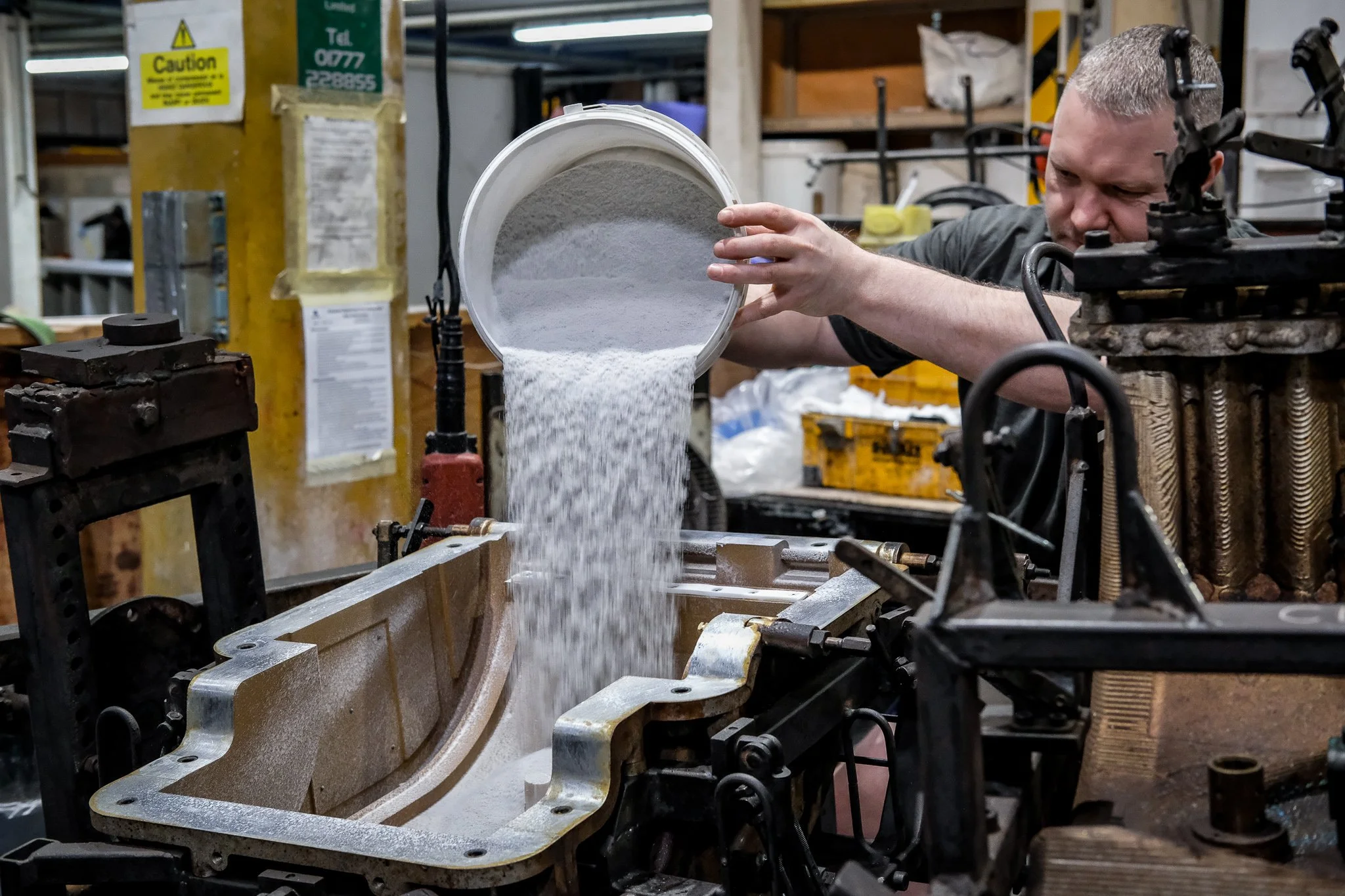
rotomoulding
Design
Introduction to Rotomoulding Design
The design stage is the most crucial part of the rotational moulding (rotomoulding) process, as it determines whether the final product will be functional and therefore successful. A key rotomoulding design principle that our expert team abide by is simplicity; their golden rule is to never overcomplicate the design. The goal is to create a design that maximises the advantages of rotomoulding, such as uniform wall thickness, strength and durability, whilst considering the unique properties the of the plastic used to ensure this aligns with the intended use of the final product.
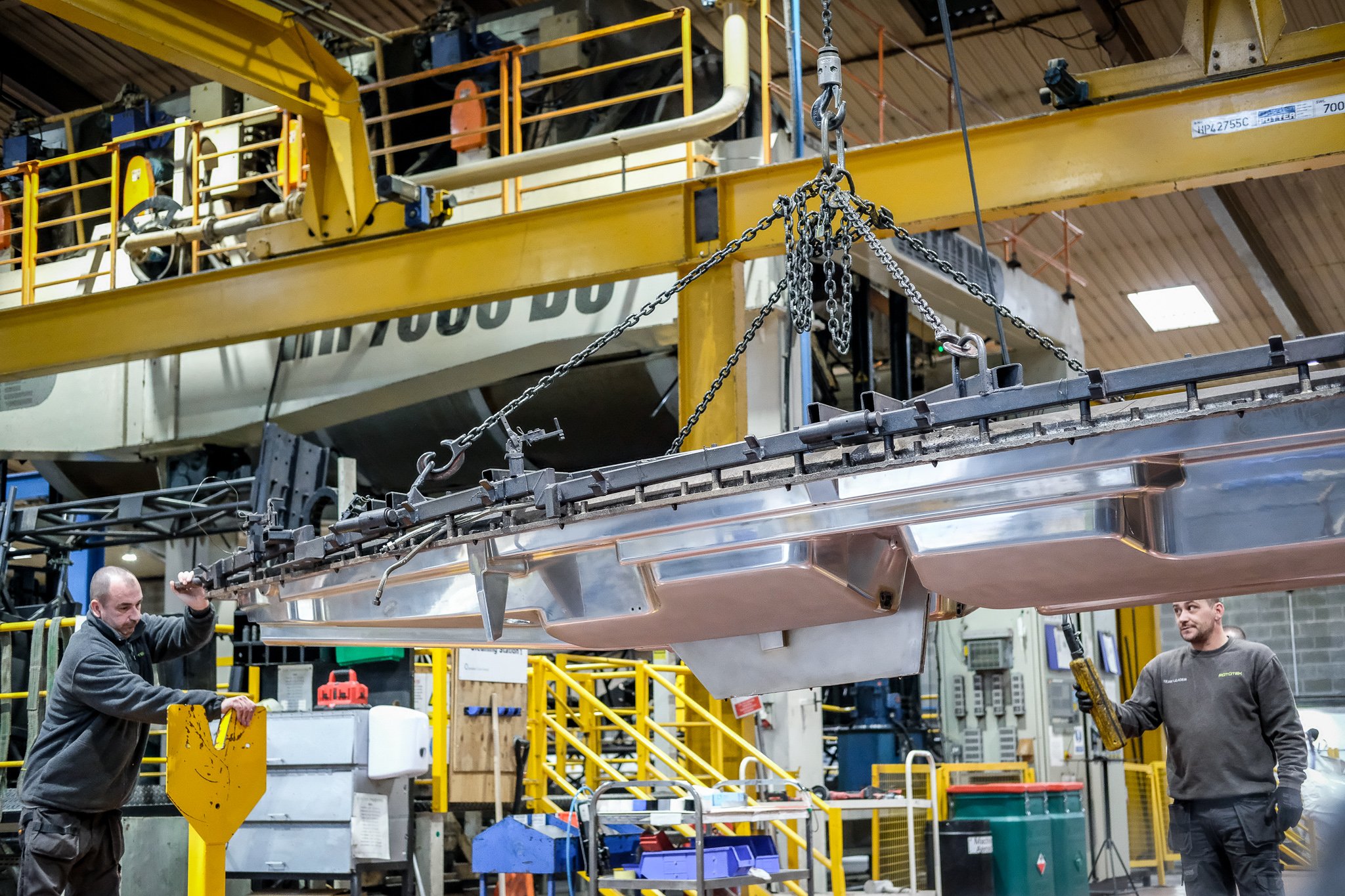
Essential Rotomoulding Design Considerations
There are many aspects to consider during the design process from material choices to the specific contours of the product. Our key design considerations are outlined below.
Uniform Wall Thickness: achieving a consistent wall thickness is crucial for the strength and durability of your final product. Although if your design requires thicker and thinner areas within the product, for example in a sailing dinghy, our advanced rock & roll machines can allow for this.
Avoid Large Flat Surfaces: large flat areas in your design can lead to distortion due to the uneven cooling rates of the material. Integrating ribs or gussets not only enhances your final product’s structural integrity but also helps maintain its shape during cooling, therefore reducing the potential of distortion. These elements can also be aesthetically pleasing and functional, such as embedding a company logo or textural designs.
Rounded Edges: sharp edges are avoided in rotomoulding design as the material does not flow well into tight spaces. A more appropriate design choice is ensuring the edges are radiused to facilitate better material flow and distribution, enhancing the quality and finish of your product.
Ease of Demoulding: incorporating appropriate draft angles is critical to ease the demoulding process, preventing damage to the product. Designs should aim to minimize undercuts to simplify the mould release, although certain complexities can be accommodated with our advanced tooling solutions.
Design for Shrinkage and Warping: considering material behaviours such as shrinkage and warping during the design phase helps in anticipating and mitigating these common issues.
Design to Minimize Material Usage: strategic insultation of tools in areas of your product that will be removed and scrapped afterwards can help to significantly reduce waste, making the process more efficient and sustainable. Rototek’s commitment to sustainability is evident in how we reprocess scrap materials, using them in less critical product applications where material characteristics are not crucial.
Impact of Colour and Texture: colour and texture choice plays a significant role in the product’s final appearance and functionality. While custom colours can align with your company branding, considerations such as scratch visibility on darker or glossy finishes must be addressed during the design stage.
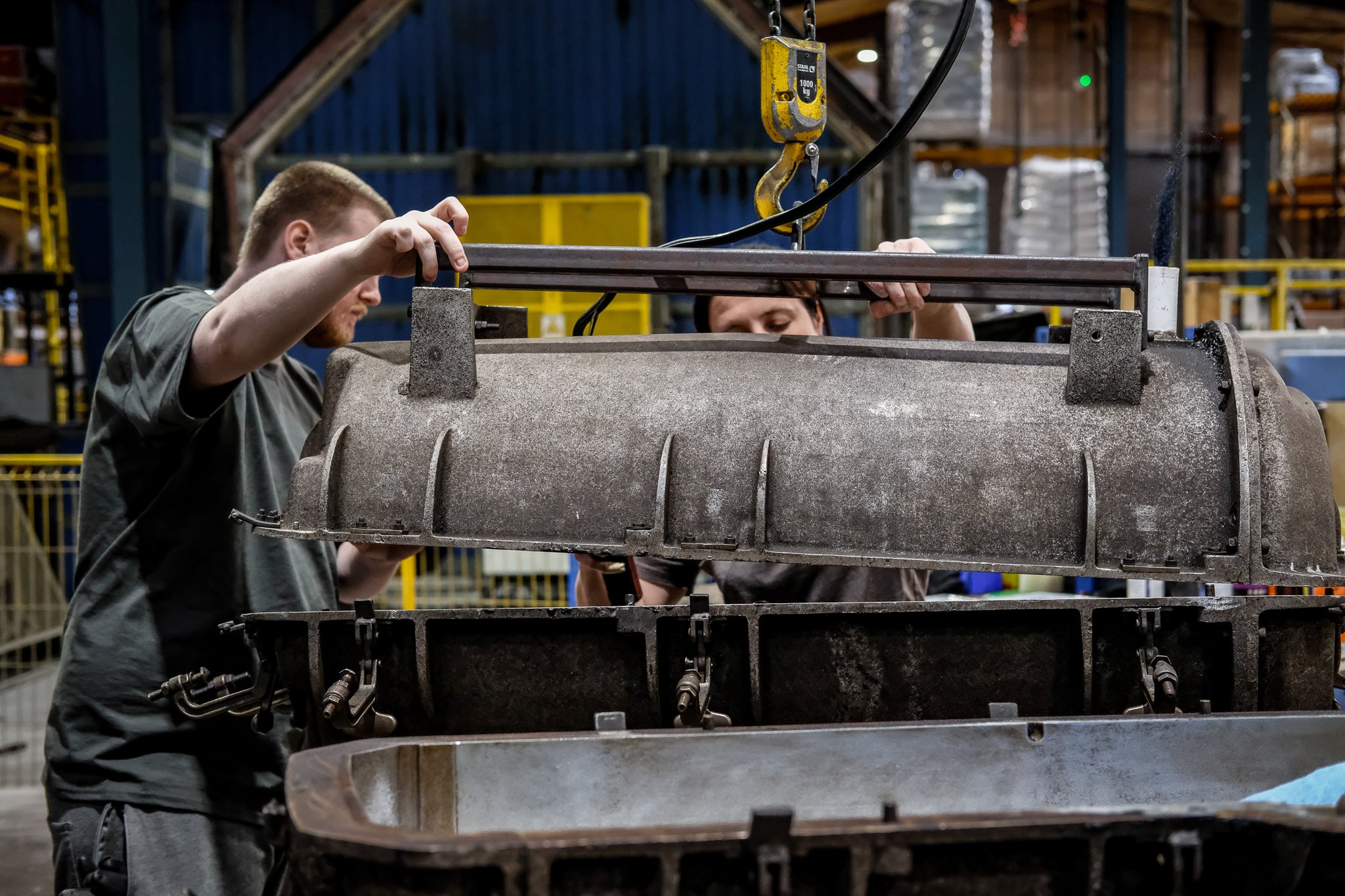
The Rototek Design Process
Designing for rotomoulding requires a balance between aesthetics and the practicalities of the material and production capabilities, fortunately our in-house design team are on hand to guide you through the process. All you need to do is come to us with an idea and our skilled team will do the rest, transforming your idea into a tangible product design.
Rototek’s design process begins with an initial concept discussion and feasibility analysis to ensure that the product is suitable for the rotomoulding
process. After the initial concept discussion, the team will optimise the design for rotomoulding, taking into account all the design considerations listed above. A key part of this optimisation is the material selection, we usually start with standard materials (eg. LLDPE) as this moulds well, comes in an array of colours and is readily available at a relatively good price. If you have specific requirements, our team can guide you to the best materials for your product.
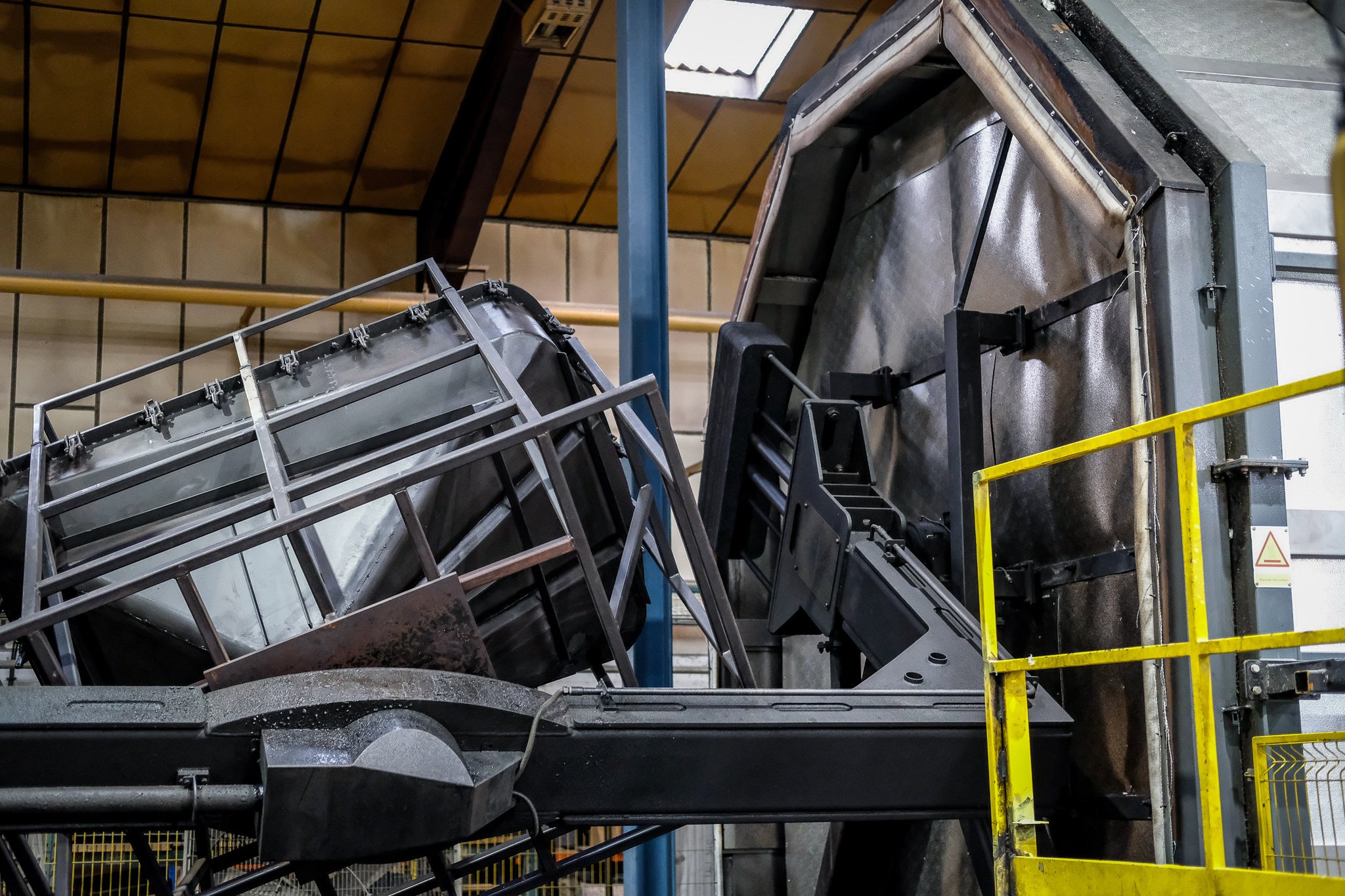
Collaborating with Client Design Teams
With over three decades of experience in technical rotomoulding, our design team can either fully create your concept or work alongside your design team to ensure your design is suitable for rotomoulding. When working alongside client design teams, communication is at the heart of this collaborative process which ensures that the design aligns perfectly with the client’s expectations and requirements for the product. Throughout this process, we will stay connected to your team through either face-to-face meetings, Teams calls, emails, whichever route best suits the needs of the project. These detailed discussions will ensure your design is aligned with rotomoulding capabilities, ensuring that every aspect from wall thickness to material choice is ideal for production.
Our design team utilize state-of-the-art Computer Aided Design (CAD) software to create detailed 3D models of your product, bringing your idea into reality. This model can be created in collaboration with your design team and helps to visualise the design before we begin creating the prototypes. Depending on the size and complexity of the product, we will create prototypes via 3D printing or wooden models; this critical step allows the team to test for design validation and make any necessary adjustments ahead of production.
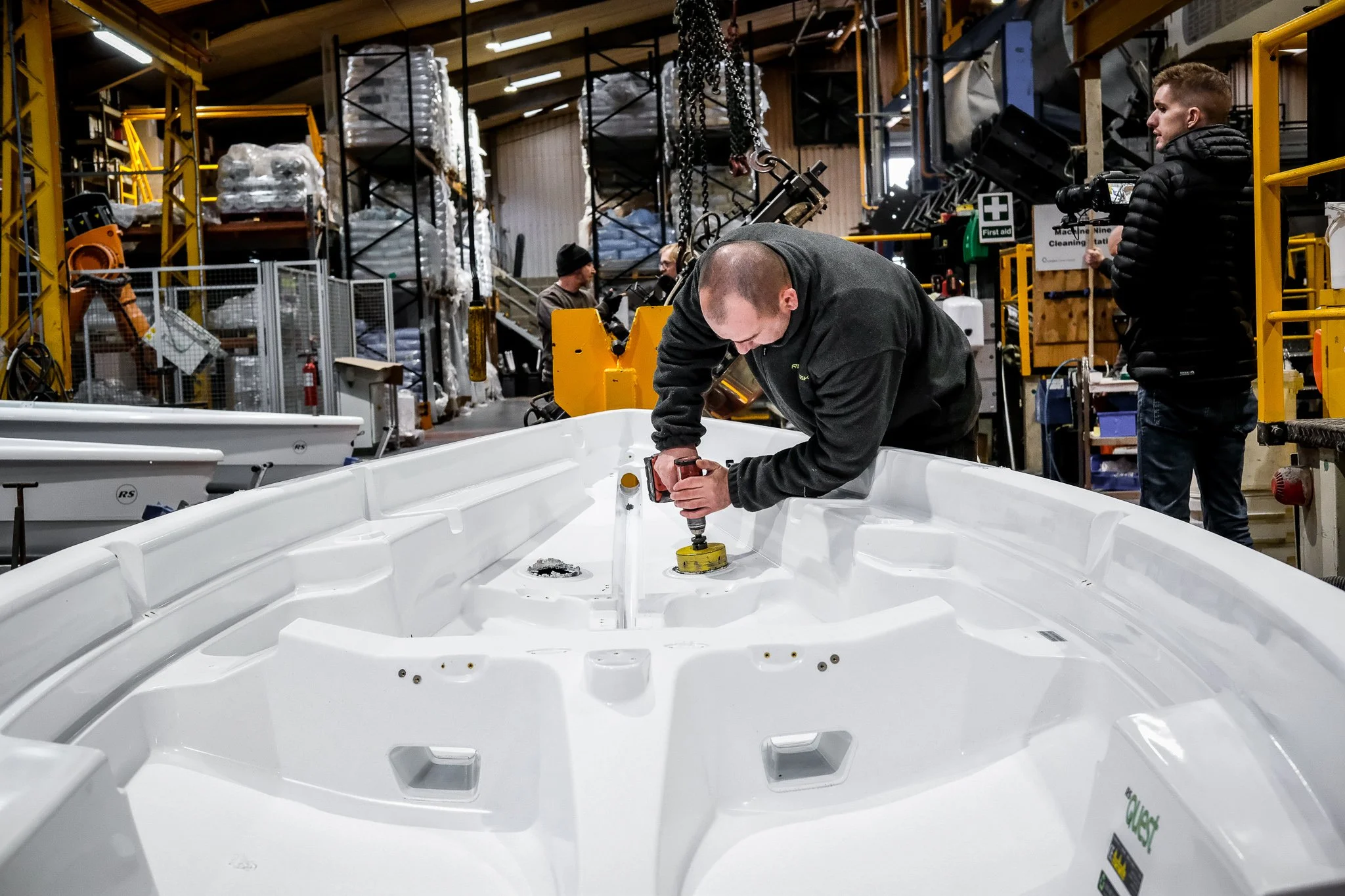
Advantages of Rototek's Design Approach
With over 30 years of experience in technical rotational moulding, our skilled team of four are purely focusing on design. Led by Ian Bingham, our team pride themselves on their communication and partnership skills throughout the design process, with their extensive background allowing them to handle complex design challenges with ease. The team ensures they don’t work in a silo; involving the production team at an early stage enhances their design capabilities, ensuring the design and tooling will work in practice in the factory. Not only does this approach enable us to find quicker solutions to any design challenges, this also empowers our team on the factory floor who feel more connected to the product once it goes into production.
Sustainability is a key priority in all our design and production processes at Rototek. As we aim to minimize waste right from the design stage, we ensure that each product uses materials as efficiently as possible. This can reduce the environmental impact of your project and improve the cost-effectiveness. Our approach aligns with the increasing demand for environmentally responsible manufacturing, and by working with Rototek you are choosing a B Corp Certified company who are investing in more sustainable production methods. If our approach to rotomoulding and design sounds like it will work for you and your project, please get in touch with Ian and the team.
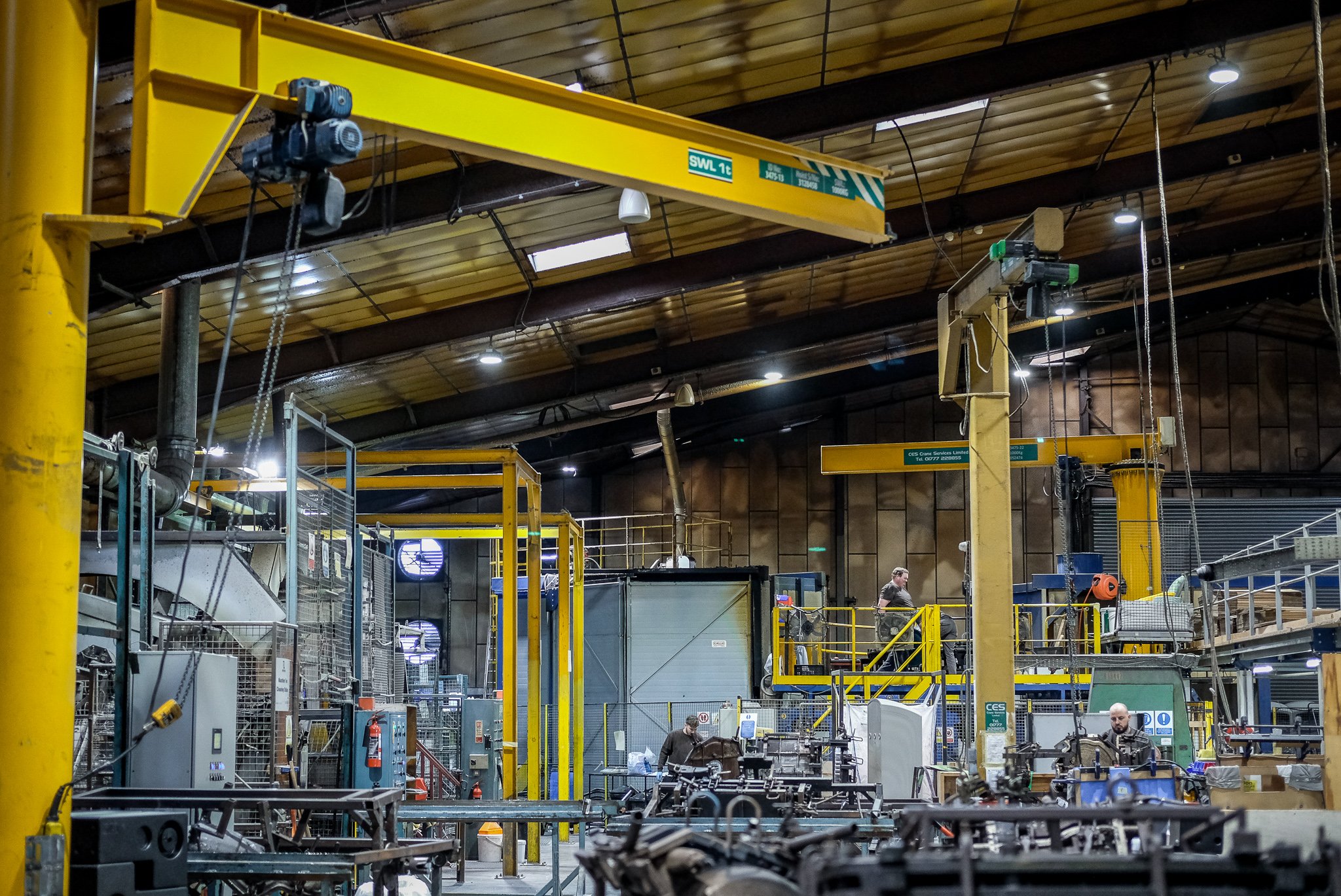
Applications of Custom Plastic Products
Our portfolio of products showcases the diversity of our manufacturing capabilities, from smaller furniture to 7m sailing dinghies, we have the capacity to create it all. Examples include: oil and water tanks, grit bins, bollards, outdoor and indoor furniture, marine applications, pump chambers/housing, mudguards, bumpers, portable toilet parts, containers, planters, privacy screenings, the list goes on! Our in-house design team loves a challenge and will work to bring your idea to reality within the capabilities of our manufacturing process.
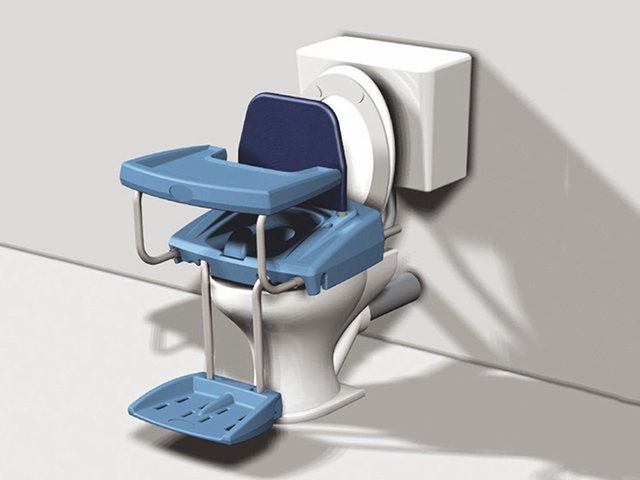
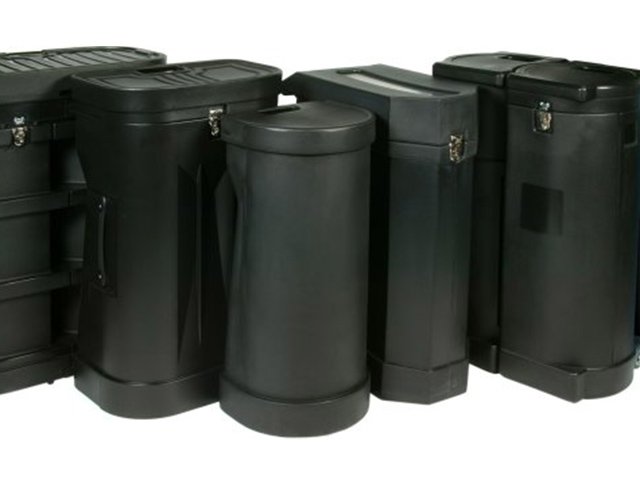
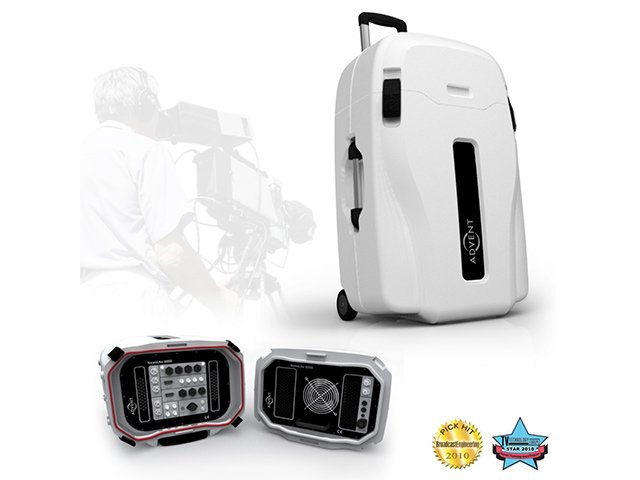
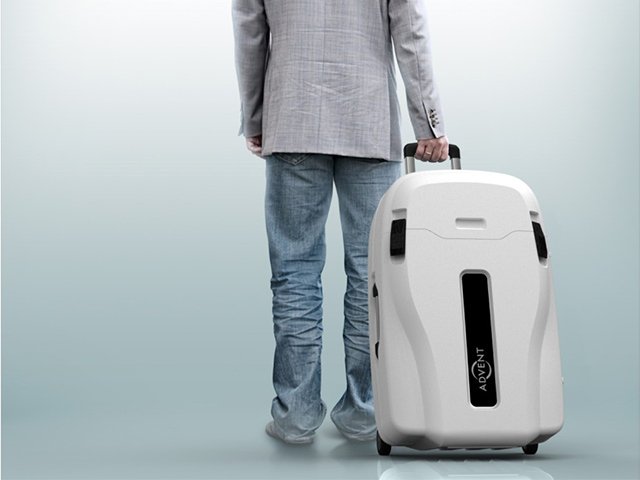
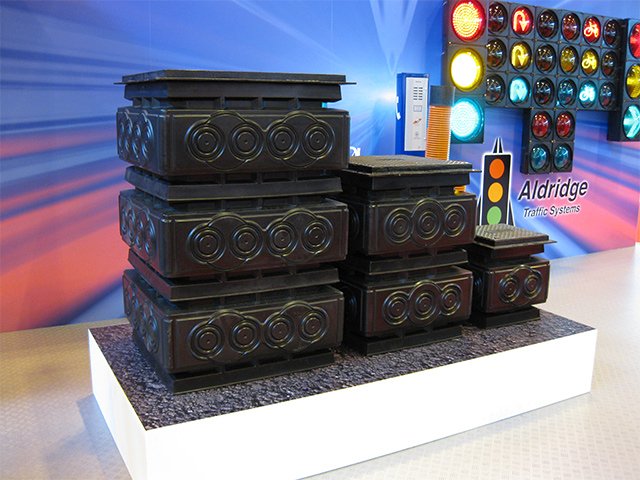
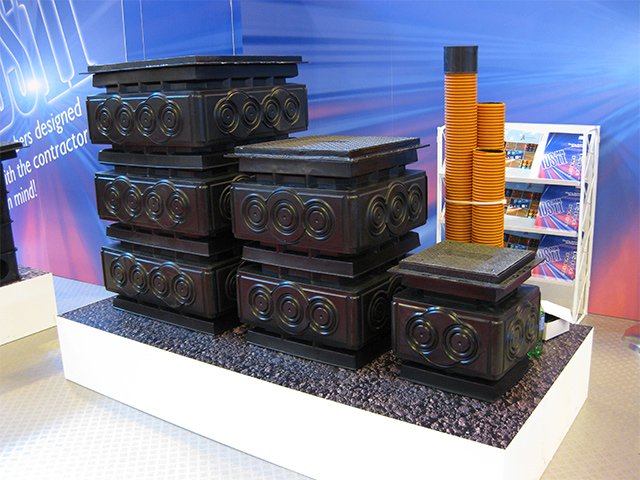
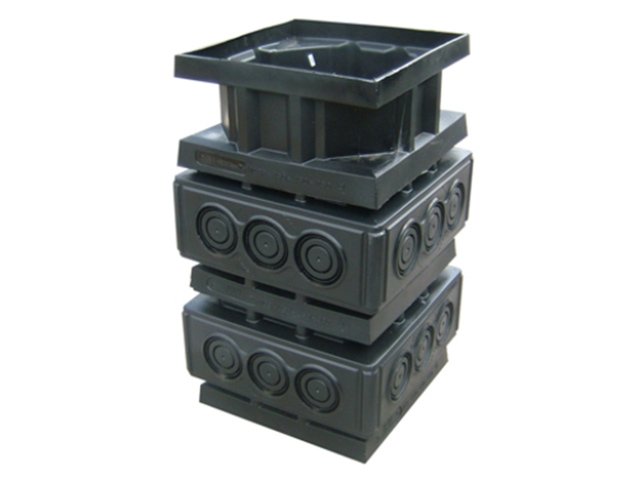
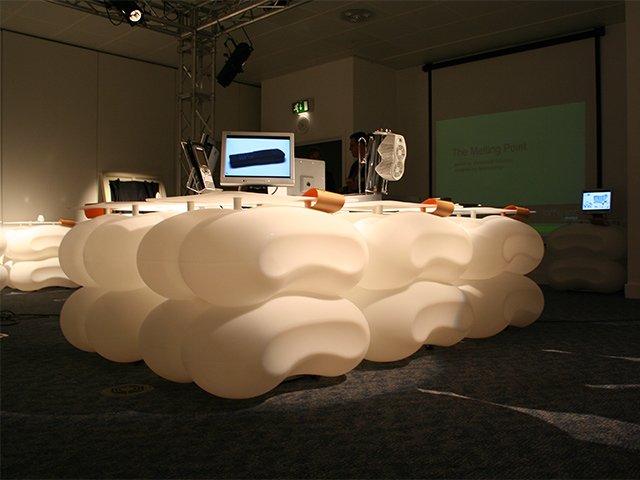
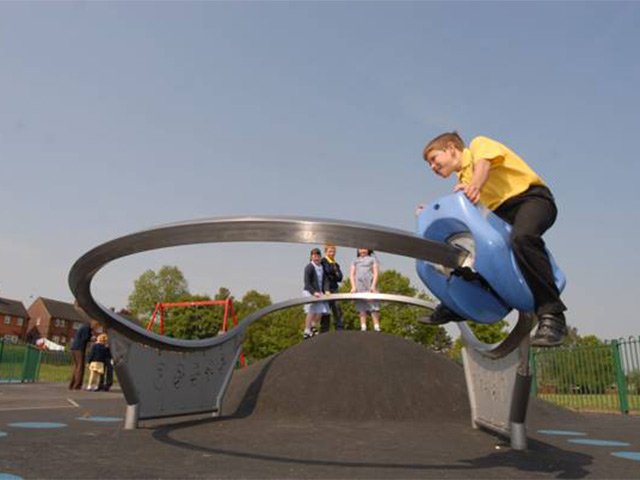
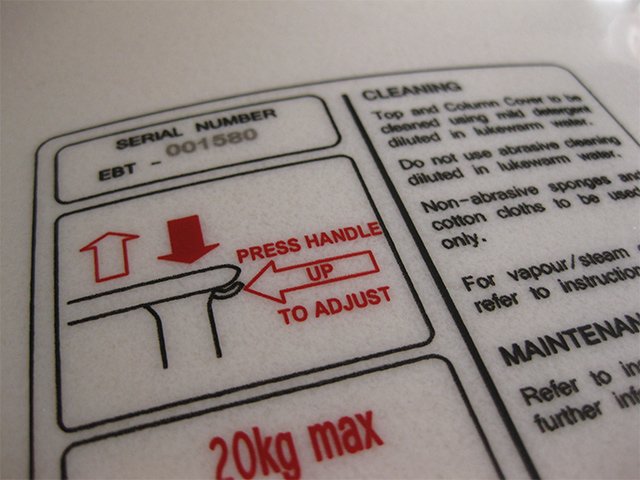
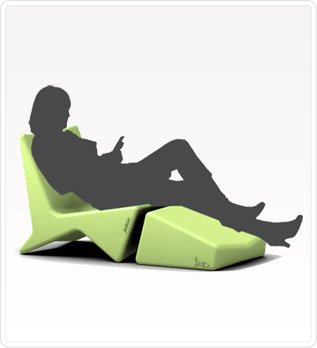
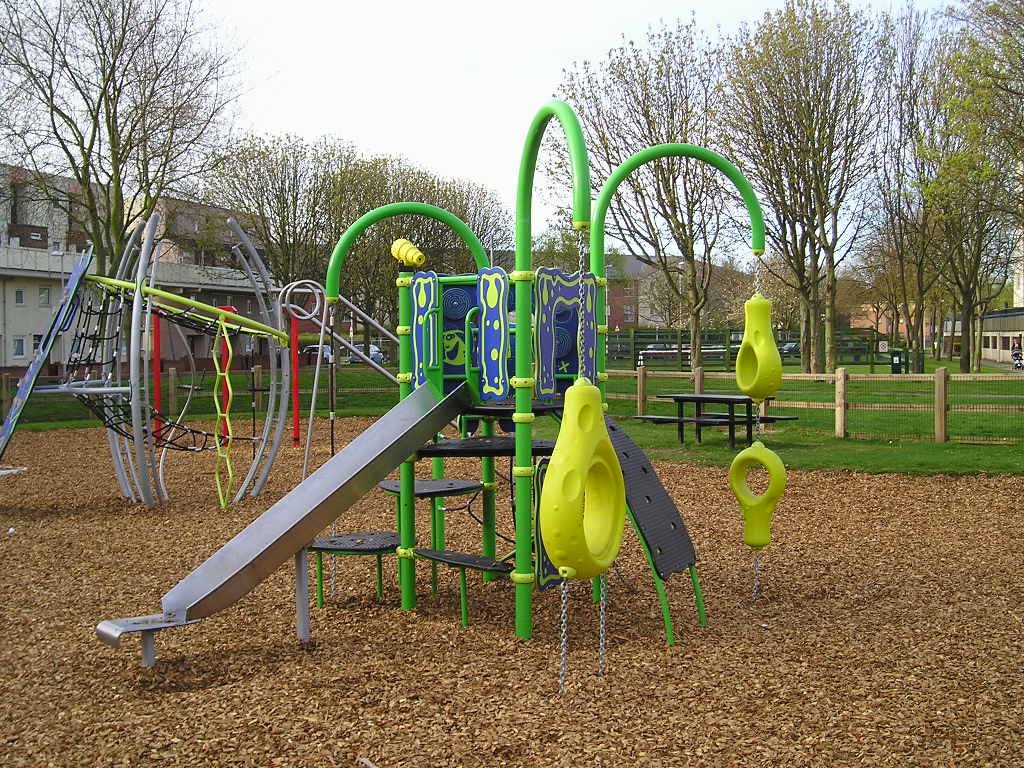
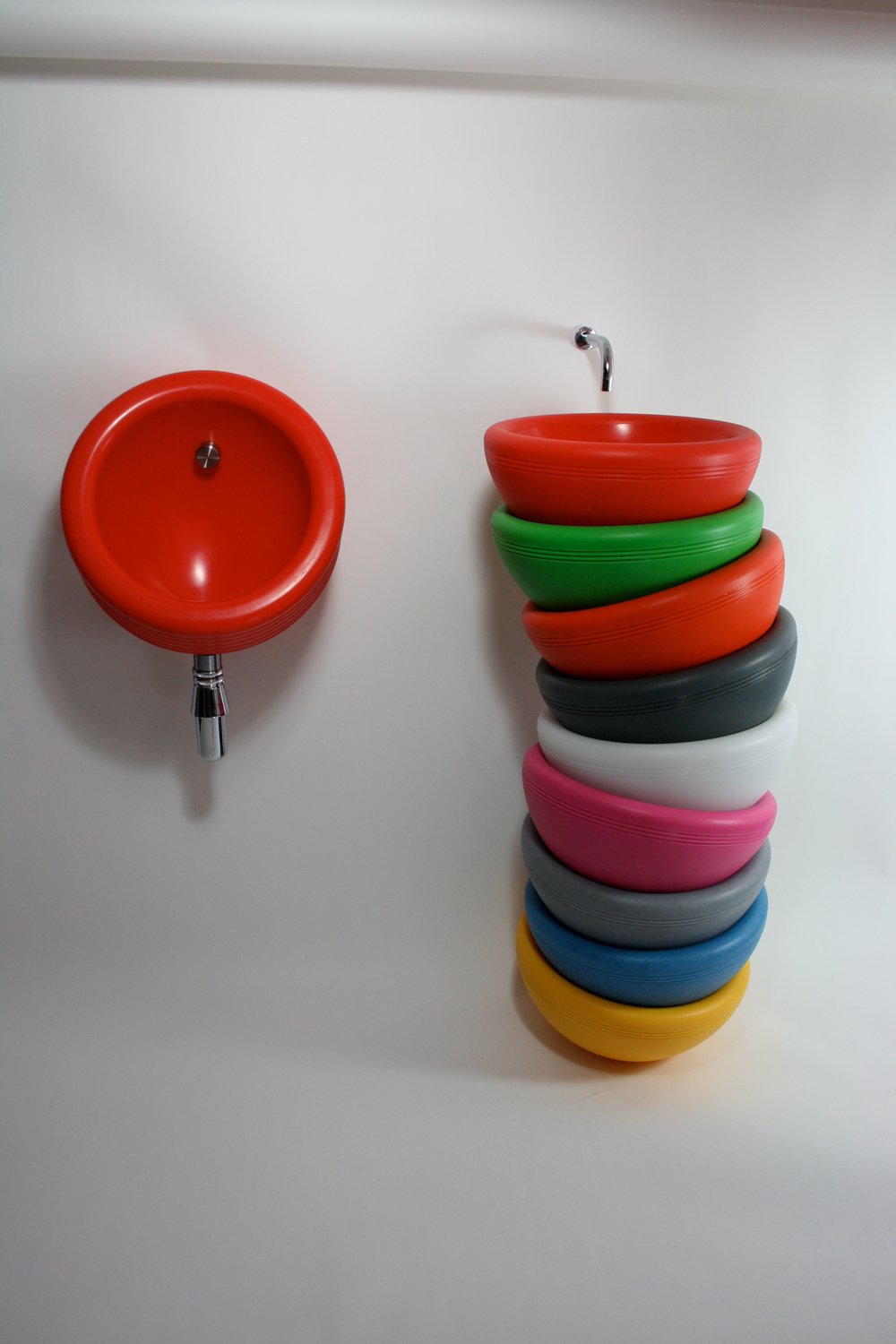
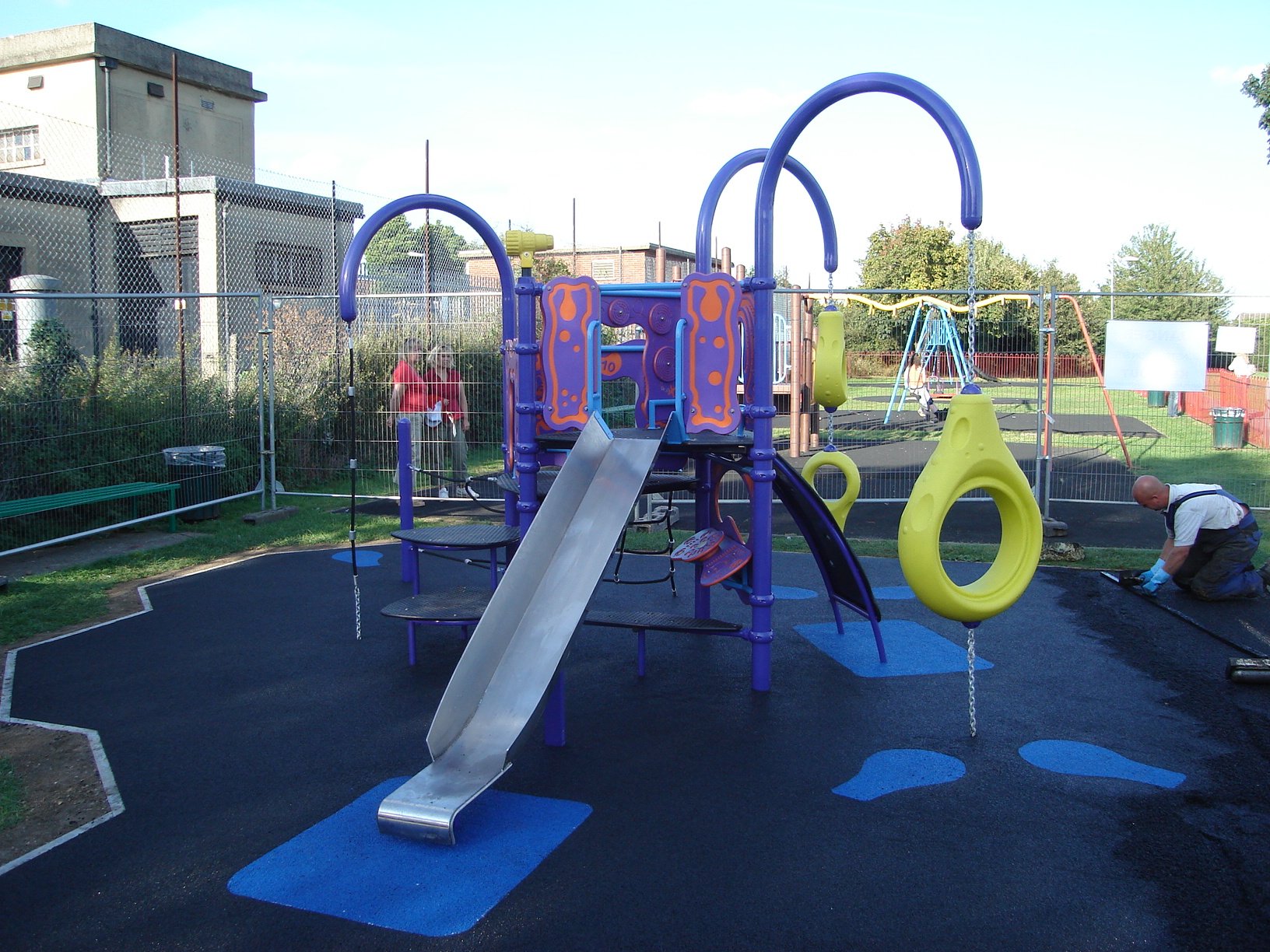
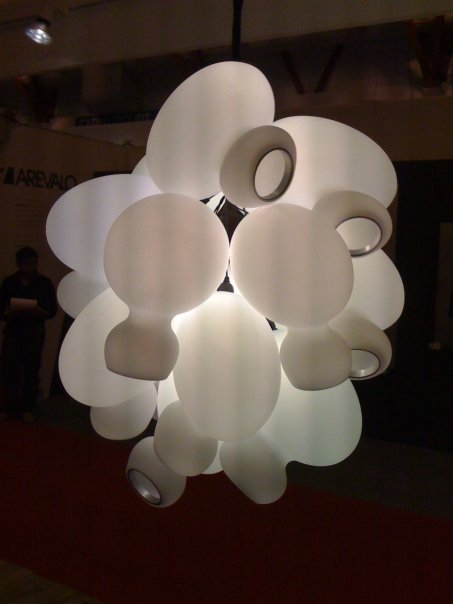
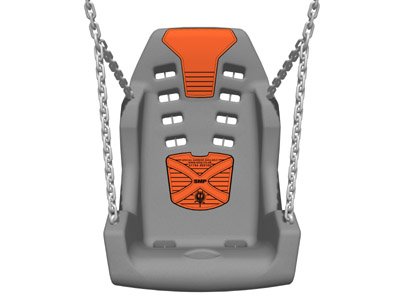
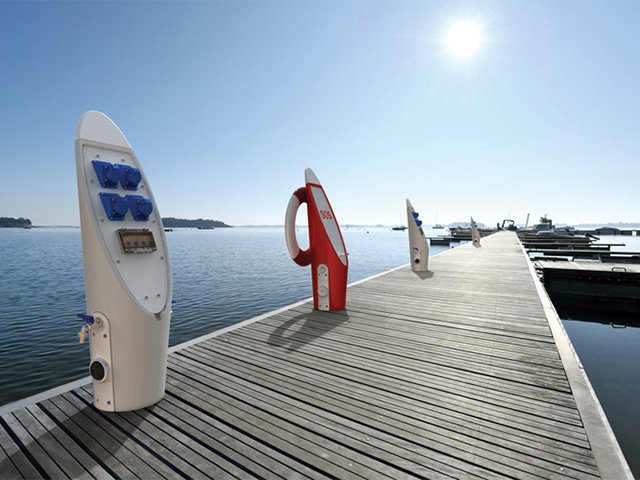

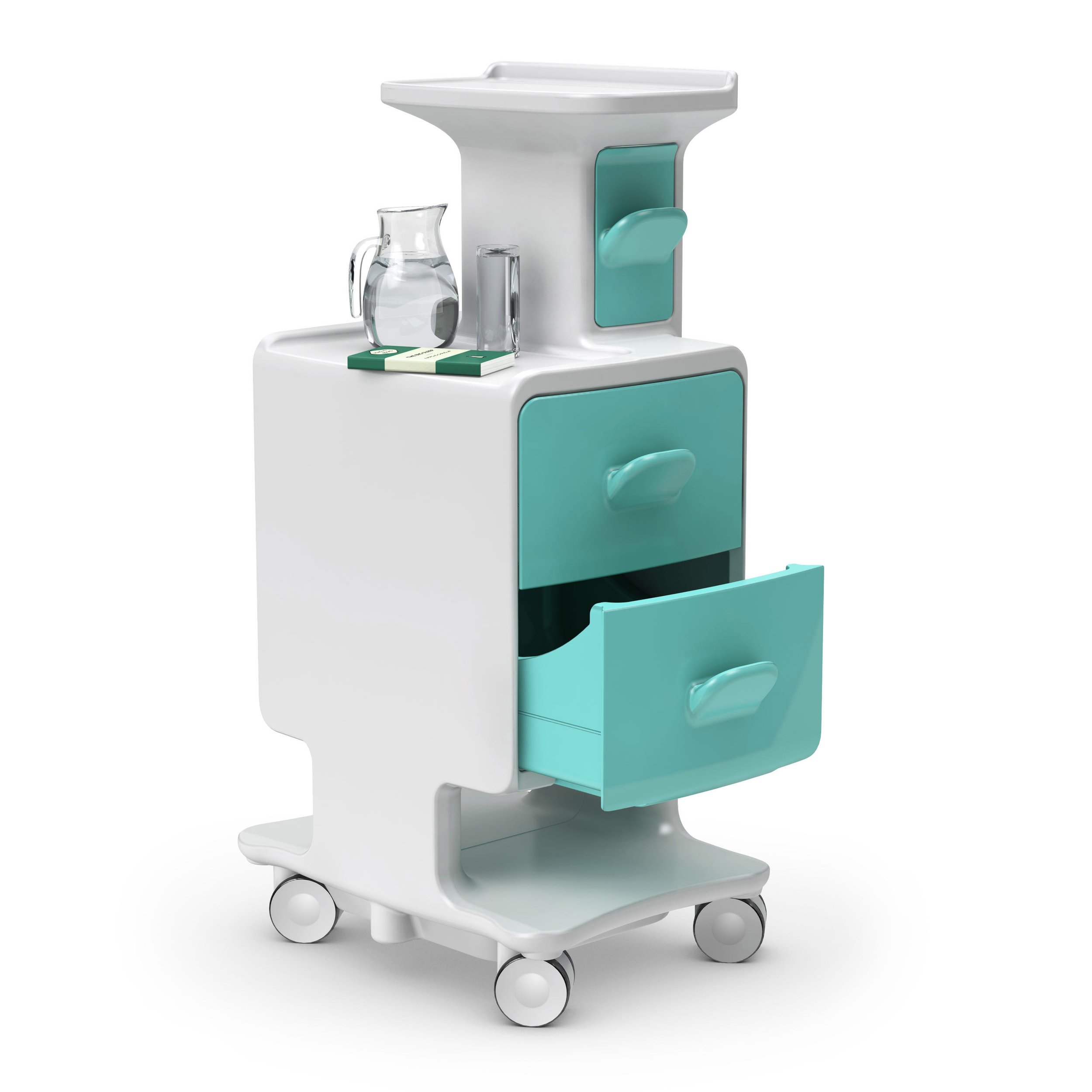
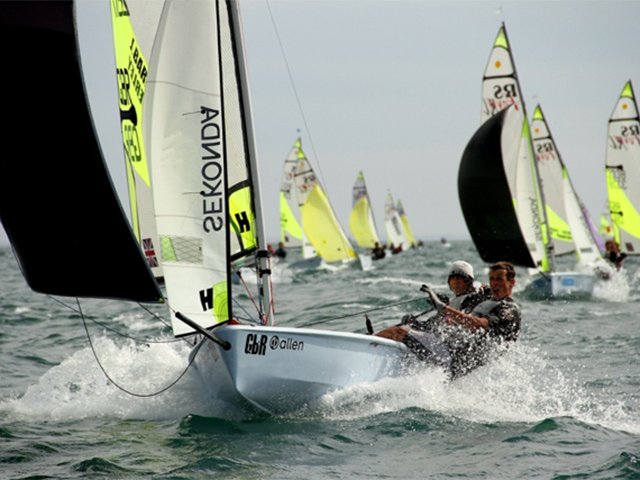
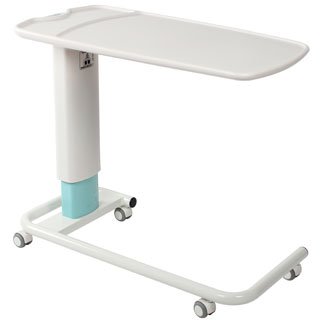
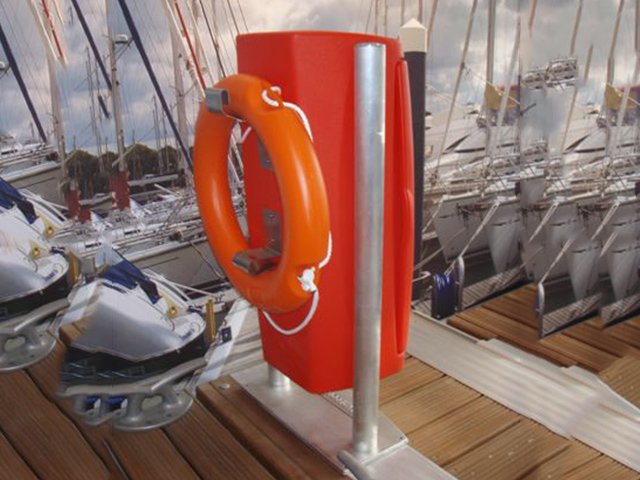
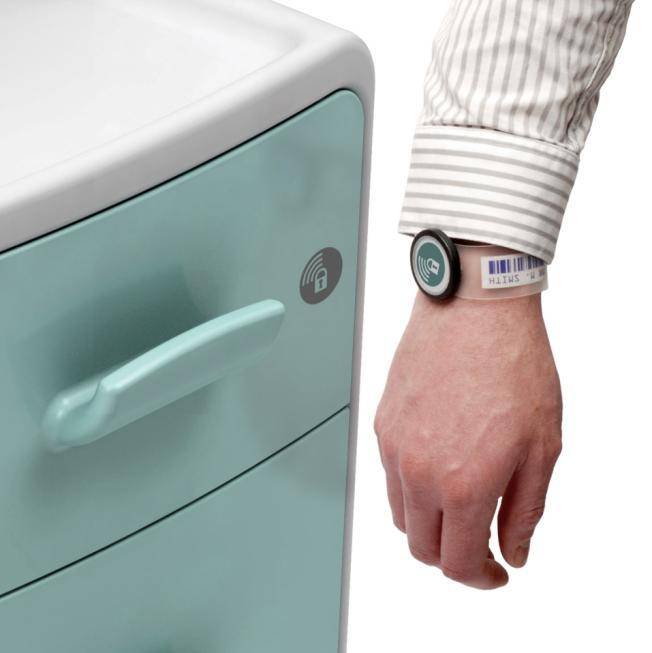
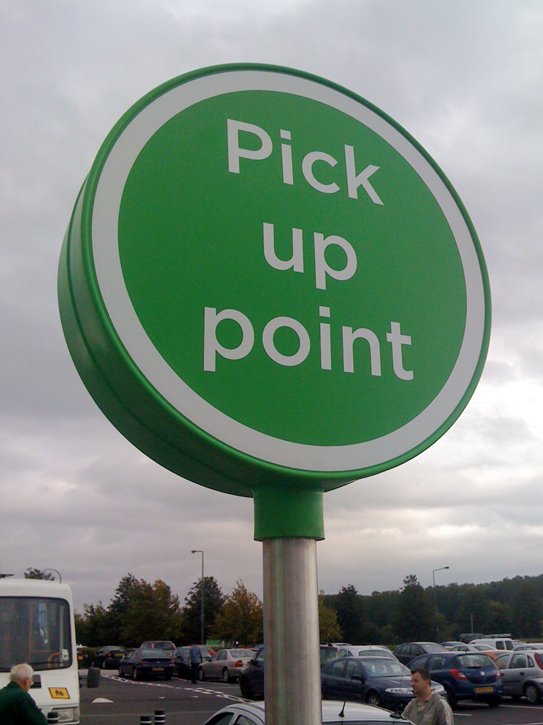
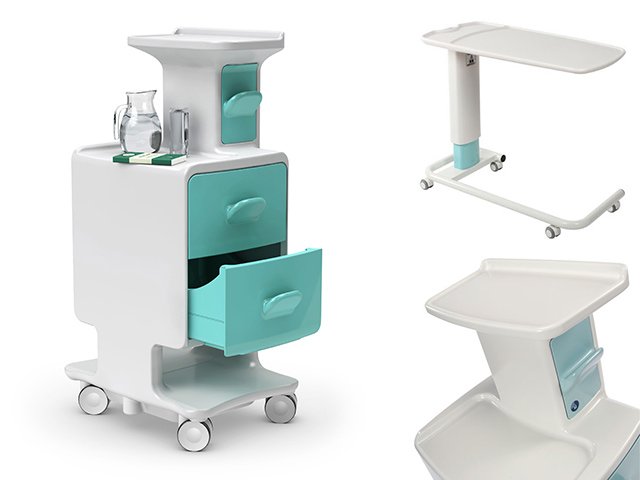
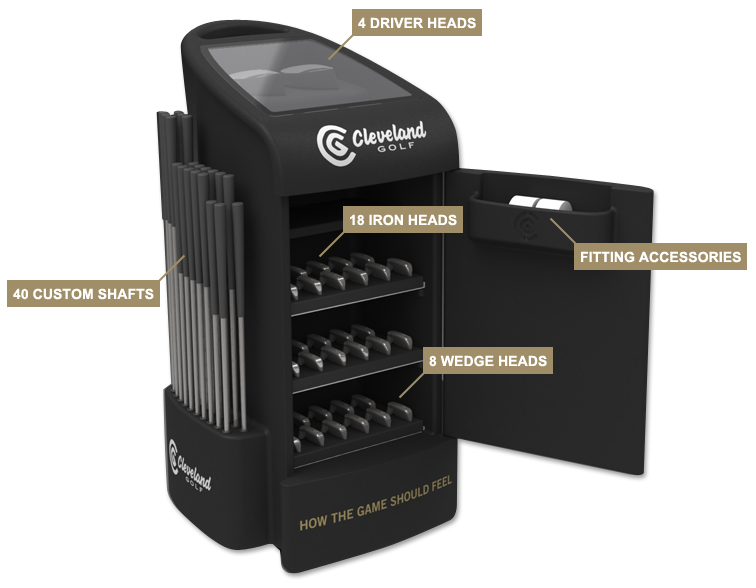
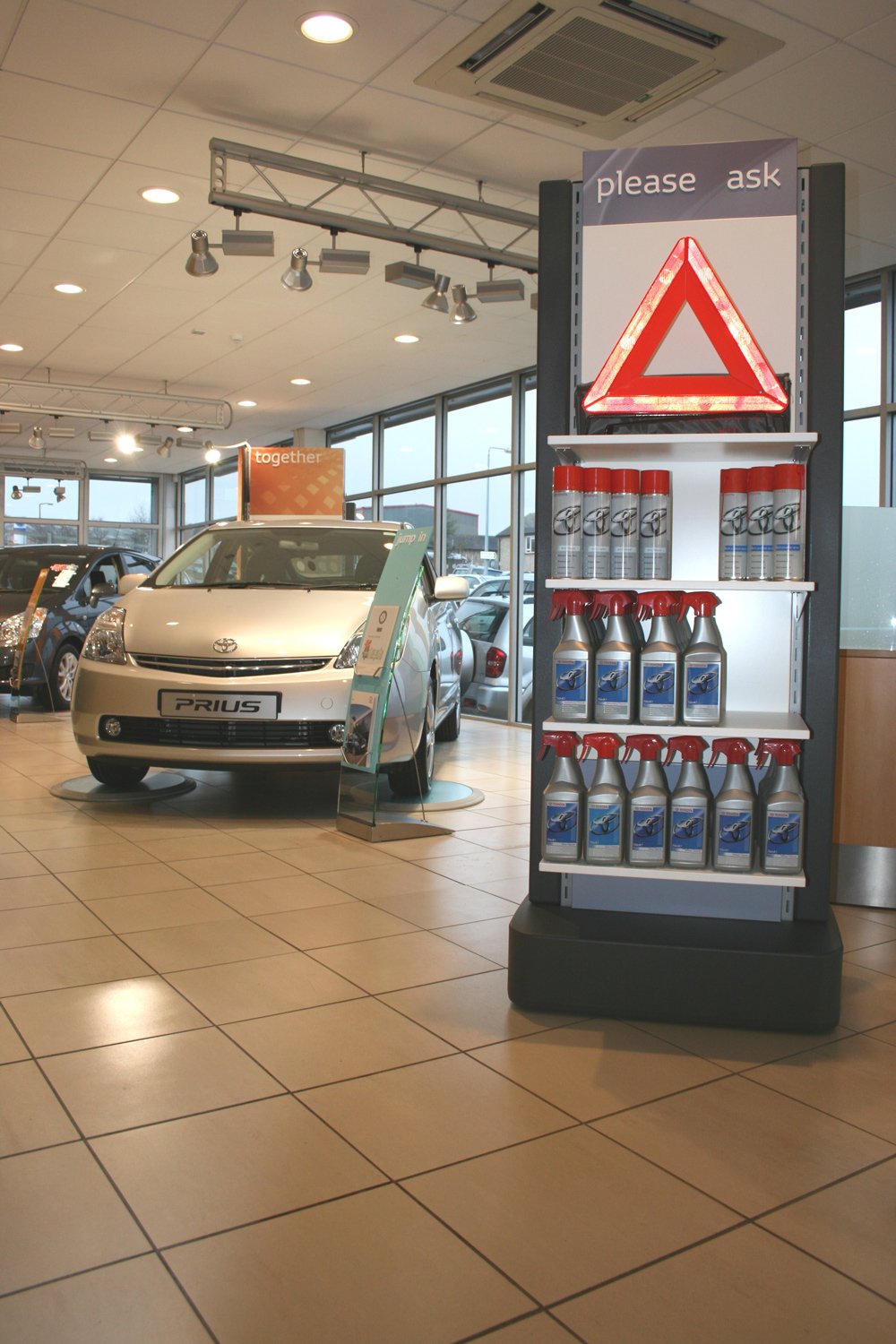
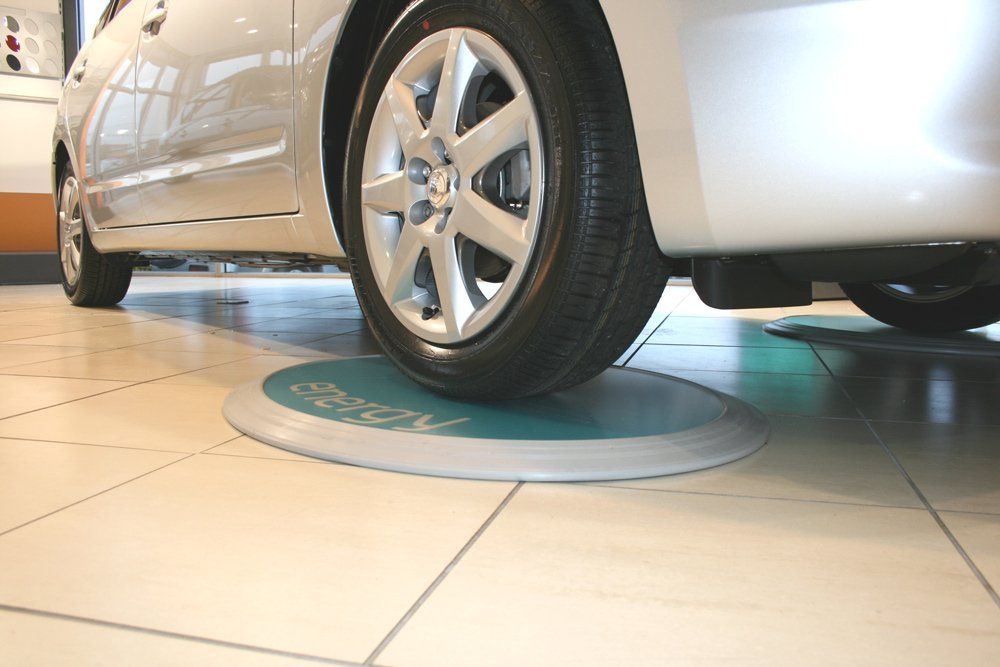
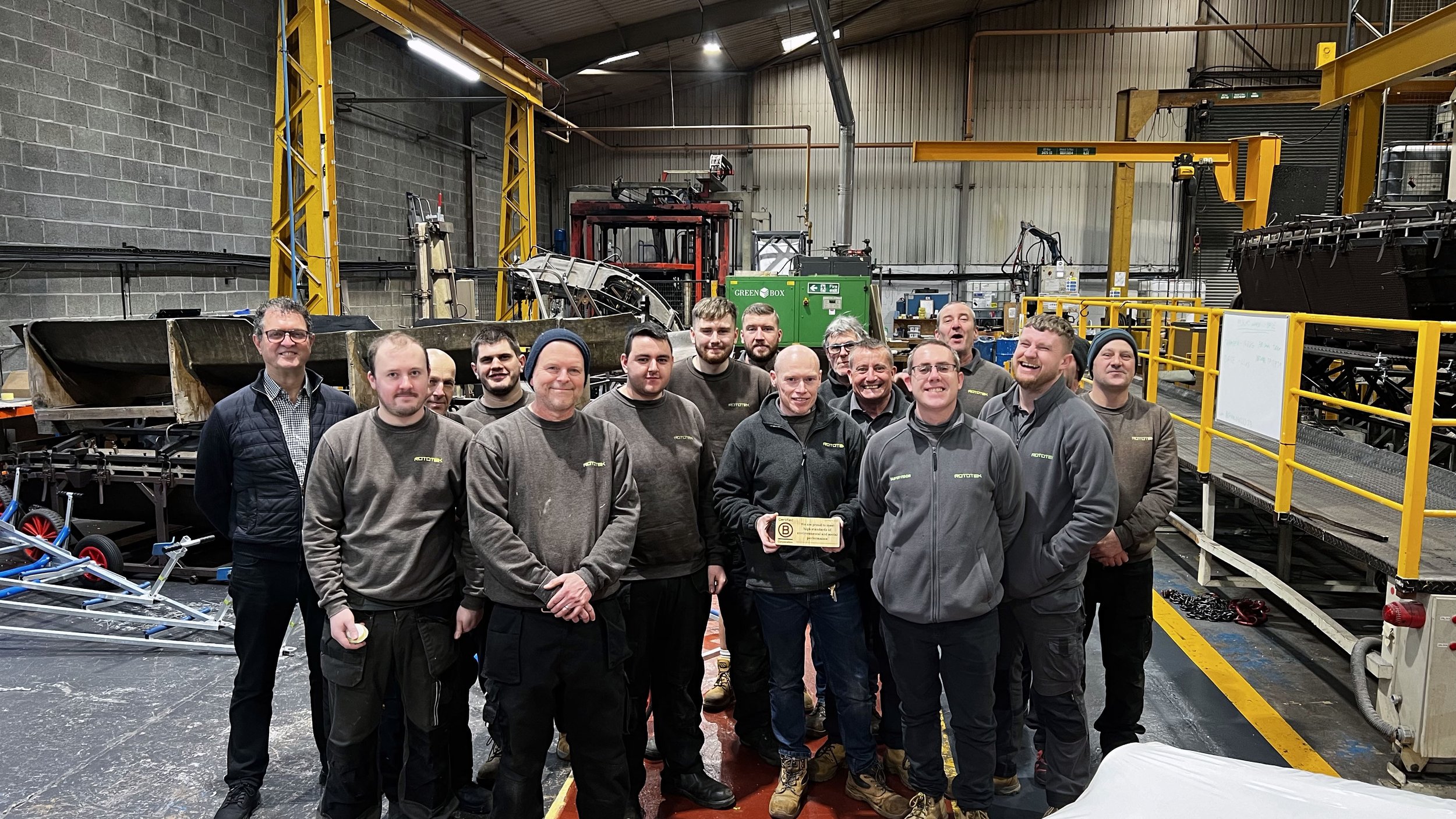
Why Choose Rototek for Custom Moulding?
Rototek brings over 30 years of experience in technical rotational moulding, combining a deep understanding of the industry with the technical skills required to produce the custom plastic moulding to fulfil your needs. Our 30-year presence in the market is a testament to our ability to adapt and thrive in this ever-evolving industry, making us a reliable partner for your manufacturing needs.
Our comprehensive, end-to-end service makes us stand out from other manufacturers, with our friendly and knowledgeable team on hand to guide clients through the process. Our brilliant team are the reason we have such
high customer retention rates and positive feedback on their customer service. Our team is dedicated to shaping the future of manufacturing, transforming your concepts into tangible products. We pride ourselves on having the right team to solve the issues that may occur, and we are there not only as your supplier but as your moulding partner, giving you the first-class service that you need.
With Rototek, you're not just choosing a service. You're partnering with a leader in innovative and sustainable manufacturing solutions.