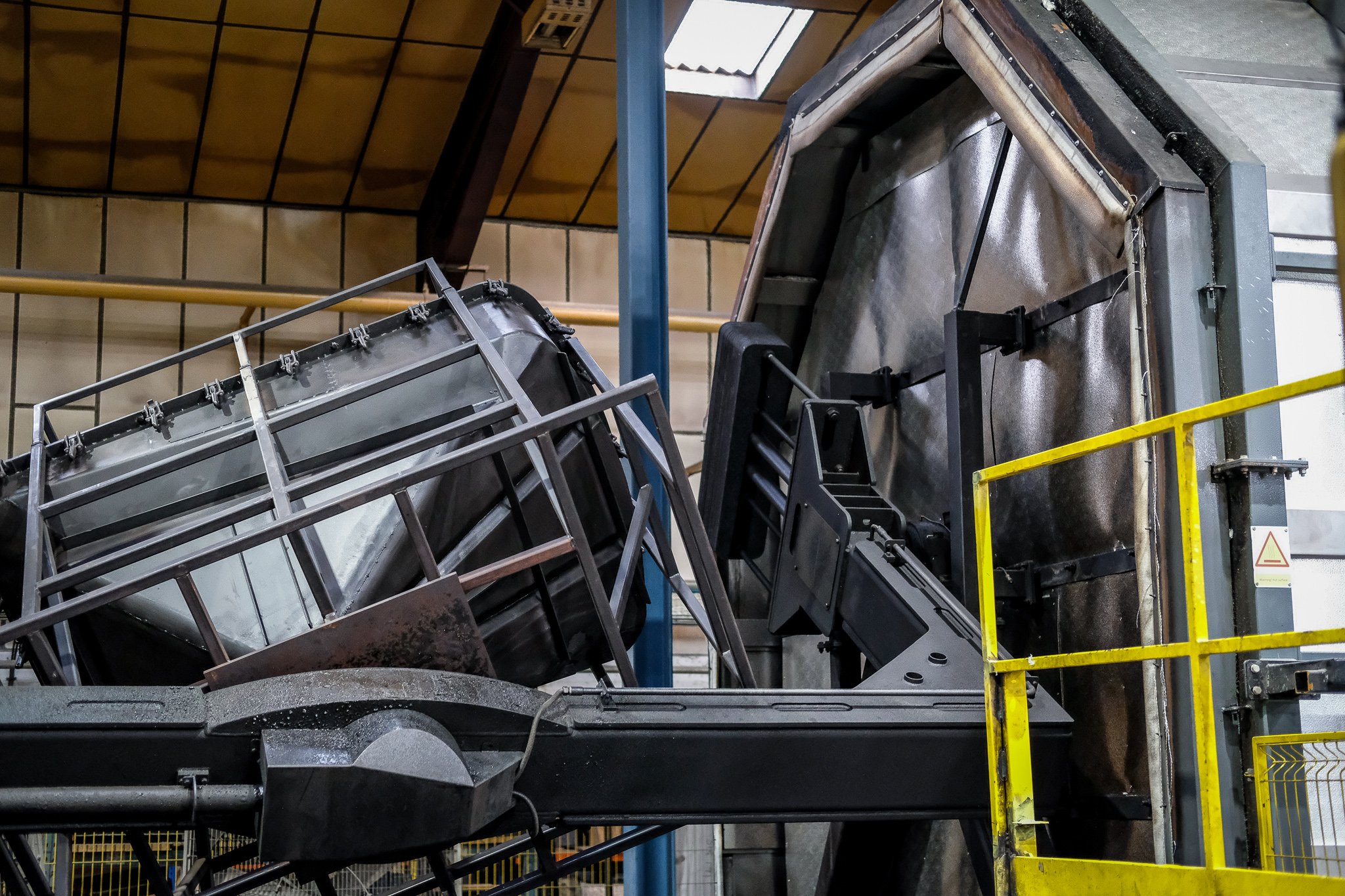
Our
Service
At Rototek, our expertise lies in custom moulding.
Our team are dedicated to shaping the future of manufacturing, transforming your concepts into tangible products, ranging from a compact 1-litre liquid container to an impressive 7-metre moulding.
With over 20 machines across our 2 sites ranging from rock & roll and bi-axial carousel to electrically heated tooling, we are working 24 hours a day, 5 days a week to bring your idea to life.
We pride ourselves on having a right team to solve the issues that may occur, and we understand that they will occur from the design stage right through the production and quality finishing, our sales team are always responsive, and we are there not only as your supplier but as your moulding partner giving you the first-class service that you need.
Rotomoulding offers relatively low tooling costs, from economical short runs to thousands of products, as well as the ability to cope with large mouldings. Rotomoudling is ideally suited to new product development and prototype work, as this can be carried out without vast expense.
With Rototek, you're not just choosing a service; you're partnering with a leader in innovative and sustainable manufacturing solutions.
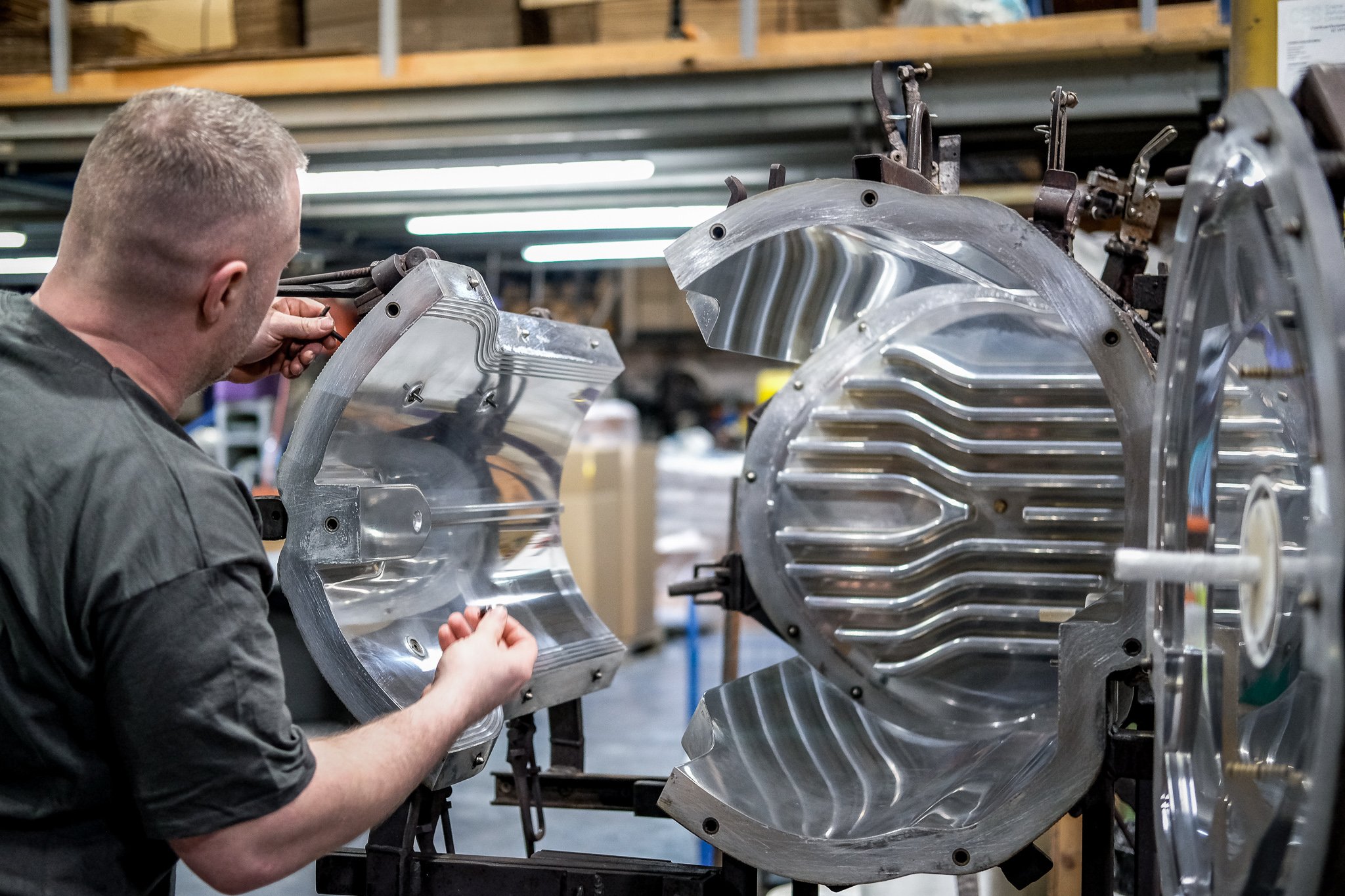
Rotomoulding
Services
-
Rototek can work with you at concept stage to prove design ideas, input data on new materials and develop new processes. Our inhouse design team can either fully create your concept, or work alongside your designers.
-
Once designs are finalised, we can supervise the toolmaking process ensuring the final moulds meet specification.
Our competitive edge lies in our advanced tooling design, programming expertise, and commitment to reducing waste and weight in our products.
-
Across our 2 sites, we have over 150,000 square feet of production space and over 20 machines to manufacture your products.
We ensure quality control throughout the production process, from the materials to the final product, employing environmentally sustainable production methods and procurement practices, all supported by our ISO 9001 and B Corp accreditations.
In 2023 over 99.7% of our factory-made products fulfilled our customer expectations, well above the industry standard.
-
We offer an assembly, inspection, packaging and despatch service. Our specialist finishing team will ensure your products are finished to your specification with any additional parts fitting to part or fully complete your products.
We can also ship products worldwide direct to your customer and offer a wide range of shipment options to suit your requirements.
-
Rototek’s custom plastic moulding solution focuses on designing a unique mould based on specific client requirements, turning the client’s idea into a product suitable for the rotational moulding process.
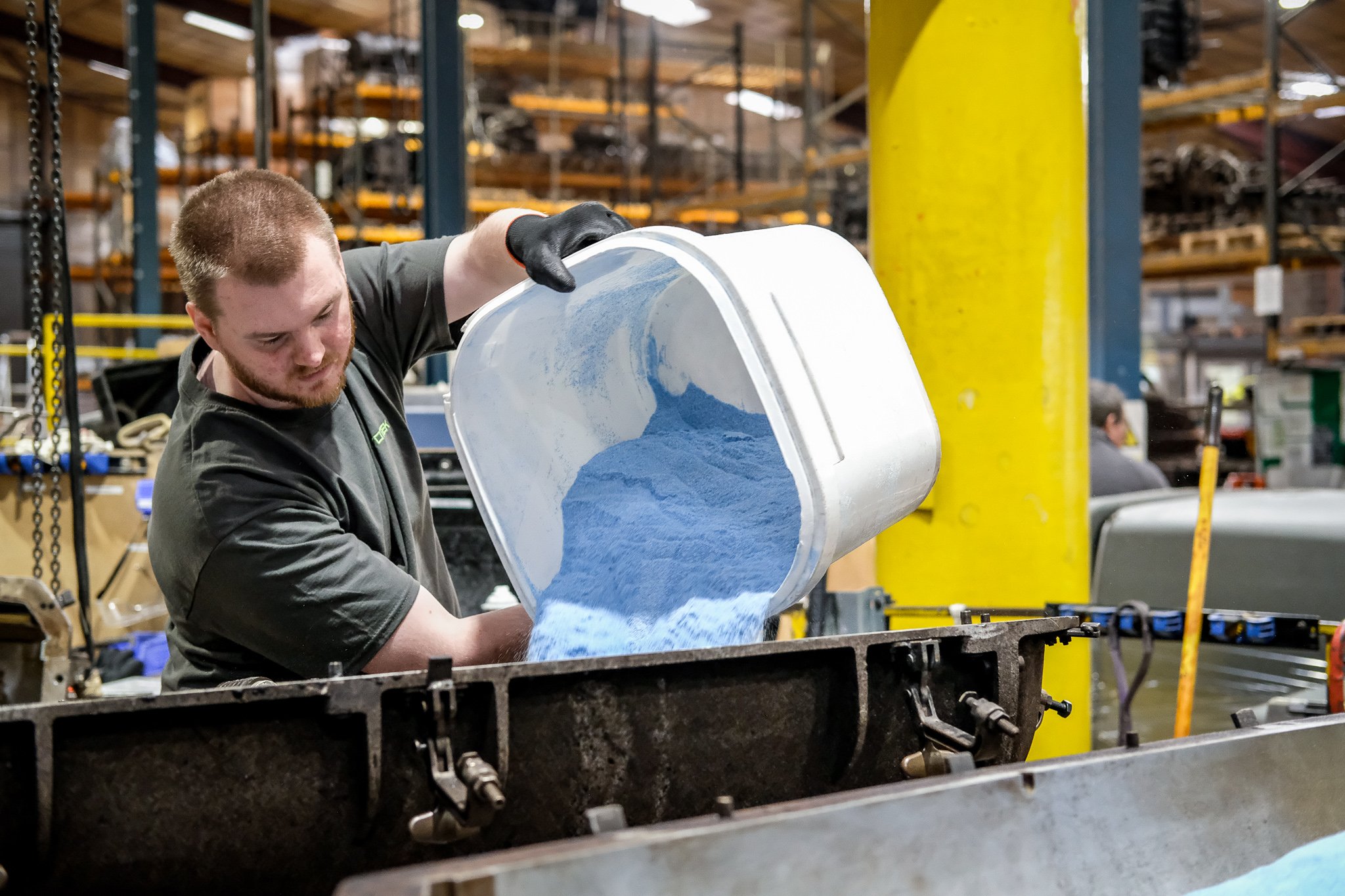
In 2023 over 99.7% of our factory-made products fulfilled our customer expectations, well above the industry standard.
We ensure quality control throughout the production process, from the materials to the final product, employing environmentally sustainable production methods and procurement practices, all supported by our ISO 9001 and B Corp accreditations.
-
1. Loading →
–
The metal mould is filled with a predetermined quantity of polymer powder, closed, clamped and then passed into an oven chamber. -
2. Heating →
–
The mould is heated externally to a high temperature and rotated around both vertical and horizontal axis. As the powder inside heats up, it begins to melt and adhere to the inner surface of the mould. This continues until an even layer of molten plastic is formed over the surface of the mould. -
3. Cooling →
–
In the cooling chamber air is directed at the mould and in some cases water jets are used. When the plastic inside the mould has become solid, the mould can be removed from the chamber. -
4. Unloading
–
The plastic component is then removed from the mould and allowed to finish the cooling process unrestricted by the mould.Cycle time can vary from 20 minutes to one hour. The plastic is formed without pressure and as a result has no moulded in stresses.
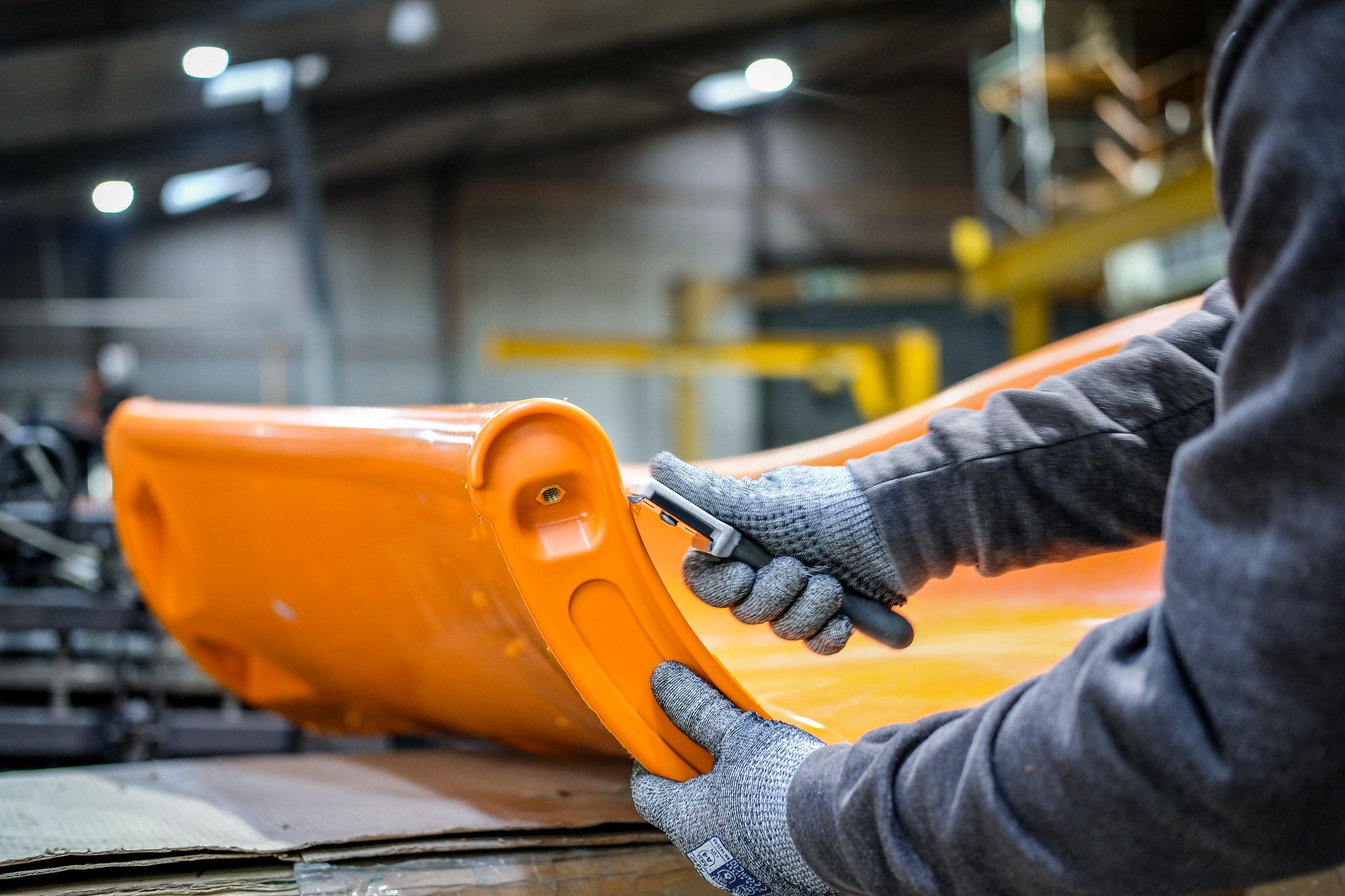
Product Examples
Have a scroll through our product examples which showcase Rototek’s manufacturing capabilities, from smaller furniture to 7m sailing dinghies we have the capacity to create it all.
These examples illustrate our versatility in delivering products of various shapes, sizes, and functions, all tailored to meet our customers' unique needs. Every item is a testament to the precision and innovation that define our state-of-the-art manufacturing facilities.
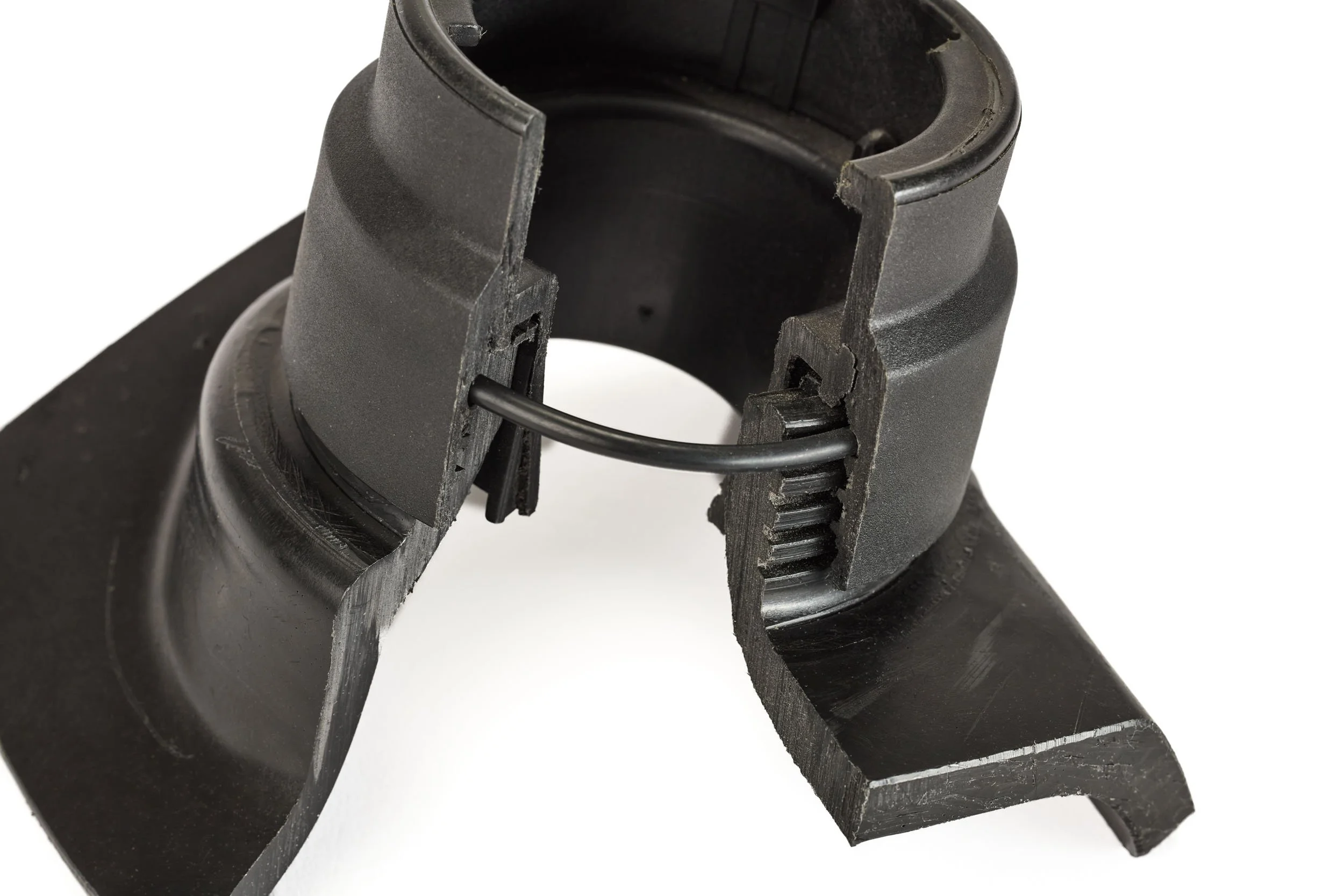
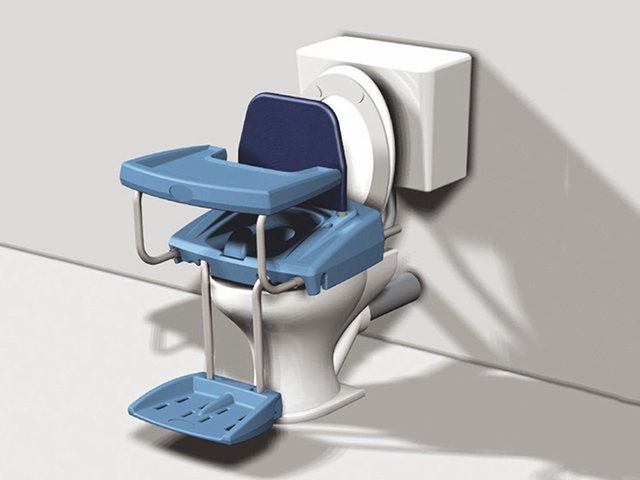
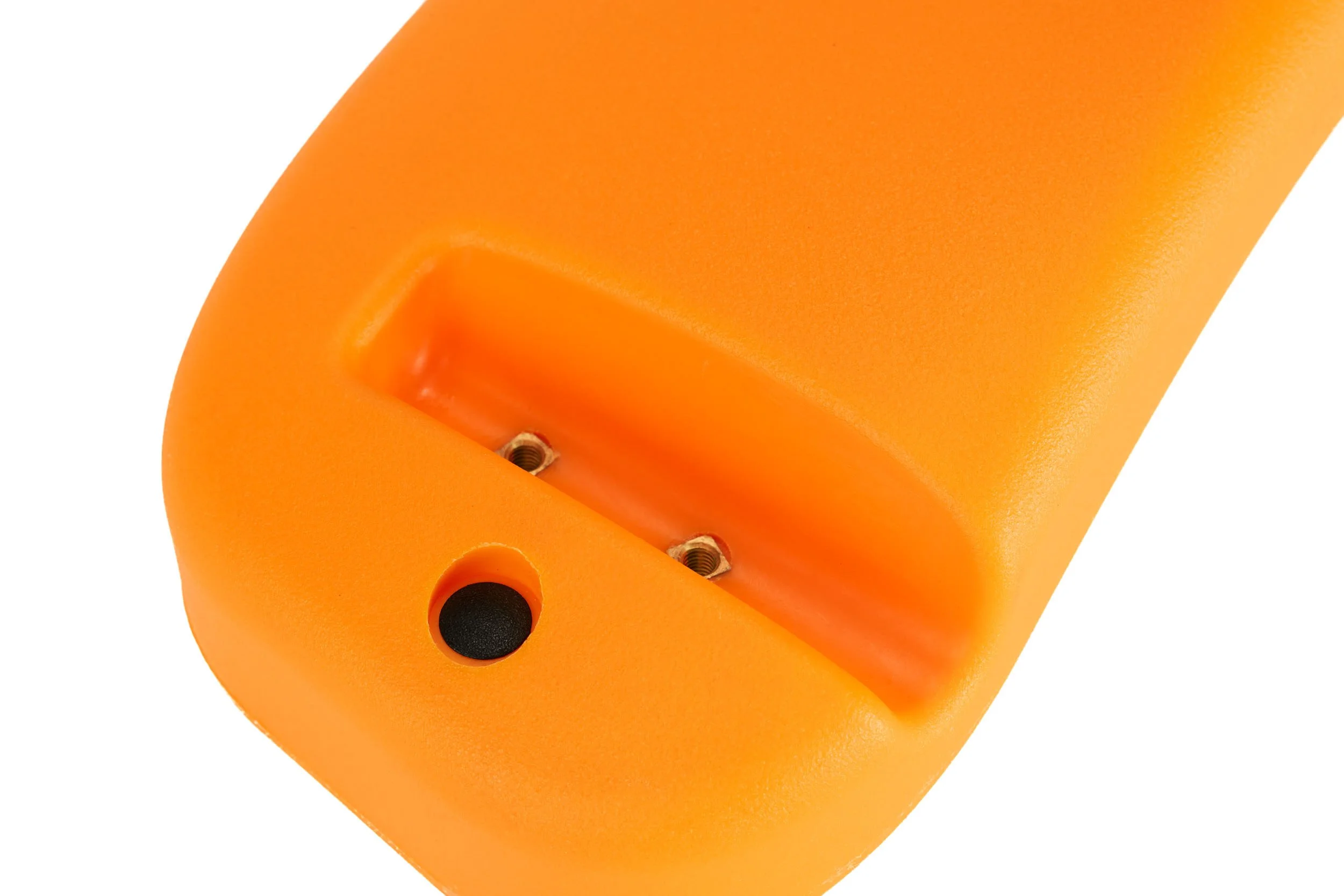
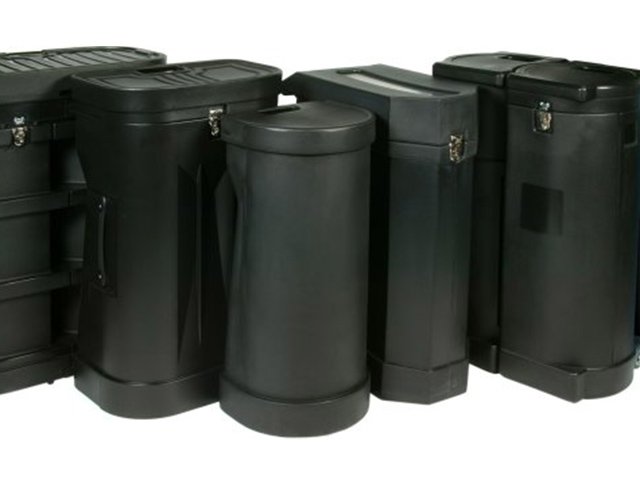
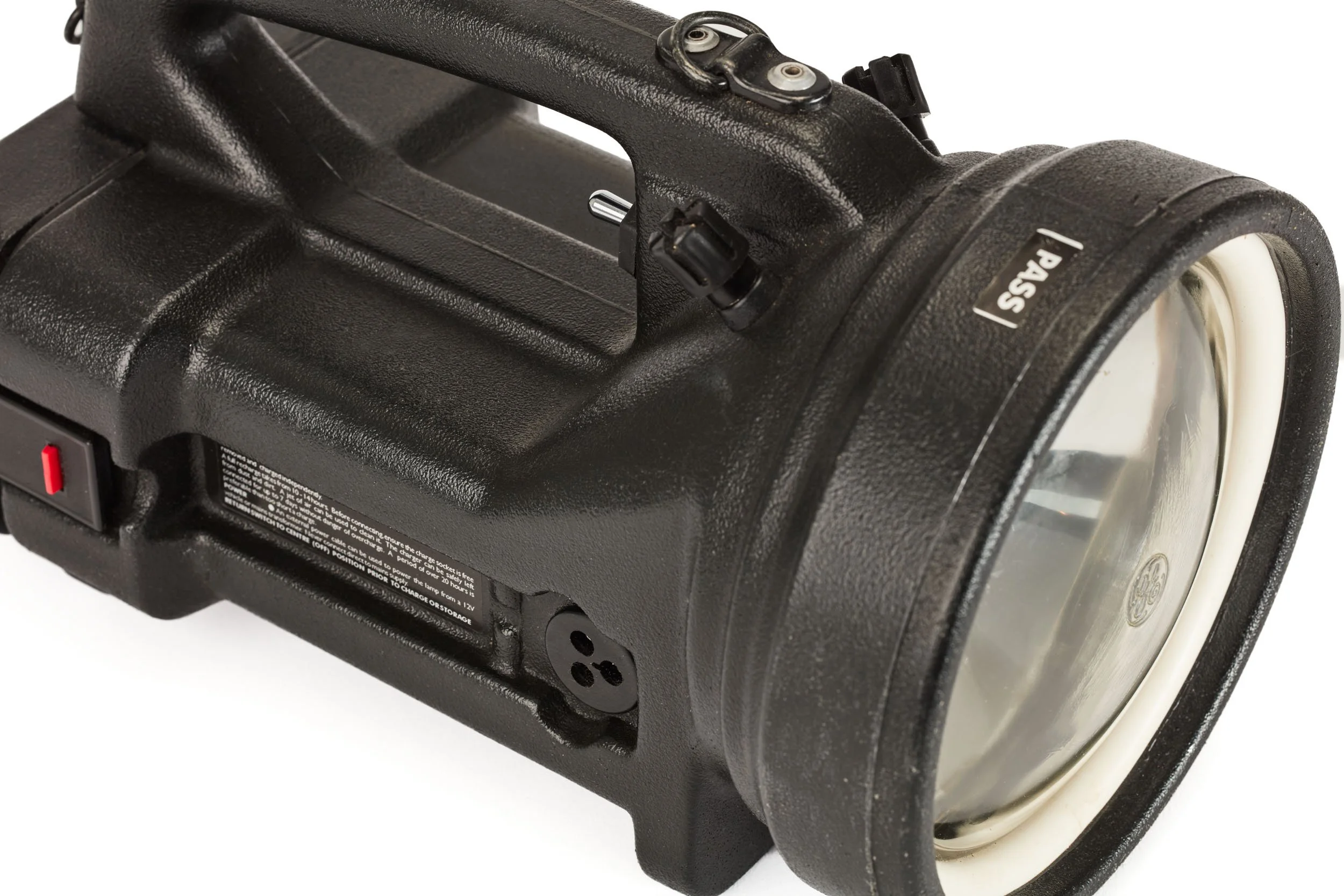
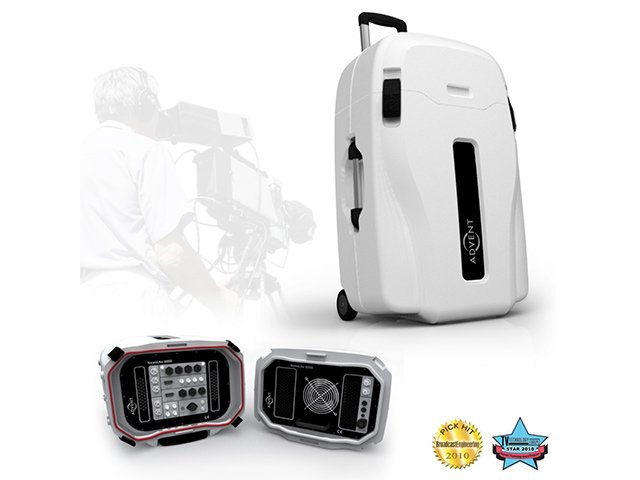
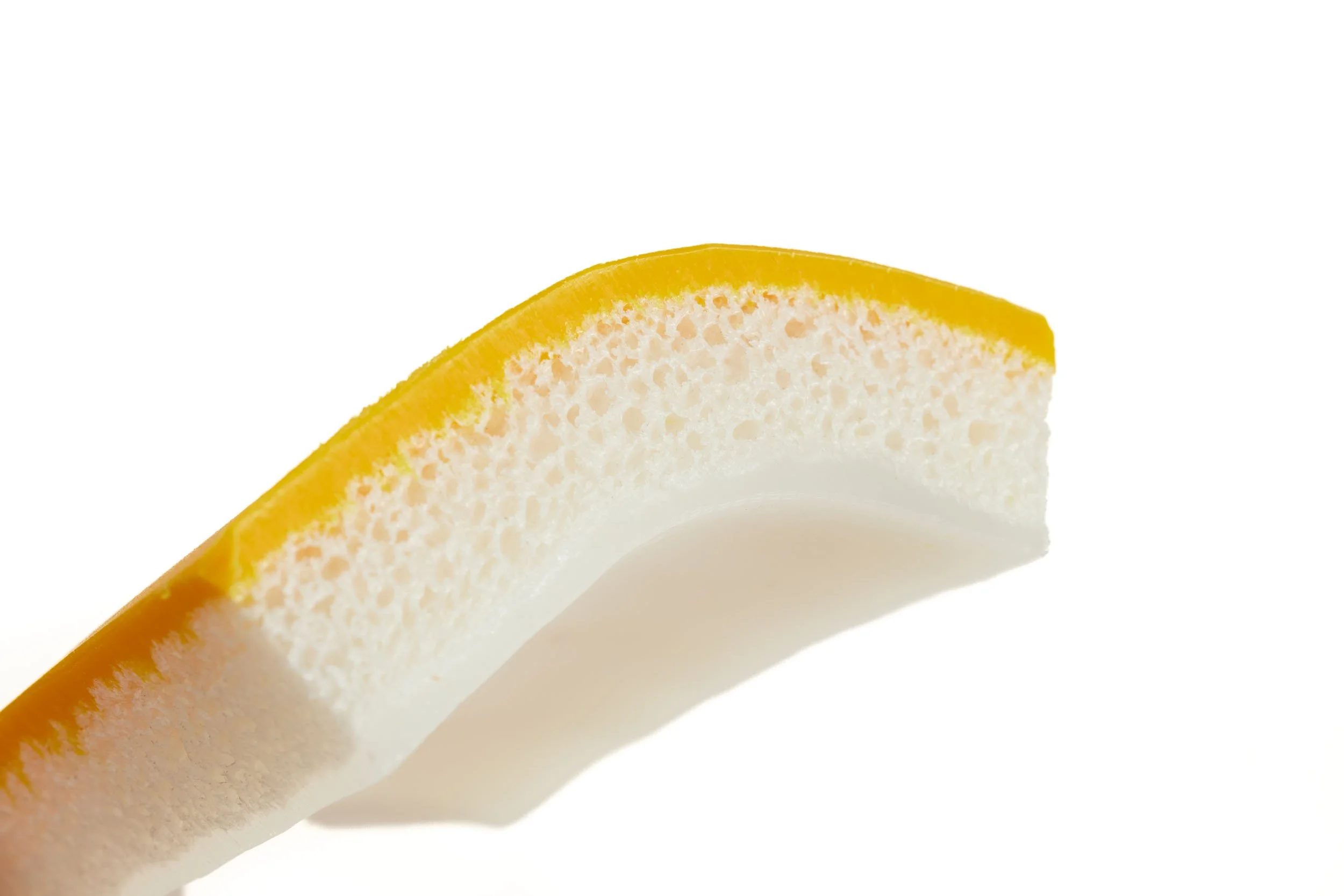
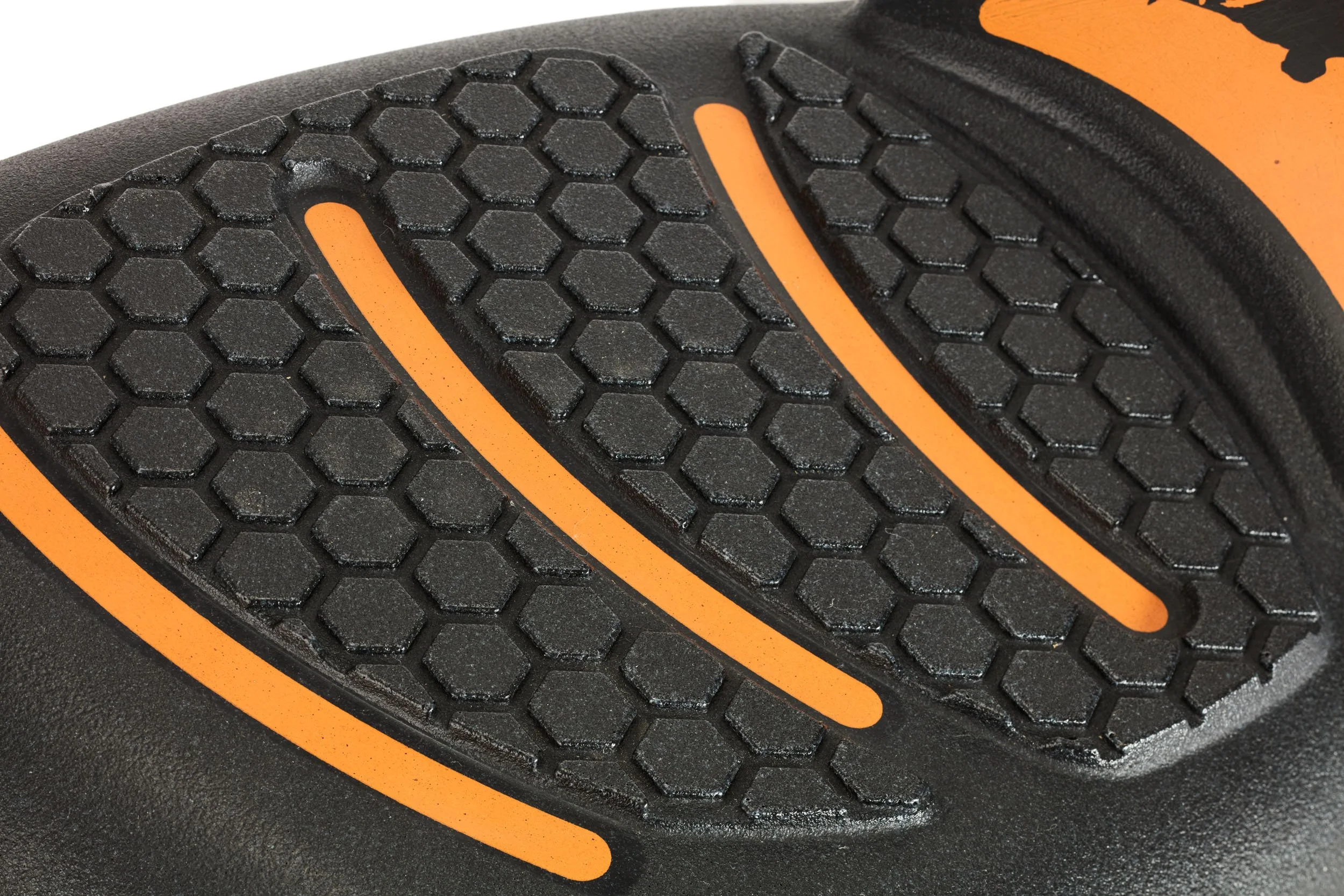
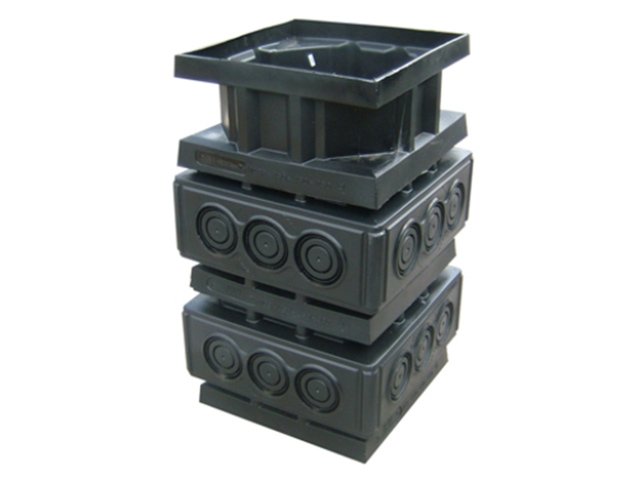
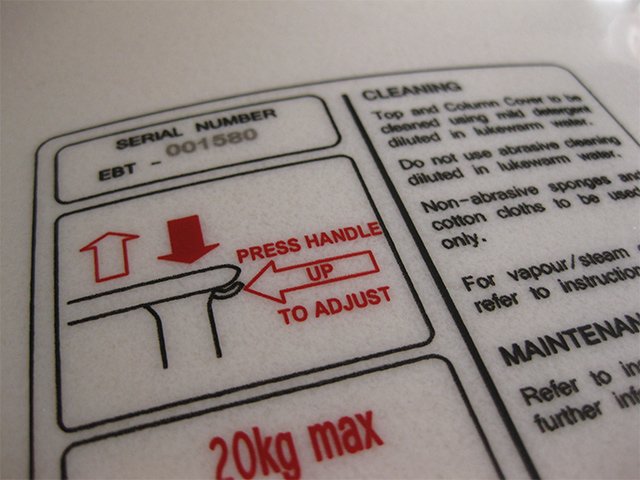
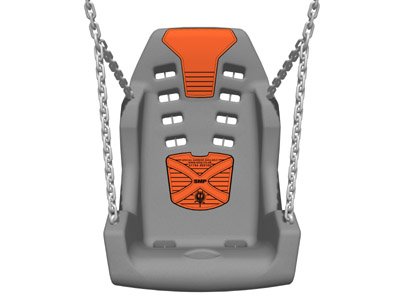
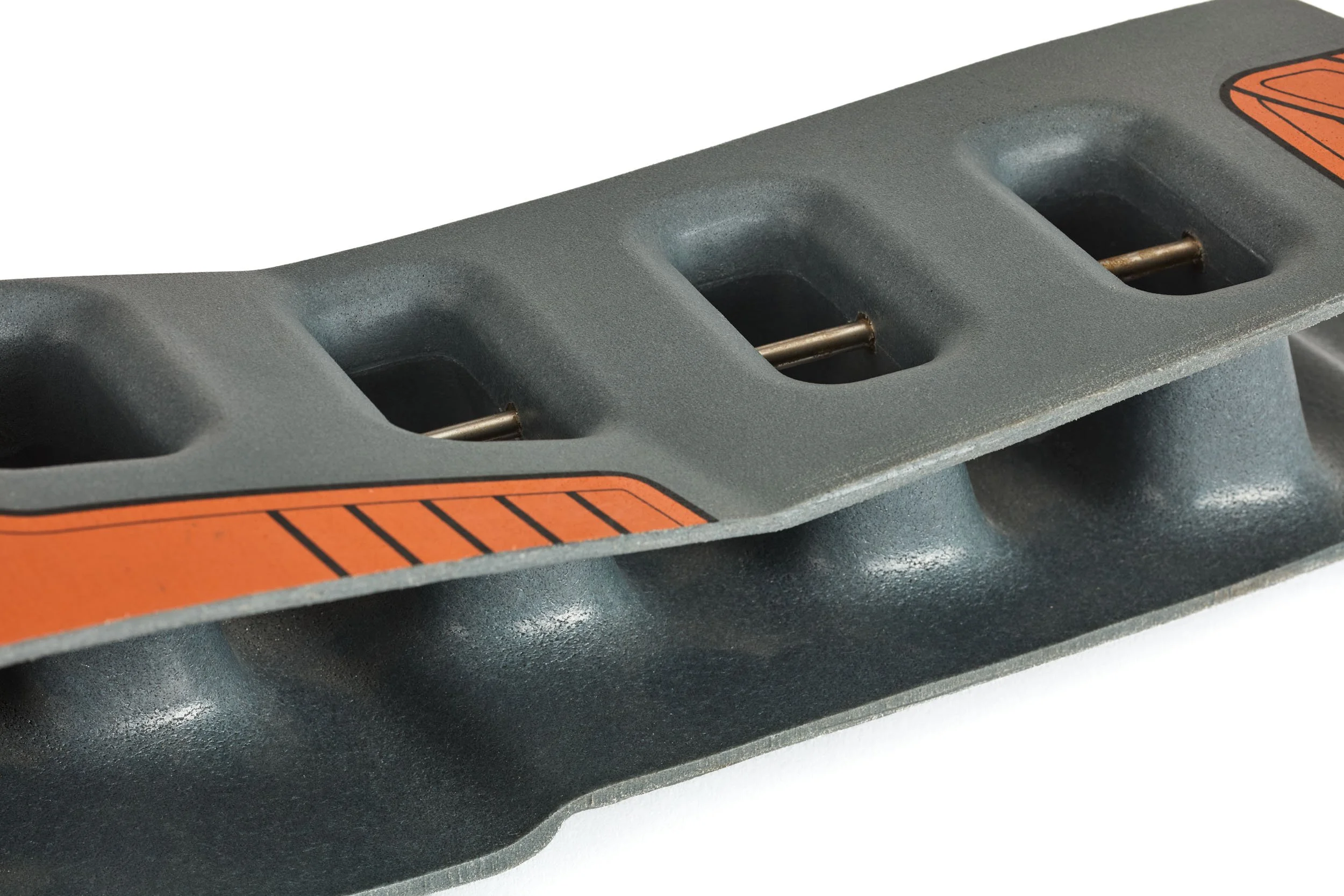
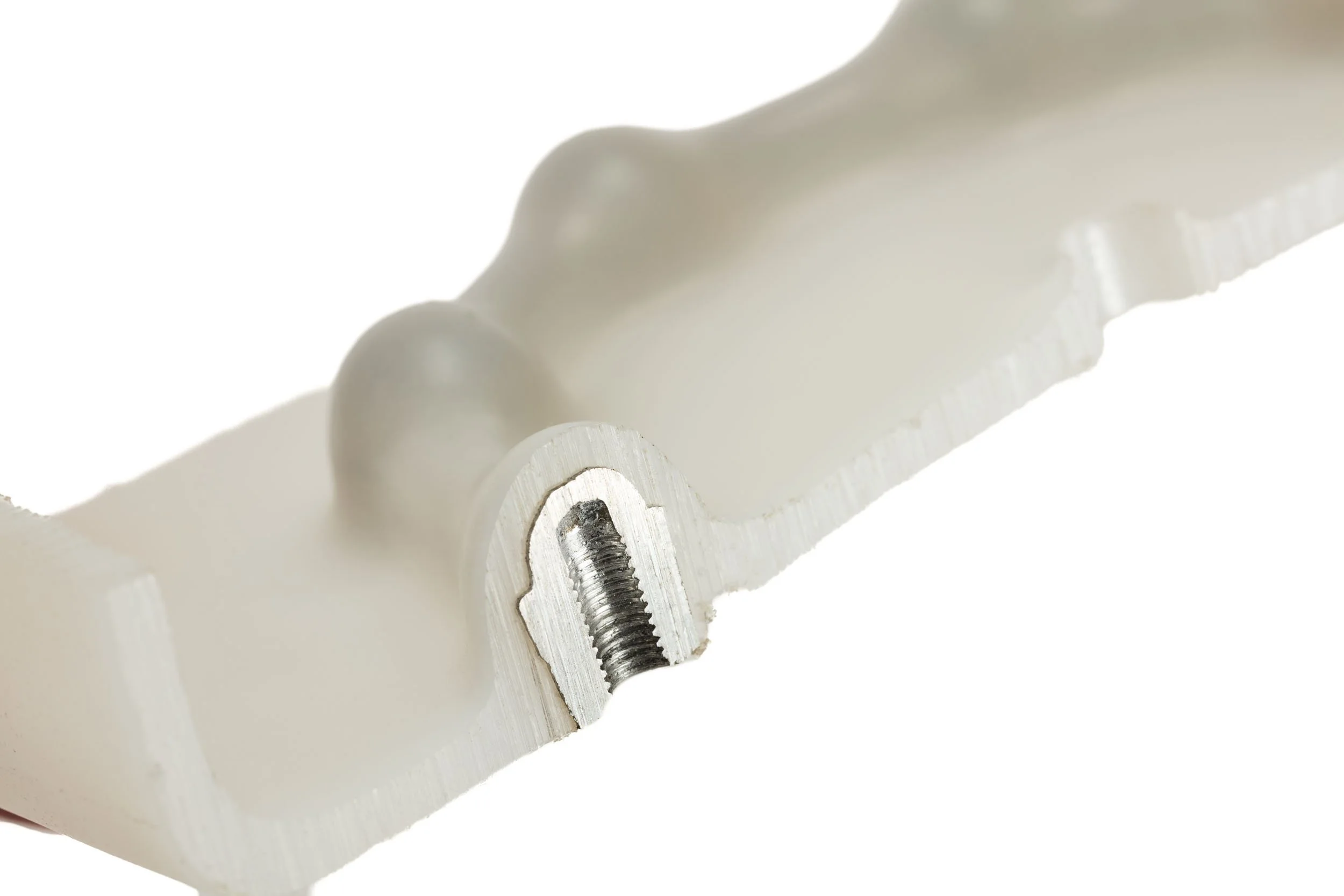
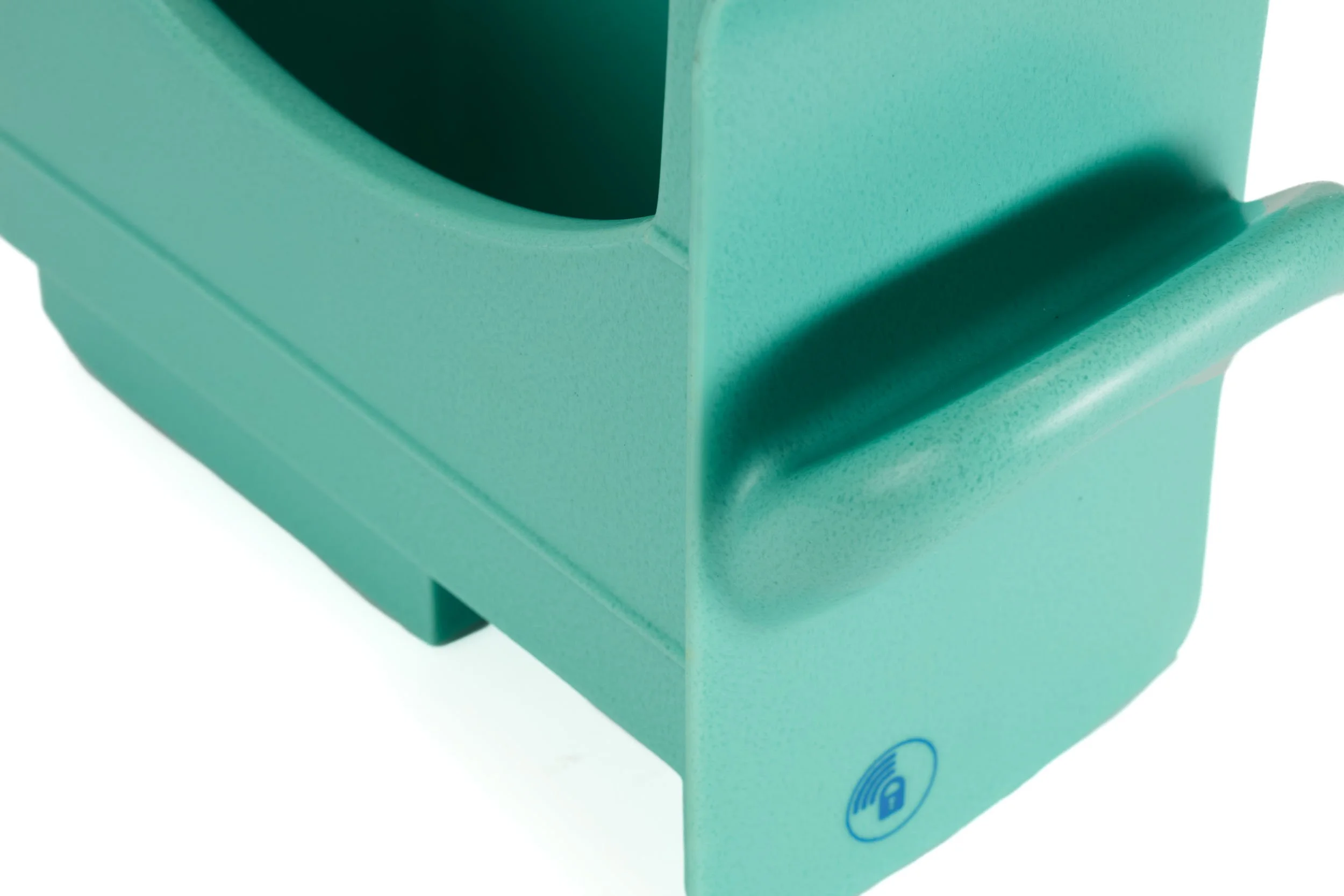

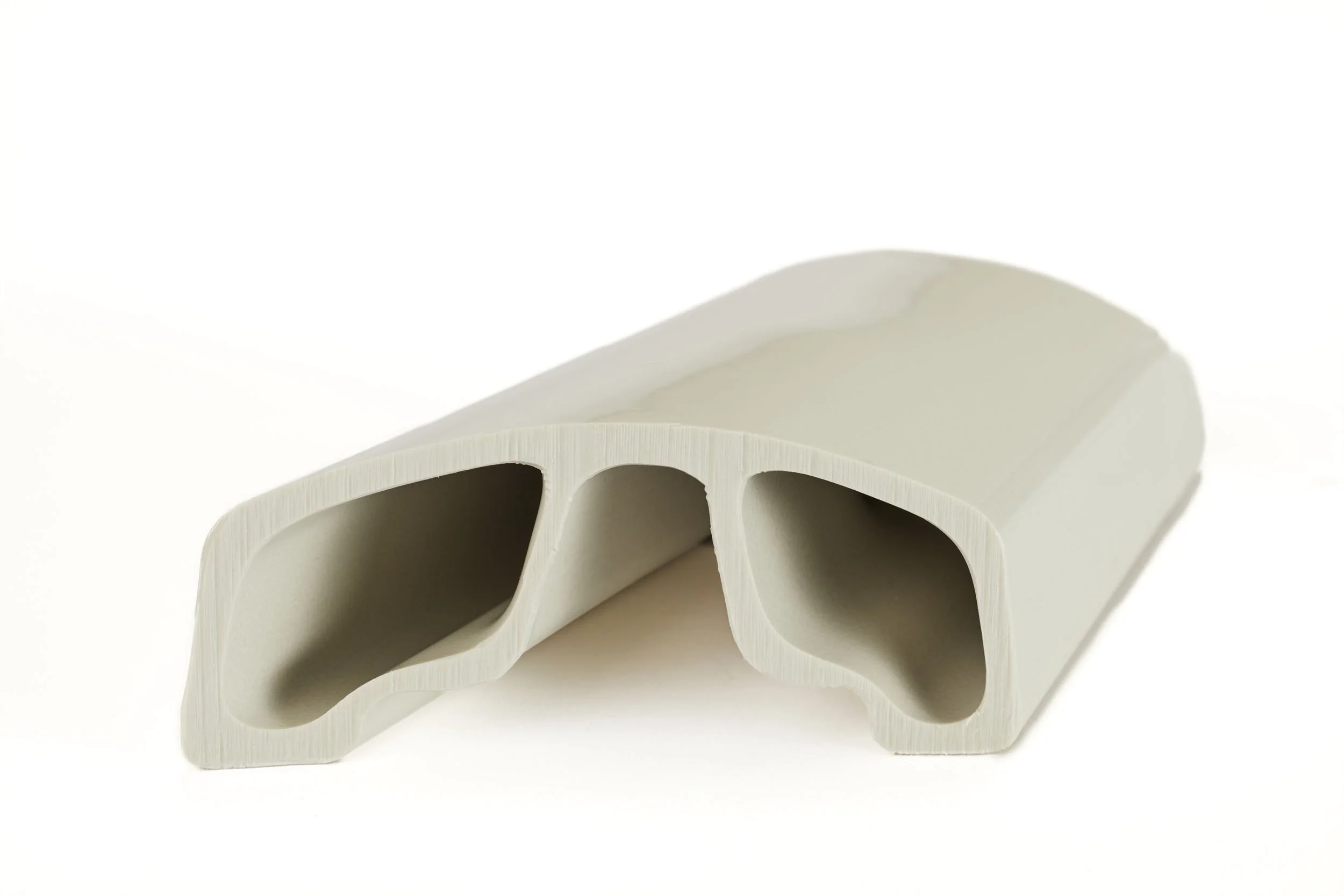
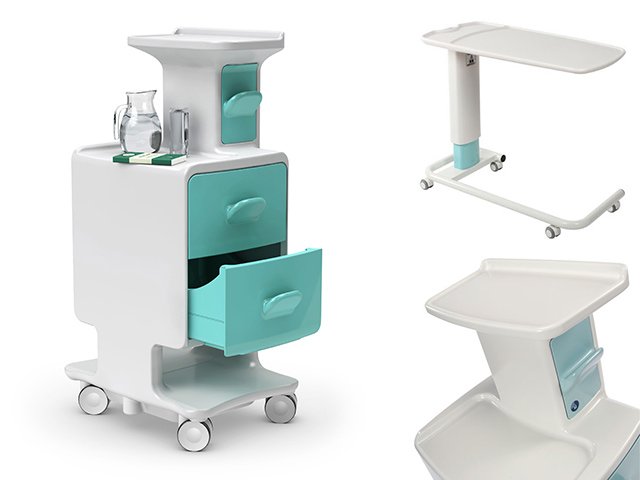
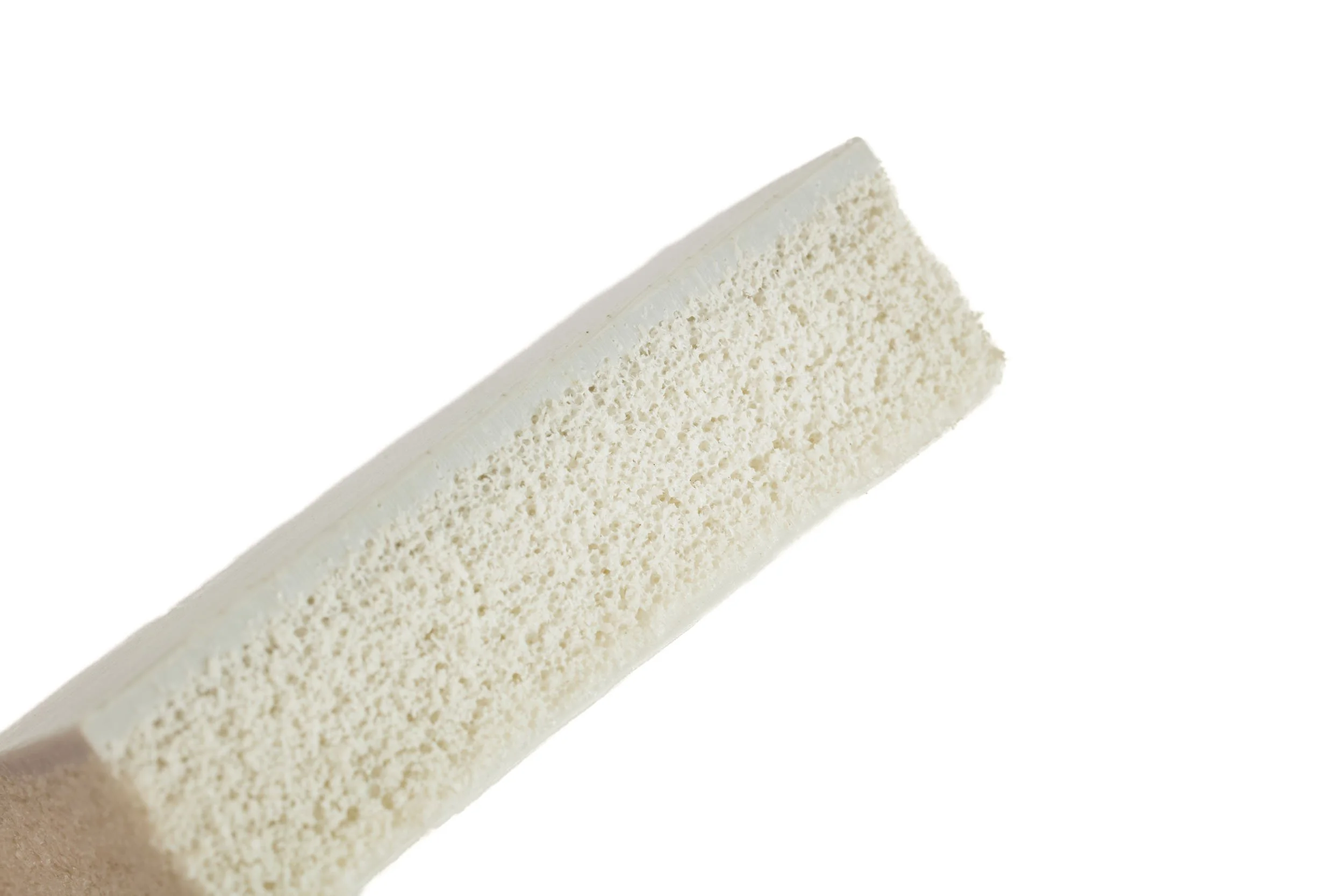

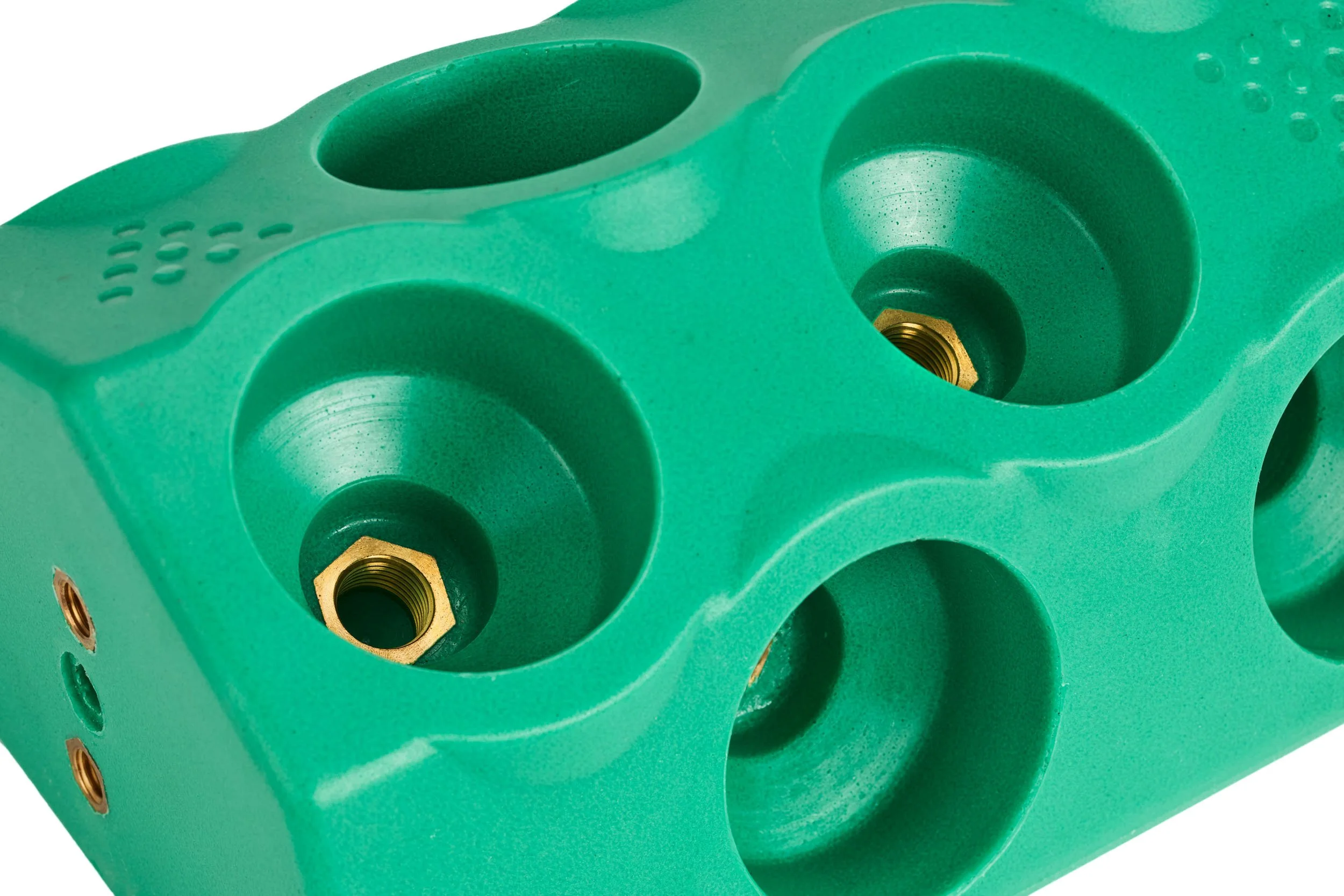

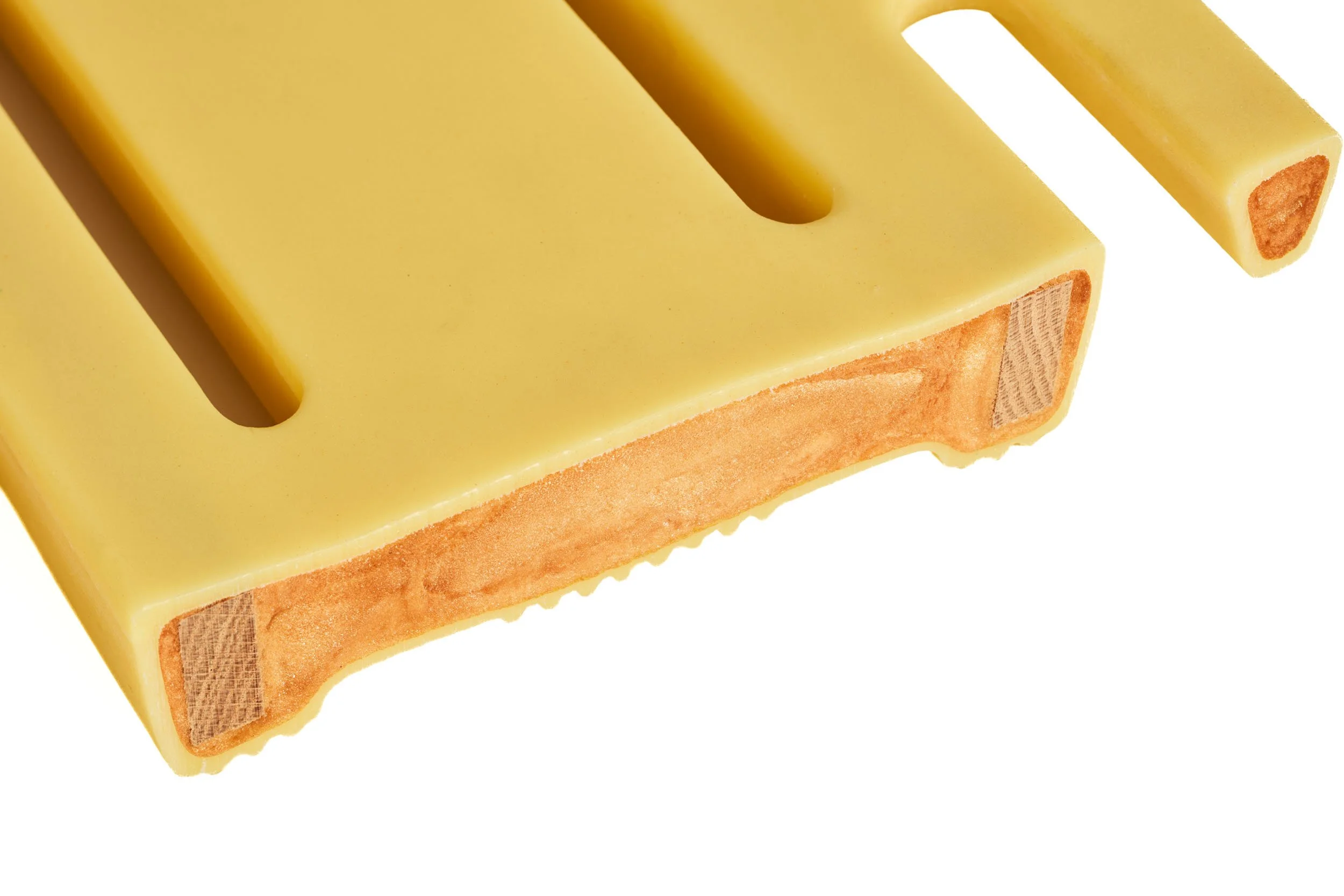


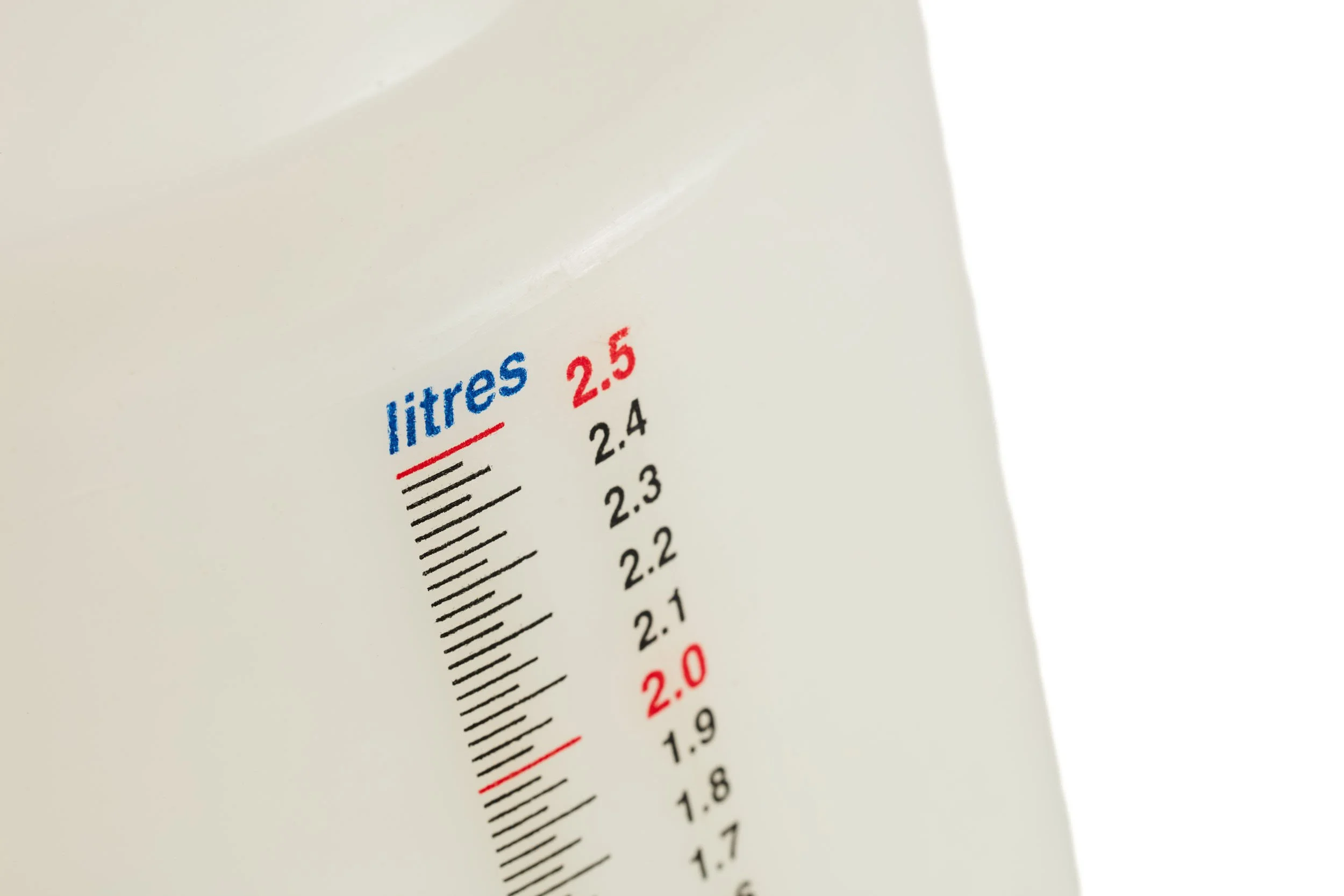
wANT to find out more?
Simply fill out the form and one of our friendly team will be in touch to assist you.