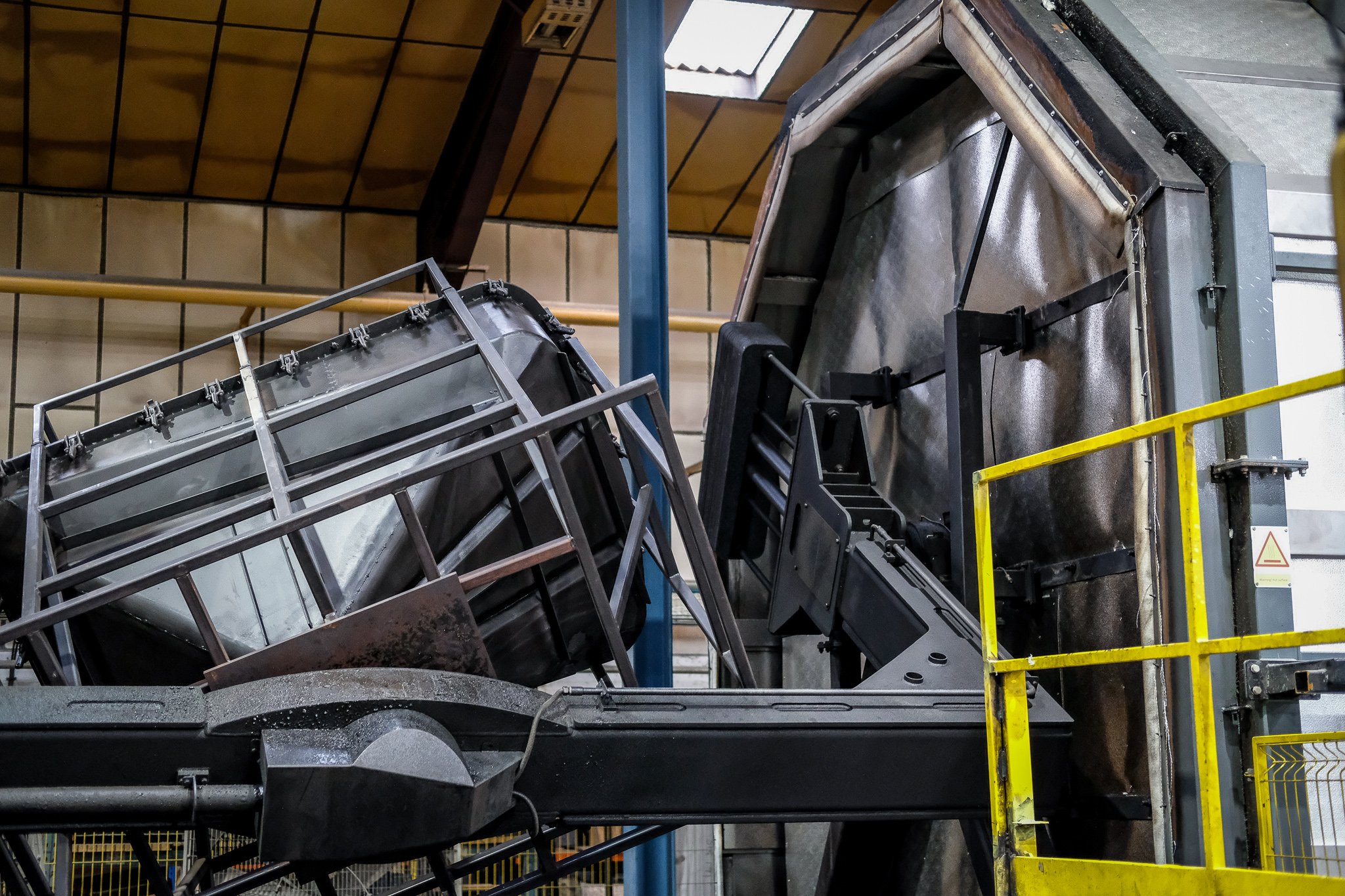
Frequently Asked
Questions
Curious About Rototek?
Find Your Answers Here.
Rototek is a leader in rotational moulding and custom plastic solutions. We're committed to providing exceptional customer service. This FAQ page addresses many of the questions we hear from our valued customers, designed to provide clear and concise answers for your convenience. If you don't find the answer you need or have specific enquiries, please reach out to us, our team is ready to help.
-
The cost-effectiveness of rotational moulding varies depending on the specific application and production requirements.
Rotational moulding typically offers lower tooling costs compared to other plastic manufacturing methods. This is because the process does not require tools to withstand high pressures, and the moulds are designed for hollow parts without the need for complex core sections.
For small to medium production runs, rotational moulding can be more economical due to its lower initial tooling investment. However, for large-scale production, methods like injection moulding may offer lower per-unit costs despite higher tooling expenses, owing to their efficiency in high-volume manufacturing.
Rotational moulding provides significant design flexibility, allowing for the creation of complex shapes and seamless, hollow parts. This capability can lead to cost savings in assembly and fabrication, as multiple components can be consolidated into a single moulded piece.
The materials used in rotational moulding, such as polyethylene, are often less expensive and offer desirable properties like durability and chemical resistance. This can contribute to overall cost savings, especially for products requiring these material characteristics.
In summary, while rotational moulding can offer cost advantages in tooling and design flexibility, the overall cost-effectiveness depends on factors like production volume, product complexity, and material requirements. It's essential to evaluate these aspects in the context of your specific project to determine the most economical manufacturing method. -
We can manufacture anything from small 100m cubed containers to 7-metre mouldings.
-
At Rototek, our design process starts with an initial concept discussion and feasibility analysis to determine if your product is suitable for the rotomoulding process. From there, our experienced in-house design team will refine and optimise the design specifically for rotomoulding. Whether you have a fully developed concept or just a rough idea, we’ll work closely with you—or alongside your design team—to bring your vision to life.
Using advanced Computer-Aided Design (CAD) software, we create precise 3D models of your product. For more complex or larger designs, we produce prototypes through 3D printing or wooden modelling. This vital step ensures the design is validated and allows for any necessary adjustments before moving into production, giving you confidence in the final result.
For more detailed information on our design services, please visit our Rotomoulding Design page. -
Rotational moulding primarily utilises polyethylene (PE) due to its versatility and ease of processing, as well as its recyclability. Various forms of PE, such as linear low-density polyethylene (LLDPE) and high-density polyethylene (HDPE), are also commonly used.
-
Rotational moulding offers several environmental advantages over other plastic moulding processes, making it a more sustainable manufacturing choice. One of the key benefits of rotational moulding is that it produces virtually no waste - every bit of raw material is used during the moulding process, ensuring minimal excess and reducing the need for additional trimming or processing.
Polyethylene, the primary material used in rotomoulding, is highly recyclable and it can be reprocessed to create new products or used in other moulding techniques. Polyethylene is not only versatile but also cleaner to produce and mould compared to many other polymers. At Rototek, we have the capacity to use recycled powder if this is appropriate for your product.
In December 2024 our first all-electric oven arrived at our Newark factory, a huge milestone in Rototek's sustainability journey. This innovation enables us to manufacture products with a substantially lower carbon footprint compared to traditional gas-powered ovens. We’re proud to be the only contract moulder in the UK offering this service!
When choosing to work with Rototek, you are also choosing to work with a B Corp Certified company, meaning that we are part of a global community of businesses that meet high standards of social and environmental impact. -
B Corps are businesses that meet high standards of social and environmental impact. Businesses are assessed across 5 main pillars: governance, workers, community, environment and customers, needing to achieve over 80 points to gain certification. We are proud to have achieved 92.3 points, putting us well above standard businesses in the UK. It doesn’t stop here though, part of becoming a B Corp means committing to continuous assessment and improvement, as all B Corps must undertake the assessment and verification process every three years to demonstrate that they are still meeting the B Corp standards.
Read more about our commitment to sustainability here. -
Rototek stands out from other rotational moulders by offering a complete, end-to-end service, from design to delivery. With over 20 machines across two sites, we can produce everything from small 1-litre containers to large 7-metre mouldings. Our in-house design team works closely with you to refine your ideas, ensuring efficient production and top-quality results. We’re ISO 9001 certified and proud to be a B Corp, reflecting our commitment to exceptional standards and sustainability. With a 99.7% success rate in delivering products that meet customer expectations, Rototek is the trusted choice for innovative and reliable rotational moulding solutions.
-
At Rototek, we recommend tooling options tailored to your project’s needs. Aluminium is our go-to choice for its durability, precision, and lightweight handling, whether cast for intricate shapes or CNC-machined for high accuracy. For larger, simpler designs, steel tooling is a robust alternative. Our team is here to help you select the best option to ensure quality and efficiency for your project.
-
The lifespan of a rotational moulding tool varies based on factors like material choice, design complexity, and maintenance practices. A well-maintained rotational moulding tool can typically last for 10 to 20 years or produce 10,000 to 30,000 cycles, depending on the material, usage, and care it receives.
-
The maximum temperature tolerance of rotationally moulded plastics depends on the specific material used. At Rototek, we commonly use polyethylene due to its versatility and durability. Polyethylene can typically withstand temperatures up to 60°C (140°F) continuously. For applications requiring higher temperature resistance, other materials like nylon or polypropylene may be considered, each offering different thermal properties. Our team can guide you in selecting the appropriate material to meet your product's specific temperature requirements.
-
Rotational moulding is ideal for manufacturing tanks as it naturally creates seamless, hollow parts with uniform wall thickness and no weak points. This ensures durability, lightweight design, and versatility in size and shape. At Rototek, we leverage this process to produce high-quality, custom-designed tanks for a variety of applications.
-
Choosing between rotational moulding and blow moulding depends on your product needs. Rotational moulding is ideal for complex, durable items with uniform wall thickness, like tanks and outdoor furniture, offering design flexibility for intricate details. Blow moulding suits high-volume production of simpler, lightweight products, like bottles, with faster cycle times but less detail and uniformity. At Rototek, we specialize in rotational moulding and can guide you to the best solution for your project.
-
Like with blow moulding, choosing between rotational moulding and injection moulding depends on your needs. Rotational moulding is best for complex, hollow products like tanks, offering design flexibility and lower tooling costs, ideal for small to medium runs. Injection moulding suits high-volume production of precise, solid parts, with faster cycle times but higher tooling costs. At Rototek, we specialize in rotational moulding and can help determine the right process for your project.
Let us help you find the perfect rotational moulding solution. Contact us today!
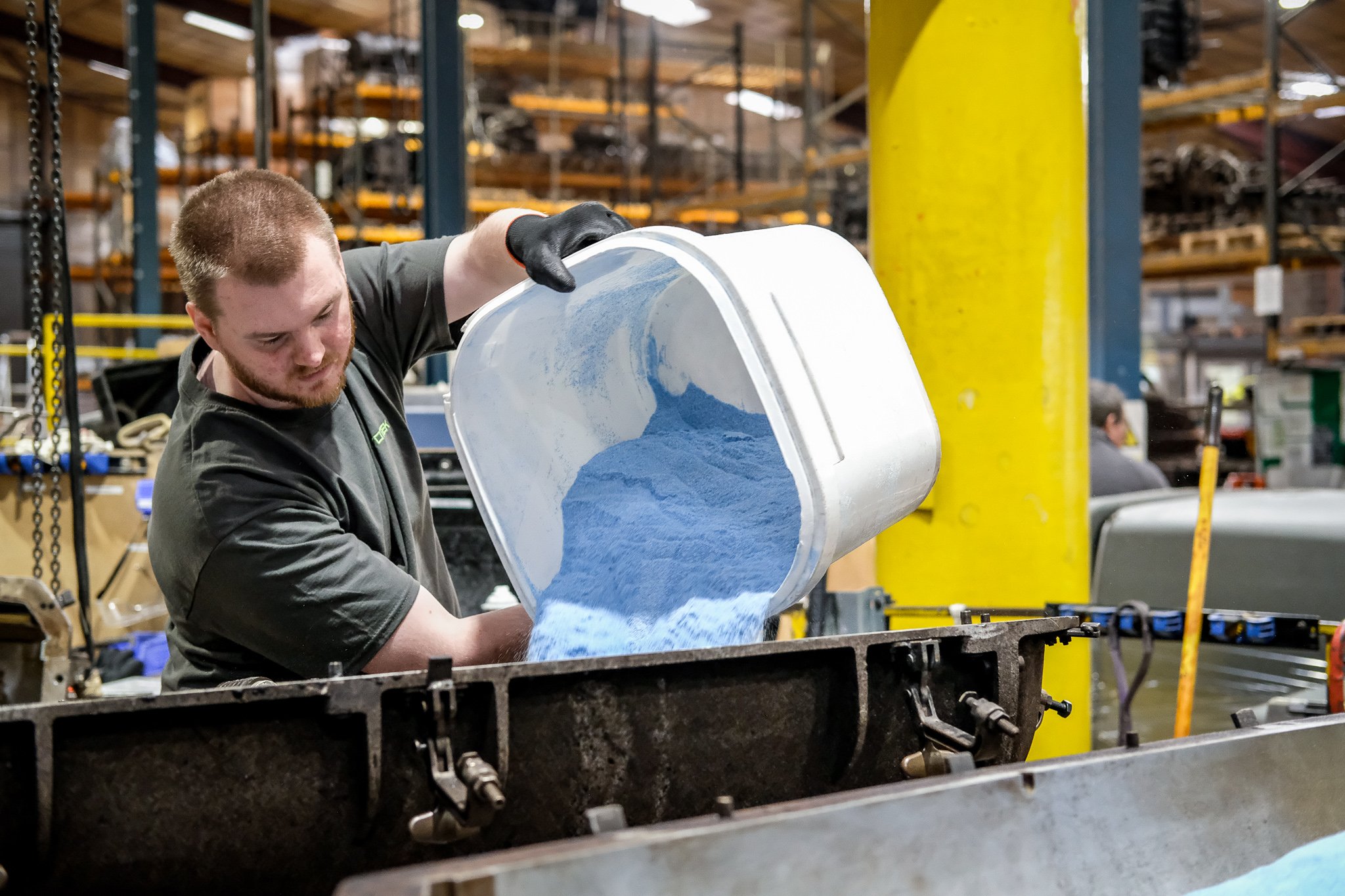
In 2023 over 99.7% of our factory-made products fulfilled our customer expectations, well above the industry standard.
We ensure quality control throughout the production process, from the materials to the final product, employing environmentally sustainable production methods and procurement practices, all supported by our ISO 9001 and B Corp accreditations.
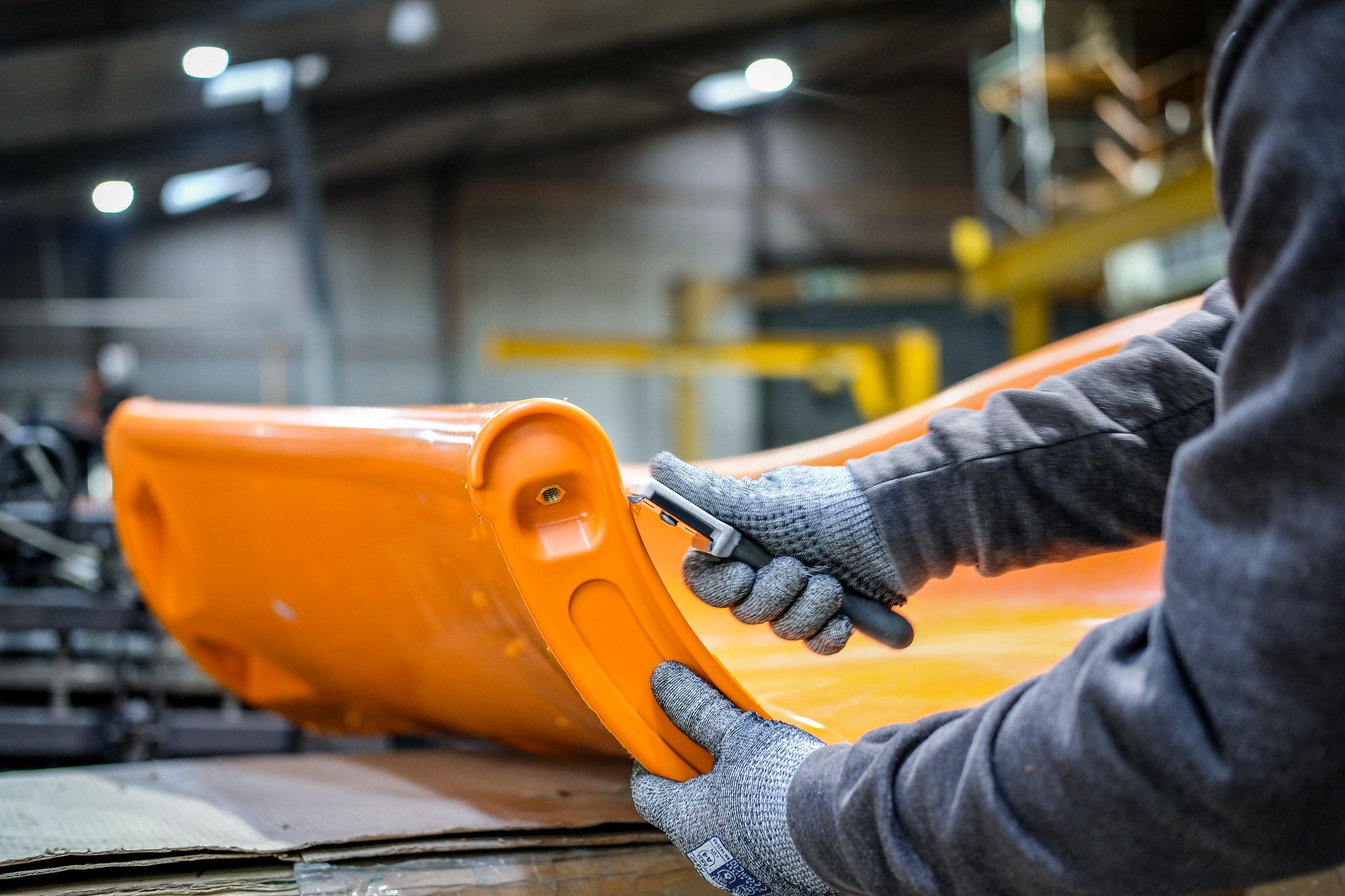
wANT to find out more?
Simply fill out the form and one of our friendly team will be in touch to assist you.