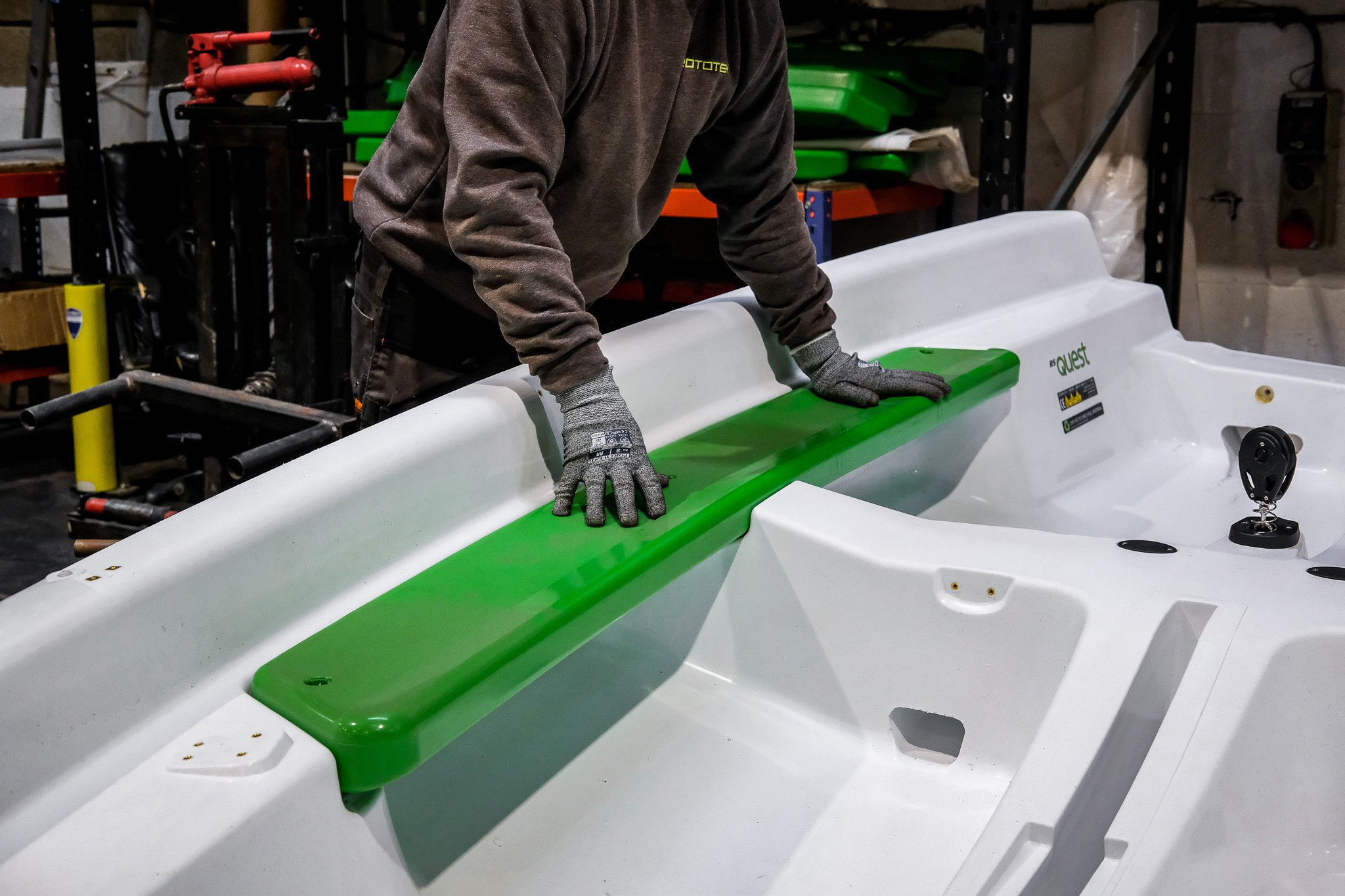
It's strange to think that there is almost no limit to rotomoulding’s application with the majority of rotationally moulded products being made from a material found by mistake in the UK. It is behind a vast array of products that facilitate our everyday lives and the businesses that support them; from medical equipment to toys, car parts to packaging, street furniture, marine offshore buoys, oil and water tanks for storage, and traffic bollards, right through to leisure products like dinghies and kayaks. Other manufacturing methods do not have the capabilities or the adaptability of rotomoulding to produce these items, in terms of the complexity, the shape of the tooling and the variety of the parts that can be designed.
Rototek has been one of Europe’s leading technical rotational moulding companies for over three decades, now operating across two manufacturing sites in Nottinghamshire, with over 250,000 square feet of production space. Our scope of expertise ranges across varying scales and complexities, from our own product range to custom projects, with our 20+ machines currently manufacturing over 100,000 products per year.
Rototek are the only UK rotational moulding company that has committed to our new production facility being 100% electrical heated tooling – a first in the industry. As a B Corp company who are committed to sustainability, we want to drive our industry towards electrically heated tooling and away from reliance on gas.
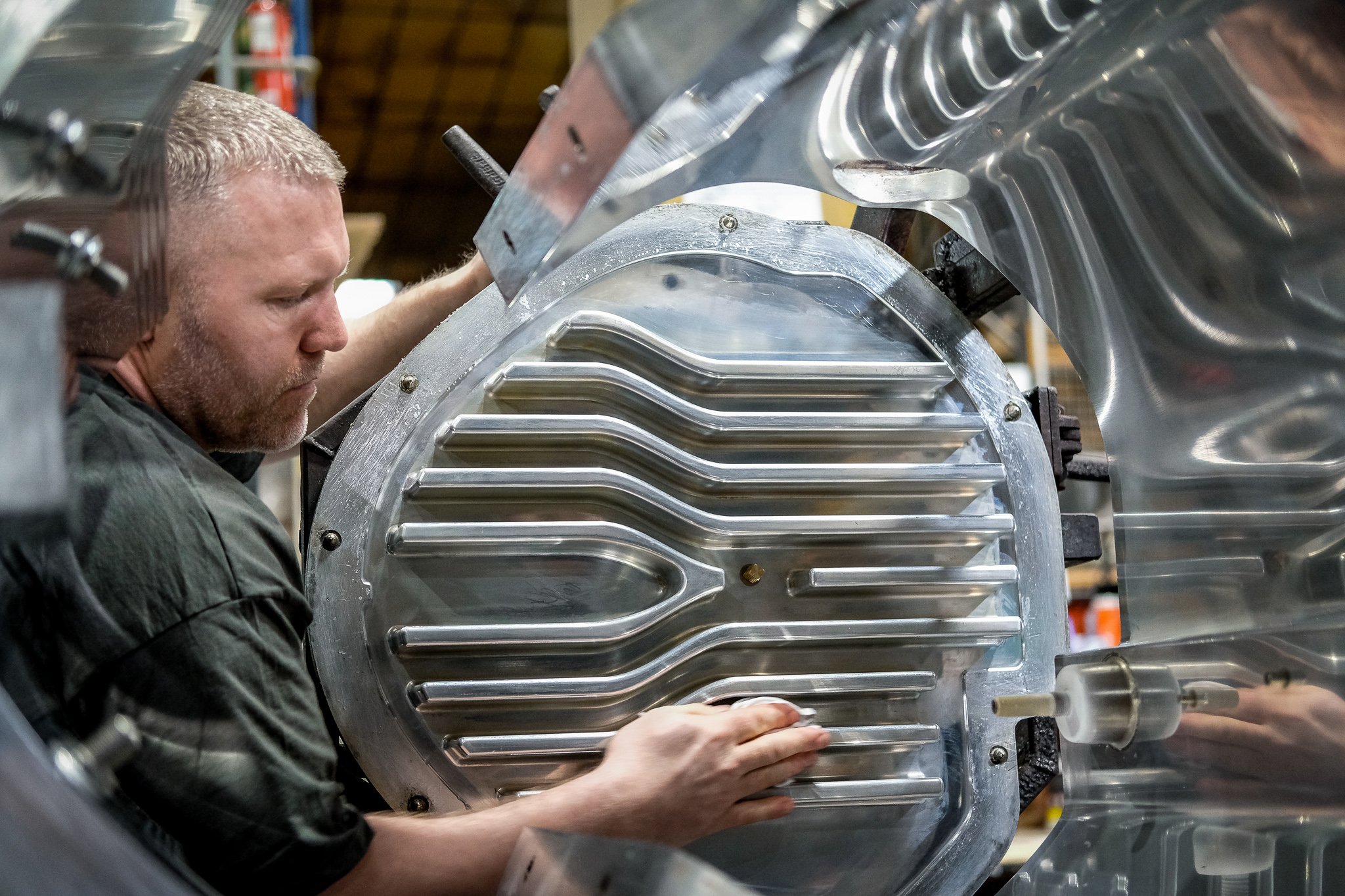
The Rotomoulding Process
Rotomoulding involves filling an aluminium or steel mould with a set weight of a polymer that will lay at the programmed positions within the tool when heated. It then solidifies when cooled. A very high percentage of the materials used are compounded in powder form and heated while the tool is slowly rotated on two axes. Polyethylene is invariably the most prominently used material because it is highly versatile and relatively easy to grind to a powder in ambient temperatures. As the polymer melts, it attaches in either a uniform thickness or a set thickness that has been programmed to the wall of the mould. Once cooled, with either air or a cool mist of water, the resulting part will be hollow in form and highly durable – this is then removed (demoulded) from the mould.
In principle, rotational moulding as a concept is reasonably straightforward, but the reality is that there are significant complexities to the process, such as the multiple variables that can affect manufacture and the quality of the end product. In the industry we call this a “Black Art” and each product will react differently. Among these different variants you will have ambient temperature and humidity having a bearing on quality, so it’s imperative that the heating power of machines is adjustable to the different materials and temperature requirements. Machines will also vary in terms of the size and movements of their rotating arms from biaxial to a rock and roll movement, still having two centrifugal motions at right angles to each other. This allows us accommodate mouldings from 100mm x 100mm to 7.0 meters x 3.0 meters.
As such, machines come in a range of shapes and sizes, almost as diverse as the applications we mentioned earlier, and are geared towards different end products. The clamshell machine is a single arm rotomoulding machine that generally takes up less space than other moulders and is low in cost compared to the size of products made. Shuttle machines have two arms that move the moulds backwards and forwards between heating chamber and cooling station and are also available in smaller scale.
In comparison, swing-arm machines can have up to four arms, each arm moving biaxially and independently of each other. Manufacturers can run different parts of the process on the other arms of the machine, for example if a part requires a longer heating or demoulding time, or carry out maintenance work, without interrupting production. Carousel machines are also available with three or four arms that can move independently, allowing different-sized moulds, and therefore different products, to be rotated simultaneously.
Rock and roll machines are specialised clamshell or shuttle machines, with either one or two arms, designed to produce predominately long, narrow parts, with a large length-to-width ratio.
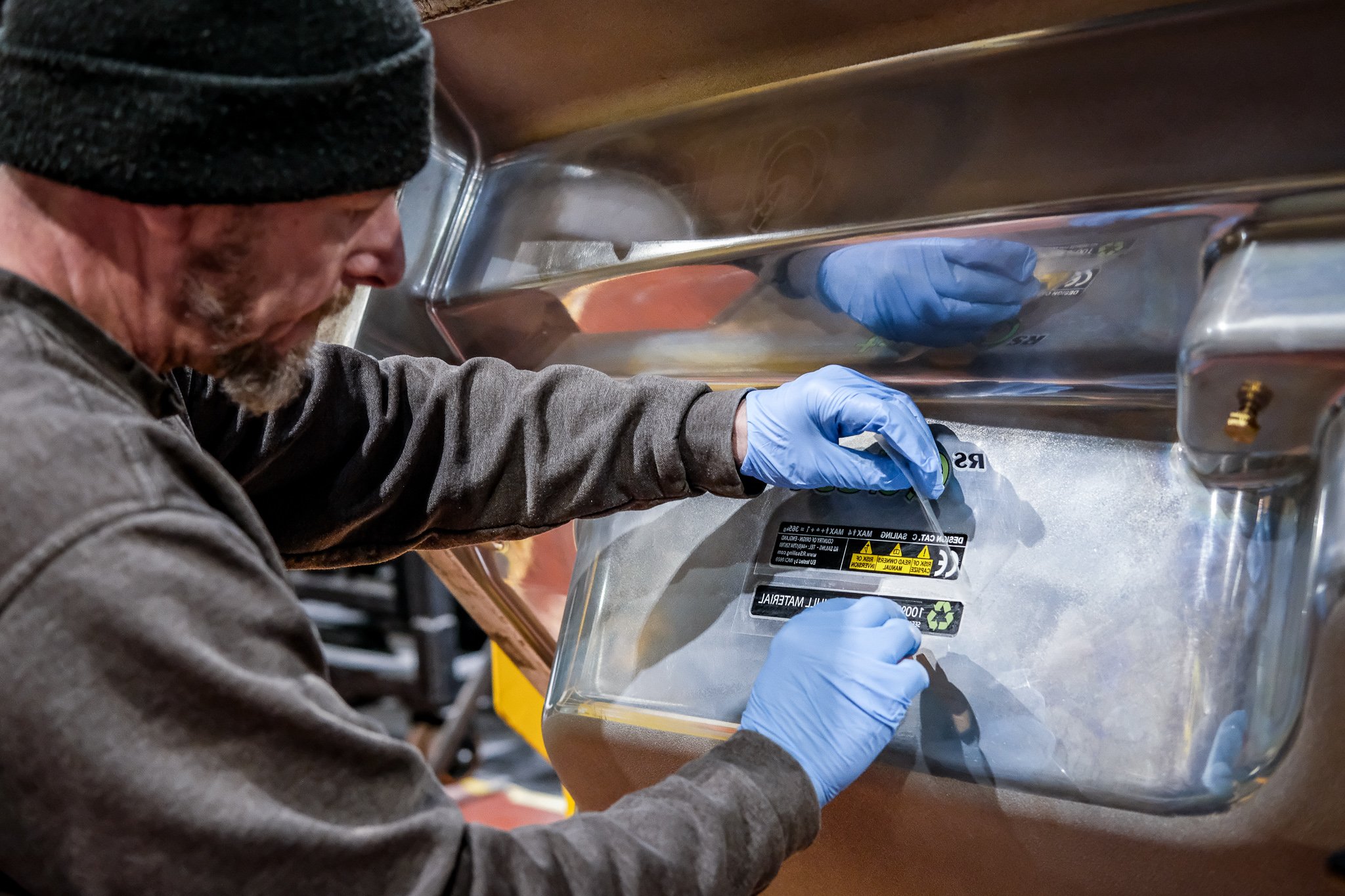
Advantages of Rotomoulding
Using the most sophisticated of varying controls, we are able to monitor parameters such as rotation speeds, internal temperature, material dispersion and wall thickness, unlike the majority of other moulders. We have been using internal temperature monitoring for over 25 years, which has taken away the inefficiencies that cause a great deal of variation in the quality of end products. This removes the majority of issues that were prominent when much of the process was largely determined by the experience of the operator, in terms of deciding when to take the part out of the oven and remove it from the mould. The technology we have embedded into our processing has, however, greatly reduced the trial and error, with far improved monitoring available of variables like the temperature and humidity mentioned above throughout the entire processing of the products.
The resulting efficiencies, along with the technologies available to mould different parts simultaneously, with minimal loss of production and the low cost of moulds, means that modern rotomoulding is a very cost-effective production process. There is also minimal waste, minimal off-cuts, and the nature of the materials used means that anything that is wasted can be recycled. Rototek is also innovating the process, by developing its own robotic and electrically heated tooling with selected partners, to ensure continuous improvement to the environmental viability of the manufacturing process.
Of course, the process’s flexibility is another key advantage. From small components for automotive assembly lines, to large, hollow parts such as oil tanks, there are countless products whose production is made much easier by rotomoulding than by any other method. Products are strong and the constant rotation of the mould ensures consistent wall thickness throughout the product, with minimal risk of structural failure in stress-concentration points and low chance of defects.
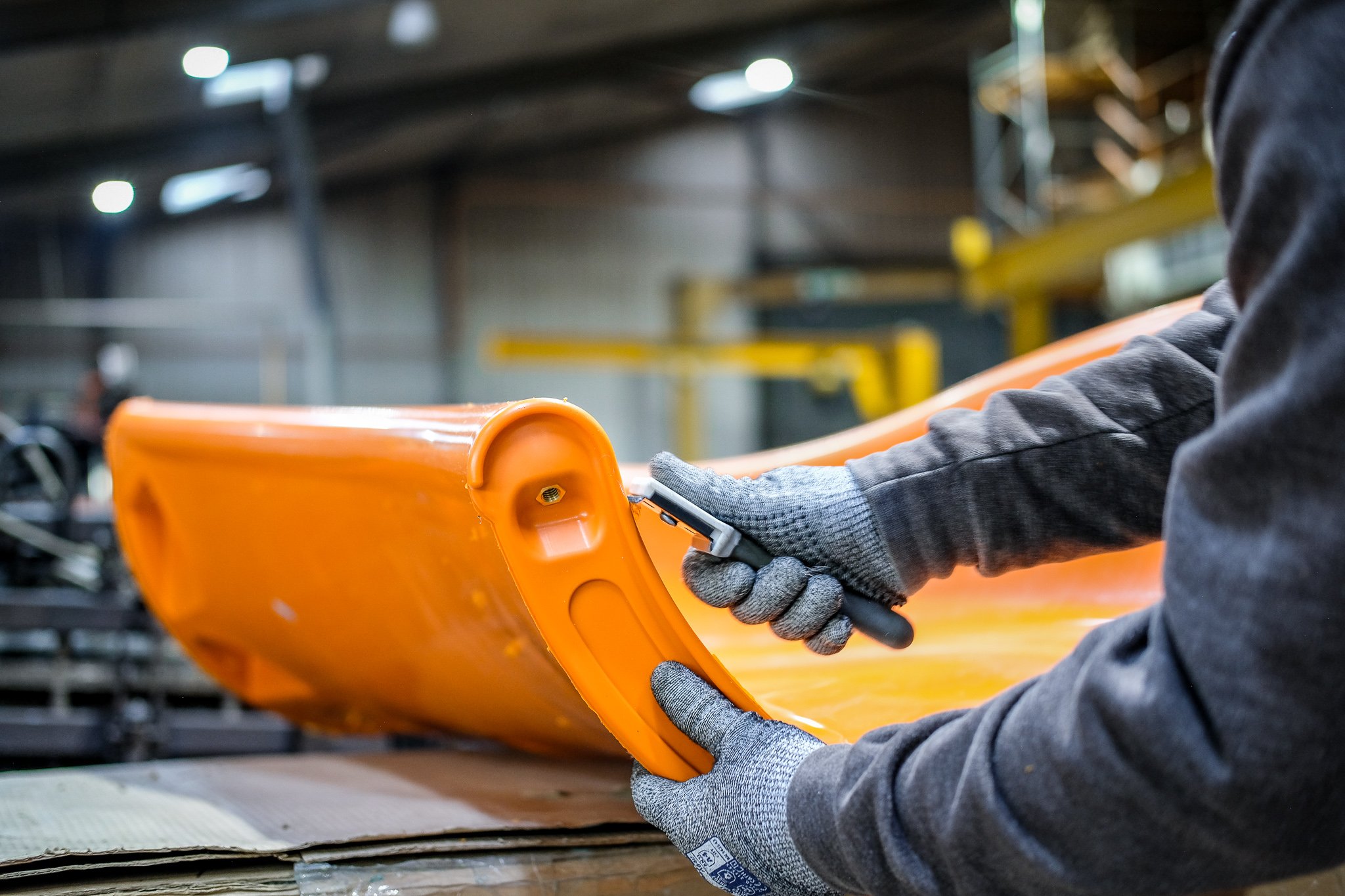
Disadvantages of Rotomoulding
Where cost inefficiencies have historically inhibited the industry, so too have time inefficiencies. Indeed, the long cycle times of heating and cooling products have been criticised, since only one or two cycles can be completed each hour, limiting production volumes. The cooling time also increases both financial and environmental costs.
We have conducted a great deal of research in improvements to the process, with fast cycling materials, and are totally committed focus on reducing these times. We also use in-mould pressurisation and have been able to reduce cooling by a minimum of 22%. By applying cold air pressure internally to the mould during the heating phase, we are able to produce parts with fewer bubbles in less time than at atmospheric pressure, thanks to the higher speed at which the polymer particles process during the oven stage. This also comes with the need to monitor this build-up of pressure and is balanced during the process. This has not been adopted on a large scale by most rotomoulding manufacturers, but this investment in time and testing will reduce the disadvantages we currently face against other manufacturing processes.
The nature of the process can restrict what can be put in the moulds, in terms of the physical properties of the materials used. As well as being easy to grind into a powder, the polymer must have a high thermal stability and flow characteristics. The polymer will also come into contact with oxygen in the mould, which can lead to deterioration of the polymer, so a number of antioxidants are added. This is also important to prevent deterioration. Polyethylene and polypropylene are relatively low-cost materials with desirable properties and are the materials of choice for rotational moulding.
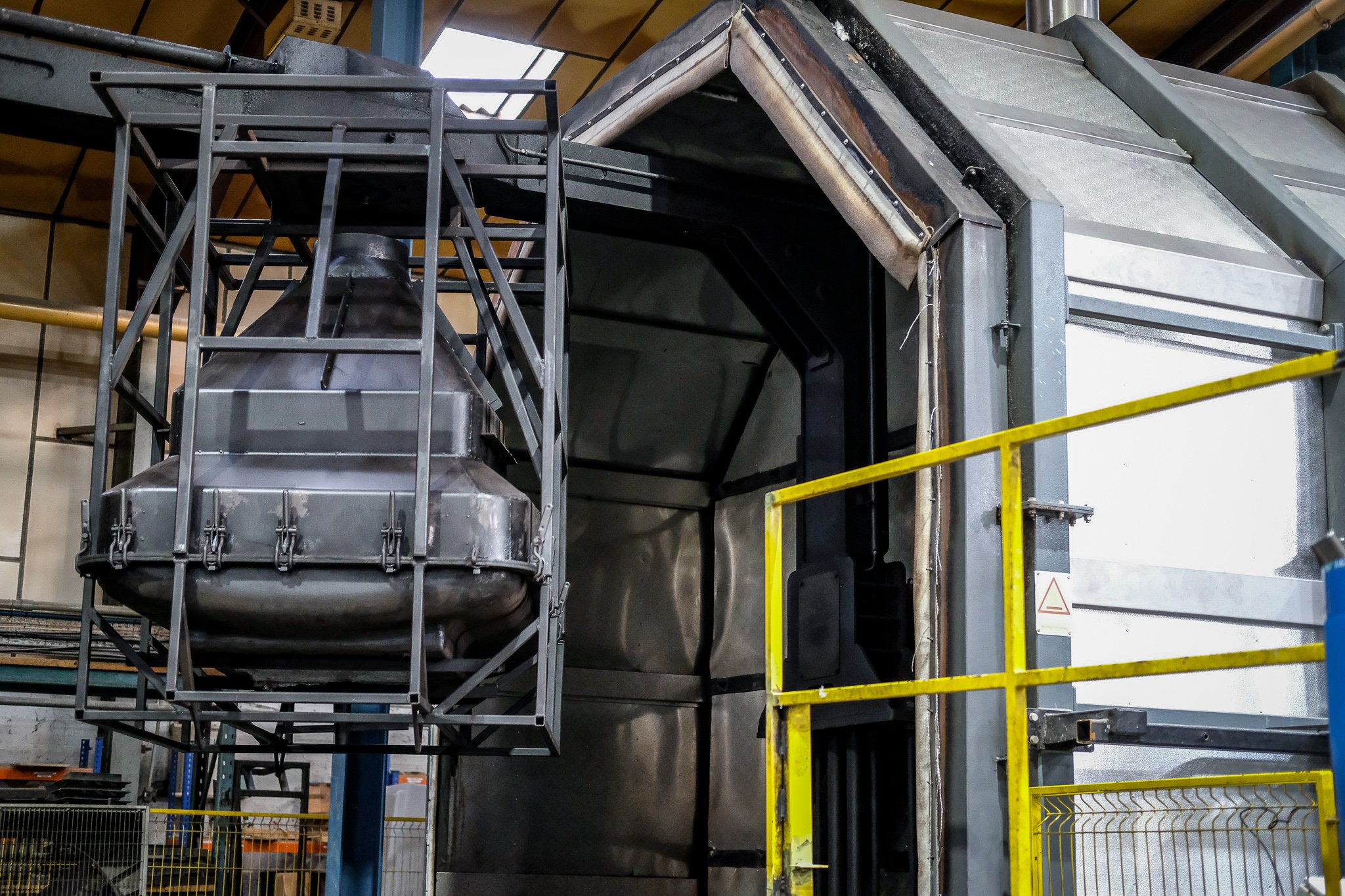
Looking ahead
Whether it’s creating durable components for industrial use or designing bespoke consumer products, rotomoulding offers a relatively cost-effective solution to manufacturing needs. There used to be a drawback in the quantity of items that could be produced, given long cycle times of conventional rotational moulding, but with investment into electrical moulding and automations we can now start to look at mass-production thresholds. The versatility in terms of the range of products that can be made, and the durability of those products make it the go-to process for countless parts and components across multiple industries; from marine and medical to leisure and lifestyle.
Contact us to find out more.